Why Employers Need to Know Workplace Safety Terms
100 Workplace Safety Terms Understanding workplace safety terms is critical for employers to ensure compliance with regulations, maintain a safe working environment, and effectively communicate with employees.
Knowing these terms can help employers identify risks, implement safety measures, and foster a culture of health and well-being.
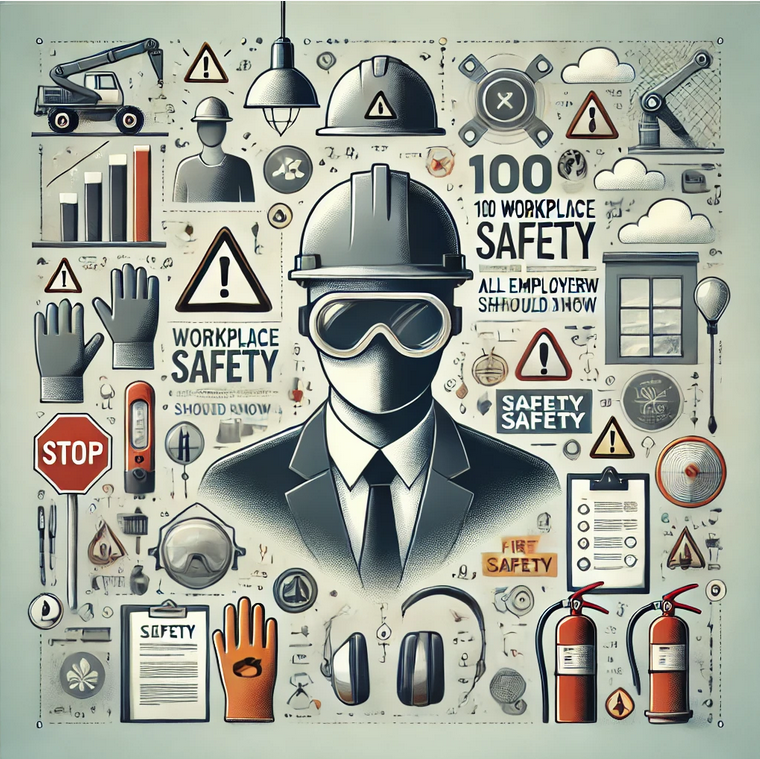
This article compiles 100 essential workplace safety terms that every employer should be familiar with.
General Safety Terms
- Accident: An unplanned event that causes injury, illness, or property damage.
- Hazard: Any source of potential harm or adverse health effect on a person.
- Risk: The likelihood of a hazard causing harm.
- Incident: An event that could lead to an accident or near miss.
- Near Miss: An incident that did not result in injury or damage but had the potential to do so.
- Occupational Health and Safety (OHS): A field focused on workplace safety and employee health.
- PPE (Personal Protective Equipment): Equipment worn to minimize exposure to hazards.
- Safety Culture: Shared attitudes and behaviors prioritizing safety in the workplace.
- Workplace Ergonomics: Designing workspaces to fit employees’ needs and reduce strain.
- Emergency Response Plan: A documented strategy for responding to emergencies like fires or chemical spills.
Regulatory and Compliance Terms
- OSHA (Occupational Safety and Health Administration): U.S. regulatory body overseeing workplace safety.
- CSA (Canadian Standards Association): Organization providing safety standards in Canada.
- ISO (International Organization for Standardization): Body setting international safety and quality standards.
- WHMIS (Workplace Hazardous Materials Information System): Canada’s system for hazard communication.
- GHS (Globally Harmonized System): International system for chemical hazard classification and labeling.
- MSDS (Material Safety Data Sheet): Document detailing chemical properties, hazards, and safety precautions.
- EHS (Environment, Health, and Safety): Management discipline ensuring compliance and employee protection.
- ANSI (American National Standards Institute): Organization overseeing voluntary workplace safety standards.
- NIOSH (National Institute for Occupational Safety and Health): U.S. research body for worker health and safety.
- Right-to-Know Law: Regulation requiring employees to be informed about workplace hazards.
Safety Equipment and Tools
- Respirator: PPE that protects against inhalation of harmful substances.
- Hard Hat: Helmet protecting against head injuries from falling objects.
- Steel-Toe Boots: Footwear with reinforced toes for impact protection.
- Gloves: Protective hand coverings made of materials like latex, leather, or Kevlar.
- High-Visibility Clothing: Bright, reflective garments to increase visibility.
- Fall Harness: Equipment preventing falls from heights.
- Lockout/Tagout (LOTO): Procedure ensuring equipment is de-energized during maintenance.
- Ear Protection: Devices like earplugs or earmuffs to guard against noise-induced hearing loss.
- Safety Goggles: Eye protection against debris, chemicals, and radiation.
- Fire Extinguisher: Device for extinguishing small fires.
Hazard Identification Terms
- Biological Hazard: Risks from bacteria, viruses, and other microorganisms.
- Chemical Hazard: Dangers posed by chemicals like acids or solvents.
- Physical Hazard: Risks from environmental factors like noise, radiation, or extreme temperatures.
