The integration of 3D Printing in Safety practices is revolutionizing the production of custom safety gear and equipment.
By leveraging the versatility and precision of 3D printing technology, organizations can address specific workplace safety challenges, enhance employee protection, and promote innovation in safety solutions.

- The Rise of 3D Printing in Safety
- Applications of 3D Printing in Safety Gear
- Innovative Materials in 3D Printing
- Sustainability and 3D Printing in OHSE
- Challenges and Considerations
- Future of 3D Printing in OHSE
- How does 3D printing enhance ergonomics?
- How does 3D printing reduce costs?
- What industries benefit most from 3D printing?
- How does 3D printing improve customization?
- Final Thoughts
The Rise of 3D Printing in Safety
3D printing, or additive manufacturing, enables the creation of complex designs by layering materials based on digital models. In the OHSE sector, this technology is being increasingly utilized to produce tailor-made safety equipment that meets unique requirements.
Benefits of 3D Printing in OHSE
- Customization: Allows the creation of gear tailored to individual worker needs.
- Cost-Effectiveness: Reduces production costs by minimizing material waste.
- Rapid Prototyping: Enables quick testing and iteration of safety designs.
Benefit | Impact |
---|---|
Customization | Improved fit and comfort for workers |
Cost-Effectiveness | Affordable production of safety gear |
Rapid Prototyping | Accelerated innovation cycles |
Pro Tip: Use 3D printing to test new designs for safety equipment before mass production.
Applications of 3D Printing in Safety Gear
1. Custom-Fit PPE (Personal Protective Equipment)
3D printing excels in producing custom-fit PPE, such as helmets, masks, and gloves, that adapt to individual worker measurements.
- Helmets: Tailor helmet designs to provide better comfort and reduce strain.
- Masks: Create masks with personalized fittings to ensure maximum protection.
- Gloves: Produce ergonomic gloves designed for specific tasks or industries.
For tips on selecting PPE, check out our Comprehensive PPE Guide.
2. Ergonomic Tools and Equipment
The technology facilitates the creation of tools and equipment that enhance worker comfort and efficiency.
- Anti-Fatigue Handles: Design handles that reduce hand strain during repetitive tasks.
- Lightweight Materials: Use 3D printing to produce lightweight yet durable equipment.
- Tool Customization: Adapt tools for specialized tasks in industries like construction and healthcare.
Explore ergonomic tool designs at Amazon.
3. Prototyping and Testing Safety Devices
3D printing enables rapid prototyping of new safety devices, allowing organizations to test designs in real-world scenarios.
- Prototypes: Produce working models of safety innovations for evaluation.
- Design Iteration: Modify and refine designs based on feedback.
- Field Testing: Test prototypes in specific workplace environments.
Innovative Materials in 3D Printing
4. Advanced Materials for Safety Gear
The development of advanced materials for 3D printing has expanded its applications in OHSE.
- Impact-Resistant Plastics: Ideal for creating durable helmets and shields.
- Flexible Polymers: Suitable for producing comfortable gloves and masks.
- Biodegradable Materials: Promote sustainability in safety gear production.
Material | Application |
Impact-Resistant Plastics | Helmets, shields |
Flexible Polymers | Gloves, masks |
Biodegradable Materials | Eco-friendly PPE |
Pro Tip: Combine advanced materials with innovative designs to maximize safety and efficiency.
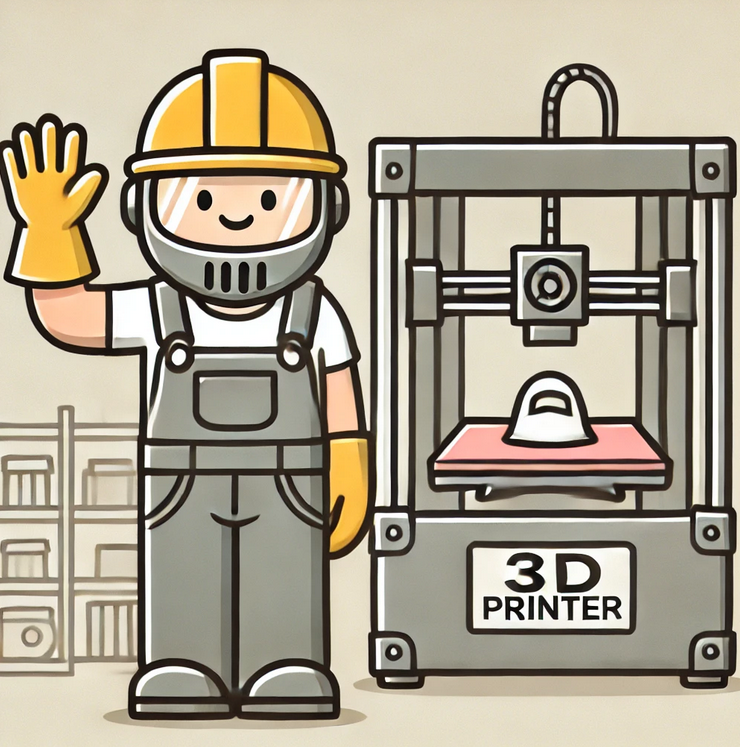
Sustainability and 3D Printing in OHSE
5. Reducing Environmental Impact
3D printing offers eco-friendly benefits by minimizing waste and promoting sustainable practices.
