Conducting a workplace risk assessment is an essential process for maintaining a safe and healthy work environment. Risk assessments help identify potential hazards and implement measures to mitigate them. Asking the right questions during this process ensures a thorough evaluation and enables organizations to protect their employees effectively.
This article explores 10 key questions to ask in a workplace risk assessment and explains their significance in depth.
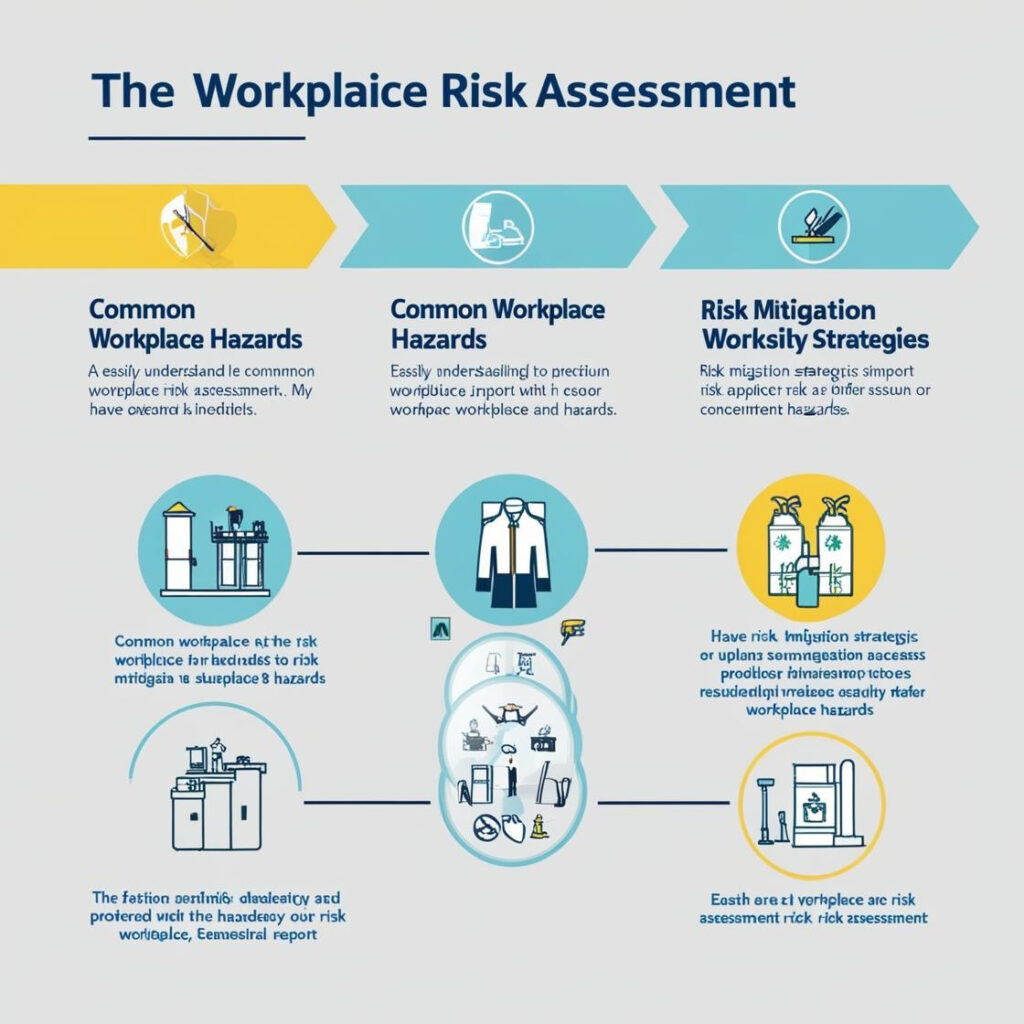
- 1. What Are the Hazards in the Workplace?
- 2. Who Might Be Harmed and How?
- 3. What Control Measures Are Already in Place?
- 4. What Additional Controls Are Needed?
- 5. What Are the Likelihood and Severity of Each Hazard?
- 6. Are Emergency Preparedness Plans in Place?
- 7. Have Employees Been Consulted?
- 8. How Will the Risks Be Monitored and Reviewed?
- 9. Are Legal and Regulatory Standards Being Met?
- 10. What Is the Plan for Communicating the Findings?
1. What Are the Hazards in the Workplace?
Identifying workplace hazards is the cornerstone of any risk assessment. Hazards can be physical, chemical, biological, or even psychosocial.
- Physical hazards: Examples include unsafe machinery, slippery floors, or ergonomic risks.
- Chemical hazards: Include exposure to hazardous substances such as cleaning agents or industrial chemicals.
- Biological hazards: Involve risks from bacteria, viruses, or mold, especially in healthcare or laboratory settings.