- Ergonomic Hazard: Risks from poor workstation design or repetitive motions.
- Safety Hazard: Immediate threats like spills, machinery malfunctions, or sharp objects.
- Psychosocial Hazard: Risks to mental health from stress, harassment, or bullying.
- Slip, Trip, and Fall: Common accidents from uneven surfaces, spills, or obstructions.
- Confined Space: Areas with limited entry and exit points posing safety risks.
- Flammable Material: Substances that ignite easily.
- Toxic Substances: Chemicals that can cause harm through exposure.
Workplace Safety Programs
- Behavior-Based Safety (BBS): Program focusing on modifying unsafe employee behaviors.
- Safety Training: Programs teaching employees how to identify and mitigate risks.
- Incident Investigation: Process of analyzing accidents to prevent recurrence.
- Safety Audits: Inspections to ensure compliance with safety standards.
- Toolbox Talks: Informal group discussions about safety topics.
- First Aid Training: Instruction in basic emergency care techniques.
- Hazard Communication Program: System for informing employees about workplace hazards.
- Return-to-Work Program: Supporting employees recovering from workplace injuries.
- Emergency Drill: Practice sessions for responding to potential workplace emergencies.
- Risk Assessment: Identifying hazards and implementing control measures.
Emergency and Incident Terms
- Fire Drill: Practice evacuation in case of fire.
- Evacuation Plan: Procedure for safely exiting during emergencies.
- Spill Response: Plan for containing and cleaning hazardous material spills.
- CPR (Cardiopulmonary Resuscitation): Life-saving technique for cardiac arrest victims.
- AED (Automated External Defibrillator): Device for restoring heart rhythm.
- Hazmat (Hazardous Materials): Dangerous substances requiring specialized handling.
- Shelter-in-Place: Staying indoors during external hazards like chemical releases.
- First Responder: The first trained individual to address an emergency.
- Incident Command System (ICS): Framework for managing emergencies.
- Business Continuity Plan (BCP): Strategy for maintaining operations after an incident.
Advanced Safety Concepts
- Root Cause Analysis (RCA): Identifying underlying reasons for safety incidents.
- Job Safety Analysis (JSA): Breaking down tasks to identify risks.
- Control Measures: Strategies to minimize risks.
- Hazardous Energy: Sources of energy that can harm workers, like electricity.
- Exposure Limit: Maximum allowable level of exposure to hazards.
- Noise-Induced Hearing Loss (NIHL): Hearing damage from prolonged noise exposure.
- Fatigue Management: Addressing risks from worker exhaustion.
- Workplace Violence: Threats or acts of physical harm at work.
- Machine Guarding: Safety features preventing contact with moving parts.
- Environmental Monitoring: Measuring workplace factors like air quality or temperature.
Legal and Ethical Terms
- Duty of Care: Employer’s obligation to ensure employee safety.
- Negligence: Failure to meet safety responsibilities.
- Workers’ Compensation: Insurance covering work-related injuries or illnesses.
- Litigation: Legal proceedings related to workplace safety violations.
- Ethical Leadership: Leading with integrity in safety practices.
- Whistleblower Protection: Safeguarding employees who report safety violations.
- Safety Committees: Groups overseeing workplace safety initiatives.
- Employee Rights: Legal protections for workers.
- Occupational Exposure Limit (OEL): Regulatory limit for hazardous substances.
- Compliance Officer: Individual responsible for ensuring regulatory adherence.
Industry-Specific Terms
- Confined Space Entry: Procedure for entering and working in confined areas.
- Hot Work: Tasks like welding that involve heat or sparks.
- Lifting Techniques: Proper methods for manual material handling.
- Chemical Spill Kit: Supplies for addressing chemical spills.
- Scaffolding Safety: Guidelines for working on elevated platforms.
- Lockout Station: Area for storing lockout/tagout equipment.
- Respiratory Protection Program: Policies for safe respirator use.
- Asbestos Management: Handling materials containing asbestos.
- Arc Flash: Electrical explosion risks requiring specialized PPE.
- Trenching Safety: Procedures for working in excavated sites.
Emerging Safety Terms
- Smart PPE: Technology-enhanced protective equipment.
- Wearables: Devices monitoring worker safety metrics like heart rate.
- Predictive Analytics: Using data to predict and prevent incidents.
- Autonomous Safety Systems: AI-driven solutions for workplace safety.
- Virtual Reality Training: Immersive safety training simulations.
- Sustainability in Safety: Integrating eco-friendly practices into safety.
- Psychological Safety: Ensuring a mentally supportive work environment.
- Safety Apps: Mobile applications aiding workplace safety.
- Zero-Incident Philosophy: Commitment to preventing all workplace accidents.
- Digital Twins: Virtual replicas of workplaces for hazard analysis.

Familiarity with these 100 workplace safety terms empowers employers to create safer environments, enhance compliance, and protect their workforce. Staying updated on safety terminology not only reduces risks but also demonstrates a commitment to employee well-being and operational excellence.
For more in-depth resources on workplace safety, visit trusted sites like OSHA or OHSE.ca.
No comments yet