- Material Efficiency: Uses only the required amount of material, reducing waste.
- Recyclable Materials: Enables the use of recycled or reusable materials.
- Localized Production: Reduces carbon footprint by producing gear on-site or nearby.
Challenges and Considerations
6. Addressing Limitations of 3D Printing
While 3D printing offers significant advantages, there are challenges to consider.
- Material Limitations: Some materials may lack durability for high-risk environments.
- Cost of Entry: Initial investment in 3D printers and software can be high.
- Regulatory Compliance: Ensuring printed gear meets safety standards is crucial.
Read our guide on navigating Safety Standards in Emerging Technologies.
7. Ensuring Quality Control
Maintaining consistent quality in 3D-printed safety gear is essential to ensure worker protection.
- Standardized Testing: Subject printed equipment to rigorous safety tests.
- Certification: Obtain certifications for 3D-printed gear from recognized authorities.
- Regular Inspections: Monitor wear and tear on printed equipment to ensure ongoing safety.
Future of 3D Printing in OHSE
The future of 3D printing in OHSE is bright, with ongoing advancements in materials, printing techniques, and integration with other technologies.
8. Integration with Smart Technology
Combine 3D printing with smart technologies to create intelligent safety gear.
- Sensors: Embed sensors in helmets or gloves to monitor worker health.
- Connectivity: Enable real-time data sharing for proactive hazard management.
- AI Integration: Use AI to analyze safety data and improve designs.
9. Expanding Applications
The versatility of 3D printing allows for endless possibilities in OHSE applications.
- Emergency Equipment: Produce customized tools for disaster response.
- Training Simulators: Create realistic models for safety training exercises.
- Replacement Parts: Manufacture spare parts for safety systems on demand.
Pro Tip: Invest in research and development to explore new ways to utilize 3D printing in OHSE.
How does 3D printing enhance ergonomics?
3D printing enhances ergonomics by enabling the creation of highly customized tools, equipment, and personal protective gear that align precisely with individual worker needs. Here’s how:
Customization for Individual Fit
- Personalized Safety Gear:
- 3D scanning technology allows for creating PPE like helmets, gloves, and masks tailored to the exact dimensions of a worker’s body, ensuring a snug and comfortable fit.
- This reduces discomfort and the risk of injuries caused by ill-fitting equipment.
- Ergonomic Tool Designs:
- Tools can be 3D-printed with handles and grips specifically shaped for a worker’s hand size and usage patterns, minimizing strain during repetitive tasks.
Improved Material and Weight Distribution
- Lightweight Designs:
- 3D printing uses advanced materials like lightweight polymers, reducing the overall weight of tools and gear without compromising durability.
- Lightweight equipment eases fatigue, especially for workers in physically demanding roles.
- Optimized Balance:
- Tools and equipment can be designed with precise weight distribution, making them easier to handle and reducing the risk of repetitive strain injuries.
Rapid Prototyping for Ergonomic Testing
- Prototyping for Comfort:
- Designers can quickly produce and test prototypes of ergonomic designs, collecting user feedback to refine the final product.
- This iterative process ensures that the final product is both functional and comfortable.
- Cost-Effective Adjustments:
- Adjustments to ergonomic designs can be made efficiently and affordably, enabling ongoing improvements without significant production delays.
Enhanced Worker Productivity and Safety
- Minimized Physical Strain:
- Properly fitted tools and gear reduce stress on joints and muscles, allowing workers to perform tasks more efficiently with less fatigue.