- Psychosocial hazards: Stress, harassment, and other mental health factors that can affect employee well-being.
Understanding all types of hazards ensures comprehensive risk coverage. Learn more about hazard identification.
2. Who Might Be Harmed and How?
This question shifts focus to people who might be affected by workplace risks, including employees, contractors, visitors, and even the public.
- Employees: Workers exposed to heavy machinery or repetitive tasks.
- Contractors: Individuals unfamiliar with workplace protocols or hazards.
- Visitors: People entering the premises without protective measures.
- Special groups: Pregnant workers, young employees, or individuals with disabilities may have unique vulnerabilities.
By identifying who might be harmed, organizations can design targeted safety measures.
3. What Control Measures Are Already in Place?
Evaluating existing controls helps identify gaps or outdated measures in current safety practices.
- Engineering controls: Are protective guards or ventilation systems functioning properly?
- Administrative controls: Are safety policies being communicated effectively?
- Personal protective equipment (PPE): Are workers using the right PPE, and is it adequate for the identified hazards?
By assessing the effectiveness of existing measures, you can determine areas for improvement. Explore best practices for PPE usage.
4. What Additional Controls Are Needed?
If existing measures are insufficient, determine what additional controls are necessary to minimize risk.
- Substitution: Replace hazardous materials or processes with safer alternatives.
- Engineering enhancements: Install barriers, alarms, or updated machinery.
- Training: Provide employees with updated training to address specific hazards.
These proactive steps not only reduce risks but also demonstrate a commitment to employee safety.
5. What Are the Likelihood and Severity of Each Hazard?
This question assesses the probability of an incident occurring and the potential consequences.
- Likelihood scale: Rank risks as unlikely, possible, or probable.
- Severity scale: Classify the impact as minor, moderate, or severe.
For example:
- A loose wire might pose a “possible” likelihood with “moderate” severity.
- Chemical spills in high-use areas could be “probable” and “severe.”
Quantifying risks helps prioritize control measures effectively.
6. Are Emergency Preparedness Plans in Place?
Emergencies such as fires, chemical spills, or natural disasters require well-developed response plans.
- Fire safety: Are extinguishers, alarms, and evacuation procedures up to date?
- First aid: Is there adequate training and availability of first-aid kits?
- Drills: Are regular drills conducted to ensure preparedness?
Having robust plans in place reduces panic and ensures a swift response during emergencies.
7. Have Employees Been Consulted?
Engaging employees in the risk assessment process provides valuable insights into potential hazards and practical solutions.
- Feedback: Workers on the ground can identify risks that may be overlooked by management.
- Participation: Involving employees fosters a culture of safety and accountability.
- Surveys: Use safety surveys to gather anonymous feedback on workplace risks.
Collaboration ensures the risk assessment is both comprehensive and relevant.
8. How Will the Risks Be Monitored and Reviewed?
Risk assessments are not static—they require regular monitoring and updates to remain effective.
- Periodic reviews: Schedule regular reviews to ensure risks are managed effectively.
- Incident reporting: Encourage employees to report near-misses and accidents promptly.
- Technology: Use safety software or apps to track and update risk assessments.
Consistent monitoring ensures that new hazards are identified and addressed promptly.
9. Are Legal and Regulatory Standards Being Met?
Compliance with local and national safety regulations is mandatory to avoid penalties and protect employees.
- Inspection readiness: Is the workplace prepared for inspections by regulatory bodies like OSHA or Canada’s CCOHS?
- Documentation: Are risk assessments documented and accessible?
- Training compliance: Ensure employees have received legally required safety training.
Staying compliant not only avoids legal issues but also strengthens workplace safety.
10. What Is the Plan for Communicating the Findings?
Once the risk assessment is complete, sharing the findings is essential for transparency and action.
- Reports: Create easy-to-understand reports for stakeholders.
- Meetings: Discuss findings during safety meetings or toolbox talks.
- Visual aids: Use posters, charts, or digital displays to communicate hazards and controls.
Clear communication ensures everyone is informed and aware of their role in maintaining safety.
Conclusion: The Importance of Asking Key Questions
Asking the 10 key questions in a workplace risk assessment ensures a thorough and actionable evaluation of potential hazards. By focusing on hazards, control measures, employee involvement, and compliance, organizations can create a safer, more productive environment.
Remember, risk assessments are ongoing processes. Regular reviews, updates, and open communication are critical for sustaining safety. Use these questions as a guide to build an effective and comprehensive risk assessment strategy.
By addressing these key questions, you not only ensure regulatory compliance but also demonstrate a commitment to employee safety and well-being.
For additional guidance, explore resources like OHSE.ca or OSHA’s guidelines.
No comments yet