A safety manager plays a critical role in ensuring workplace safety and compliance with health and safety regulations. Safety managers are responsible for identifying risks, developing policies, and implementing procedures to protect employees.
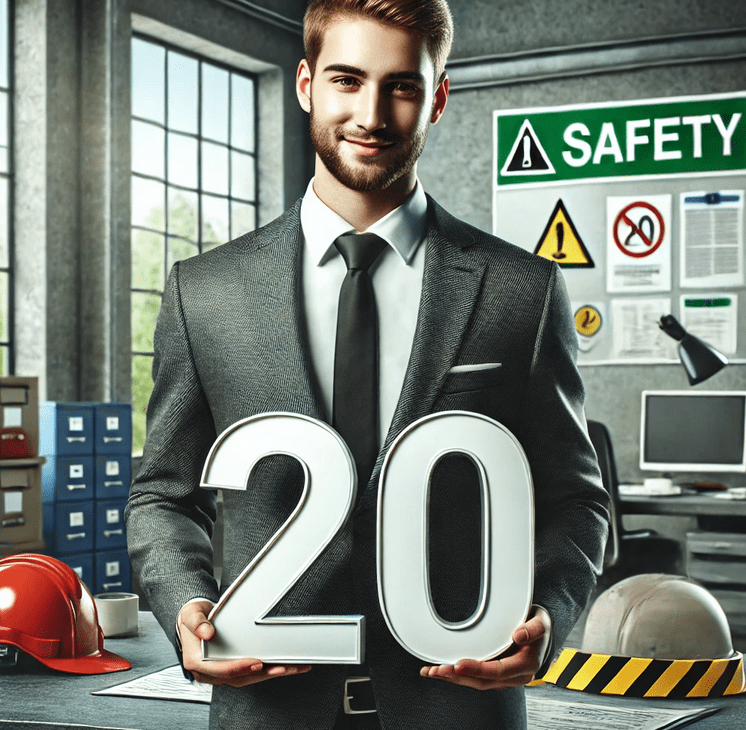
To be effective in this role, a safety manager must have a comprehensive understanding of workplace hazards, regulatory requirements, and emergency protocols.
Here are 20 key questions every safety manager should be able to answer, along with insights into their importance.
- 1. What Are the Top Hazards in Our Workplace?
- 2. How Do We Assess Risks in the Workplace?
- 3. What Are Our Key Safety Policies and Procedures?
- 4. How Do We Train Employees on Safety Practices?
- 5. How Do We Respond to an Emergency?
- 6. What Are Our Legal Responsibilities Regarding Workplace Safety?
- 7. How Do We Handle and Store Hazardous Materials?
- 8. How Do We Monitor and Improve Air Quality?
- 9. How Are Workplace Accidents and Near Misses Reported?
- 10. How Do We Enforce Lockout/Tagout (LOTO) Procedures?
- 11. What Is Our Plan for Ergonomic Safety?
- 12. How Do We Inspect and Maintain Equipment?
- 13. How Do We Promote a Culture of Safety?
- 14. How Do We Control Slips, Trips, and Falls?
- 15. How Do We Manage Noise Levels in the Workplace?
- 16. How Do We Ensure the Proper Use of Personal Protective Equipment (PPE)?
- 17. How Are We Prepared for a Fire Emergency?
- 18. How Do We Manage Stress and Mental Health in the Workplace?
- 19. How Are Safety Audits Conducted?
- 20. How Do We Handle Contractors and Temporary Workers?
1. What Are the Top Hazards in Our Workplace?
A safety manager must be able to identify the specific hazards associated with their workplace. Whether it’s chemical exposure, machinery risks, or ergonomic issues, knowing the top hazards allows for effective risk management.
Why It Matters:
Understanding the hazards is the first step in mitigating risks and developing targeted safety measures.
2. How Do We Assess Risks in the Workplace?
Risk assessments are a fundamental tool for identifying and evaluating potential hazards. A safety manager must explain how risks are assessed and prioritized for mitigation.
Why It Matters:
Accurate risk assessments allow for proactive safety planning and help prevent accidents before they occur.
3. What Are Our Key Safety Policies and Procedures?
Safety policies and procedures outline how hazards are controlled and how employees are protected. A safety manager should know all relevant safety protocols and ensure they are communicated clearly to staff.
Why It Matters:
Employees need clear guidance on how to work safely and respond to emergencies. Strong policies provide a framework for compliance and accountability.
4. How Do We Train Employees on Safety Practices?
Training is critical to ensuring that employees understand safety protocols. A safety manager must be able to explain how training programs are designed, delivered, and updated.
Why It Matters:
Regular and comprehensive training helps employees stay informed about the latest safety procedures and reduces workplace accidents.
5. How Do We Respond to an Emergency?
Every safety manager should know the company’s emergency response plan, including evacuation procedures, first aid protocols, and the roles of key personnel.
Why It Matters:
A clear and effective emergency response plan can save lives in critical situations like fires, chemical spills, or natural disasters.