- Injury Prevention:
- Ergonomic designs decrease the likelihood of workplace injuries, such as carpal tunnel syndrome or back strain, caused by poorly designed tools or equipment.
By integrating 3D printing into workplace safety and design, organizations can create ergonomic solutions that cater to diverse worker needs, improving both comfort and productivity.
How does 3D printing reduce costs?
3D printing reduces costs across various stages of production and operations, making it an increasingly popular choice for industries prioritizing efficiency and cost-effectiveness. Here’s how it achieves this:
1. Reduces Material Waste
- Precision Manufacturing:
- 3D printing uses additive manufacturing, where material is layered precisely to create the desired object. This eliminates the waste associated with subtractive methods like cutting or machining.
- Less waste means lower costs for raw materials, particularly for expensive materials like metals or advanced polymers.
- Optimized Material Usage:
- Designs are optimized to use only the material required for structural integrity, further minimizing waste.
2. Lowers Production Costs
- On-Demand Manufacturing:
- Parts and equipment can be printed as needed, reducing the need for large inventories. This avoids costs associated with storage and overproduction.
- Tool-Free Production:
- Traditional manufacturing often requires expensive molds or tools for production. 3D printing eliminates these requirements, especially for short production runs or custom orders.
3. Enables Rapid Prototyping
- Cost-Effective Prototypes:
- 3D printing allows businesses to create and test prototypes quickly without investing in expensive tooling or setup processes.
- Fewer Design Iterations:
- With quick prototyping, errors can be identified and fixed early, reducing the need for multiple expensive iterations.
4. Shortens Production Time
- Streamlined Processes:
- 3D printers can produce complex parts in one go, eliminating the need for multiple assembly steps and reducing labor costs.
- Faster Time to Market:
- Companies can accelerate product development cycles, reducing costs associated with lengthy development timelines.
5. Localized Manufacturing
- Reduces Shipping Costs:
- 3D printing enables localized production, reducing the costs of transporting goods from centralized manufacturing facilities to end-users.
- On-Site Repairs:
- Spare parts can be printed on-site, reducing downtime and costs associated with ordering and shipping replacement components.
6. Customization at Scale
- Cost-Efficient Customization:
- Producing custom items traditionally requires separate molds or processes for each variation. With 3D printing, customization comes at little to no additional cost.
- Mass Customization:
- Businesses can offer personalized products without the need for separate production lines, saving significantly on setup costs.
7. Simplifies Supply Chains
- Inventory Reduction:
- Digital files replace physical inventory, allowing businesses to store designs rather than products, saving warehousing costs.
- Fewer Suppliers:
- With 3D printing, multiple components can be consolidated into a single part, reducing reliance on multiple suppliers.
By integrating 3D printing into their operations, businesses can achieve significant cost savings while maintaining flexibility and innovation, making it a transformative tool for modern industries.
What industries benefit most from 3D printing?
3D printing is a transformative technology benefiting numerous industries by enabling cost-effective production, customization, and innovation. Here are the industries that benefit most from 3D printing and how it impacts them:
1. Healthcare and Medicine
- Custom Prosthetics and Orthotics:
- 3D printing allows the creation of patient-specific prosthetics, orthotics, and implants, improving comfort and functionality.
- Surgical Tools and Models:
- Surgeons use 3D-printed anatomical models for preoperative planning and training, enhancing surgical precision.
- Bioprinting:
- Emerging applications include printing tissues and organs for research and, potentially, transplantation.
Example Impact:
Reduced costs and lead times for prosthetics, enabling broader access to life-changing devices.
2. Aerospace and Defense
- Lightweight Components:
- Aerospace companies use 3D printing to produce lightweight, high-strength parts, improving fuel efficiency.
- Complex Geometries:
- The technology creates intricate components, such as turbine blades and engine parts, that are difficult to manufacture traditionally.
- Rapid Prototyping:
- Defense contractors use 3D printing for quick iterations of new designs, accelerating innovation.
Example Impact:
Reduced weight of aircraft components, saving fuel costs and enhancing performance.
3. Automotive
- Prototyping and Testing:
- Car manufacturers use 3D printing to rapidly create prototypes and test new designs without the need for costly tooling.
- Custom and Spare Parts:
- Classic car restorations and performance tuning benefit from 3D-printed parts that are no longer available or need customization.
- Tooling and Jigs:
- Factories use 3D printing to produce custom tools, reducing costs and improving efficiency.