6. What Are Our Legal Responsibilities Regarding Workplace Safety?
Understanding legal responsibilities is essential to ensure compliance with occupational health and safety (OHS) laws and regulations. A safety manager must know the relevant laws that apply to their industry.
Why It Matters:
Failure to comply with safety regulations can result in legal penalties, fines, or even criminal charges, as well as reputational damage.
7. How Do We Handle and Store Hazardous Materials?
If your workplace involves hazardous substances, a safety manager must be knowledgeable about how these materials are stored, handled, and disposed of safely.
Why It Matters:
Proper management of hazardous materials prevents accidents, such as spills, fires, or exposure to toxic chemicals.
8. How Do We Monitor and Improve Air Quality?
Indoor air quality is a critical factor for worker health. A safety manager must ensure that ventilation systems are functioning properly and that air quality is regularly monitored.
Why It Matters:
Poor air quality can lead to respiratory issues and decrease productivity, especially in environments with dust, fumes, or chemicals.
9. How Are Workplace Accidents and Near Misses Reported?
An effective reporting system ensures that accidents and near misses are documented and investigated. A safety manager should have a process in place for tracking incidents and implementing corrective actions.
Why It Matters:
Learning from near misses and accidents helps prevent future incidents and improves overall workplace safety.
10. How Do We Enforce Lockout/Tagout (LOTO) Procedures?
Lockout/Tagout procedures are essential for ensuring that machinery is safely de-energized before maintenance. A safety manager should enforce these procedures and train employees on proper LOTO practices.
Why It Matters:
LOTO procedures prevent accidental machinery start-up, which can result in severe injuries or fatalities.
11. What Is Our Plan for Ergonomic Safety?
Ergonomic safety focuses on reducing the risk of musculoskeletal disorders caused by repetitive tasks, improper lifting, or poor workstation design. A safety manager should know the ergonomic risks and implement solutions to minimize them.
Why It Matters:
Ergonomic injuries are one of the leading causes of workplace-related health issues, affecting productivity and employee well-being.
12. How Do We Inspect and Maintain Equipment?
Regular inspections and maintenance of machinery and equipment are vital for preventing malfunctions that could lead to accidents. A safety manager should oversee these inspections and ensure that maintenance schedules are followed.
Why It Matters:
Preventive maintenance reduces the likelihood of equipment failure and keeps workers safe.
13. How Do We Promote a Culture of Safety?
A strong safety culture ensures that safety is a priority for everyone in the organization. A safety manager should have strategies for promoting safety awareness and encouraging employees to follow protocols.
Why It Matters:
A proactive safety culture leads to fewer accidents, higher compliance rates, and a more engaged workforce.
14. How Do We Control Slips, Trips, and Falls?
Slips, trips, and falls are among the most common workplace accidents. A safety manager must be able to identify the causes of these incidents and implement measures to prevent them.
Why It Matters:
Preventing falls can significantly reduce workplace injuries, especially in environments where workers are at risk of slipping or tripping.
15. How Do We Manage Noise Levels in the Workplace?
Excessive noise can cause hearing loss and contribute to fatigue and stress. A safety manager should monitor noise levels and ensure that hearing protection is available where necessary.
Why It Matters:
Noise-induced hearing loss is a preventable workplace injury, and reducing noise levels improves overall worker comfort and health.
16. How Do We Ensure the Proper Use of Personal Protective Equipment (PPE)?
PPE is a key component of workplace safety, and a safety manager must ensure that employees have the necessary protective gear and know how to use it correctly.
Why It Matters:
Proper use of PPE reduces exposure to hazards and prevents injuries from occurring.
17. How Are We Prepared for a Fire Emergency?
A safety manager should ensure that fire safety equipment, such as extinguishers and alarms, is regularly inspected and that employees are trained on evacuation routes and procedures.
Why It Matters:
Fires can be devastating, but proper preparedness can minimize damage and ensure that everyone evacuates safely.
18. How Do We Manage Stress and Mental Health in the Workplace?
Workplace stress and poor mental health can lead to decreased productivity, burnout, and increased accident risk. A safety manager should promote mental health initiatives and provide resources to help employees manage stress.
Why It Matters:
A healthy workforce is more productive, and addressing mental health issues helps prevent absenteeism and presenteeism.
19. How Are Safety Audits Conducted?
Regular safety audits help identify weaknesses in safety protocols and ensure compliance with regulations. A safety manager must lead these audits and develop action plans based on the findings.
Why It Matters:
Safety audits provide valuable insights into areas of improvement and help prevent accidents.
20. How Do We Handle Contractors and Temporary Workers?
Contractors and temporary workers may not be as familiar with your workplace’s safety protocols. A safety manager should ensure that they receive adequate safety training and are aware of all relevant risks.
Why It Matters:
Ensuring that all workers, regardless of employment status, are aware of safety protocols helps prevent accidents and maintains a safe working environment.
A safety manager must be well-versed in all aspects of workplace safety, from identifying hazards to implementing safety procedures.
By being able to answer these 20 essential questions, a safety manager can ensure that the workplace remains safe, compliant with regulations, and prepared for emergencies. A proactive approach to safety not only protects workers but also enhances productivity and organizational reputation.
No comments yet