Example Impact:
Shorter product development cycles and enhanced customization options for vehicles.
4. Consumer Goods and Retail
- Personalized Products:
- 3D printing enables mass customization, such as personalized shoes, jewelry, and eyewear, catering to individual customer preferences.
- Rapid Design Changes:
- Designers can quickly iterate and produce new products based on market trends.
- Eco-Friendly Practices:
- Producing on demand minimizes waste and reduces overproduction.
Example Impact:
Better customer satisfaction through personalization and faster response to changing market demands.
5. Construction and Architecture
- 3D-Printed Buildings:
- Entire structures, from homes to office buildings, can be constructed using large-scale 3D printers, reducing material waste and costs.
- Intricate Models:
- Architects use 3D printing to create detailed models of designs, enhancing client presentations and planning.
- Custom Components:
- Custom fixtures and components, like decorative panels, can be produced more affordably.
Example Impact:
Faster and cheaper housing solutions with reduced environmental impact.
6. Education and Research
- Hands-On Learning:
- Educational institutions use 3D printing for STEM education, allowing students to create and test prototypes.
- Research Applications:
- Researchers across fields utilize 3D printing for testing theories, producing models, and developing innovative solutions.
Example Impact:
Enhanced learning experiences and accelerated research development.
7. Fashion and Jewelry
- Customized Accessories:
- Jewelry designers use 3D printing to create intricate, custom pieces with minimal waste.
- Sustainable Fashion:
- Clothing and accessories are being 3D-printed using eco-friendly materials, reducing the environmental footprint.
- Rapid Prototyping:
- Designers can quickly iterate designs, speeding up the production cycle.
Example Impact:
Affordable customization and sustainable practices in the fashion industry.
8. Manufacturing
- Tooling and Molds:
- Manufacturers use 3D printing to create custom molds and tools, streamlining production lines.
- Low-Volume Production:
- Ideal for small production runs of highly specialized products or parts.
- Spare Parts on Demand:
- Instead of stocking large inventories, spare parts can be printed as needed.
Example Impact:
Reduced downtime and costs in industrial production processes.
9. Energy and Utilities
- Renewable Energy Components:
- 3D printing is used to create wind turbine parts and solar panel components more efficiently.
- Oil and Gas Industry:
- Custom parts for pipelines and machinery are produced quickly to minimize downtime.
- Nuclear Power:
- The technology produces intricate parts for reactors that require high precision.
Example Impact:
Improved efficiency and reduced costs in energy production and distribution.
10. Art and Entertainment
- Props and Set Designs:
- 3D printing allows rapid creation of intricate props and sets for movies, theater, and video games.
- Art Installations:
- Artists use 3D printing for creating complex sculptures and innovative art pieces.
- Gaming Accessories:
- Custom controllers, miniatures, and replicas are produced to enhance user experiences.
Example Impact:
Unprecedented creativity and reduced production costs for the entertainment industry.
Why 3D Printing Matters Across Industries
3D printing provides industries with unparalleled flexibility, cost savings, and the ability to innovate. Its applications are continually expanding as technology advances, ensuring its impact across sectors remains transformative.
How does 3D printing improve customization?
3D printing significantly improves customization by enabling the creation of unique, tailored products and components that precisely meet individual or specific requirements. Here’s how:
1. Tailored to Individual Needs
- Personalized Designs:
- 3D printing uses digital models to create custom-fitted items, such as prosthetics, orthotics, and personal protective equipment (PPE).
- Scanning technologies like 3D scanning capture exact measurements, ensuring a perfect fit for the user.
- Healthcare Applications:
- For example, dental implants, hearing aids, and orthopedic devices can be printed to fit the unique anatomy of patients.
2. Complexity Without Extra Costs
- No Added Costs for Complexity:
- Traditional manufacturing methods often increase in cost with complexity, but 3D printing handles intricate designs without additional tooling or labor costs.
- Complex geometries, such as lattice structures or internal channels, can be produced as easily as simple shapes.
- Custom Components:
- Industries like aerospace and automotive benefit by producing lightweight, intricate parts optimized for performance and efficiency.
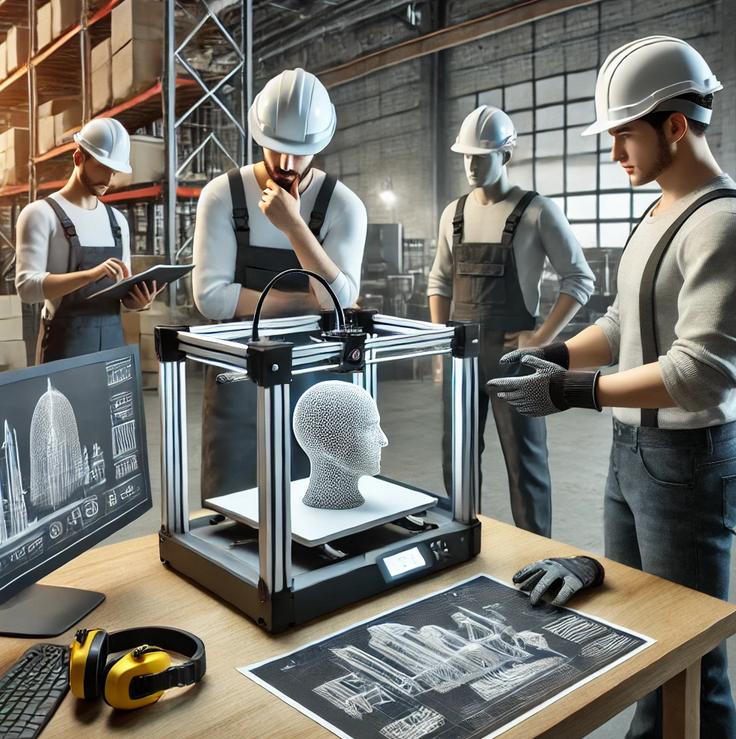
3. On-Demand Customization
- Localized Manufacturing:
- Products can be printed on-site or close to the end-user, reducing lead times and transportation costs.
- This is particularly useful for creating spare parts or tools in remote or specialized settings.
- Rapid Adjustments:
- Designs can be modified quickly in the digital phase, allowing businesses to respond to customer feedback or evolving needs with minimal delay.
4. Mass Customization
- Economies of Customization:
- Unlike traditional mass production, where identical items are created in large quantities, 3D printing allows for mass customization.
- Companies can produce unique variations of products, such as shoes, jewelry, or eyewear, tailored to individual customer preferences without retooling costs.
- Fashion and Retail:
- Brands use 3D printing to create personalized items, like customized athletic footwear or bespoke fashion accessories.
5. Prototyping and Design Iteration
- Rapid Prototyping:
- Designers can quickly create prototypes, test them, and make adjustments in real time, ensuring that the final product meets specific requirements.
- This iterative process is particularly beneficial in industries like architecture, where customized scale models are required.
- Feedback Integration:
- End-users can be involved in the design process, providing input that results in products perfectly tailored to their needs.
6. Improved Ergonomics
- User-Specific Features:
- Tools and equipment can be customized for individual comfort and usage patterns, reducing strain and improving usability.
- For example, custom ergonomic handles for tools can minimize worker fatigue and repetitive strain injuries.
- Adaptive Design:
- 3D printing allows for the production of items that adapt to changing user needs, such as modular furniture or adjustable equipment.
7. Reduced Waste in Custom Production
- Material Efficiency:
- Traditional customization methods often involve cutting or reshaping materials, leading to waste.
- 3D printing adds material layer by layer, using only what’s needed for the specific design.
- Eco-Friendly Practices:
- This approach supports sustainable manufacturing by reducing excess material usage, particularly for single-use or disposable custom items.
8. Applications Across Industries
- Healthcare: Prosthetics, implants, and surgical models tailored to patient anatomy.
- Automotive: Custom car parts and personalized interiors.
- Consumer Goods: One-of-a-kind jewelry, fashion items, and electronics.
- Education: Tailored teaching tools and student-specific learning aids.
- Entertainment: Unique props and costumes designed for individual projects.
Why Customization Matters with 3D Printing
3D printing empowers businesses and individuals to create products that meet precise requirements, offering unprecedented flexibility and personalization. This ability to combine efficiency with uniqueness is transforming industries and enhancing user satisfaction.
Final Thoughts
3D printing is transforming the OHSE landscape by enabling the creation of custom safety gear and equipment tailored to specific workplace needs.
By leveraging advanced materials, sustainable practices, and innovative designs, organizations can enhance worker safety and drive technological progress. As this technology continues to evolve, its applications in OHSE are set to expand, making workplaces safer and more efficient.
No comments yet