Personal Protective Equipment (PPE) is a critical tool for maintaining workplace safety, acting as the final barrier between workers and potential hazards.
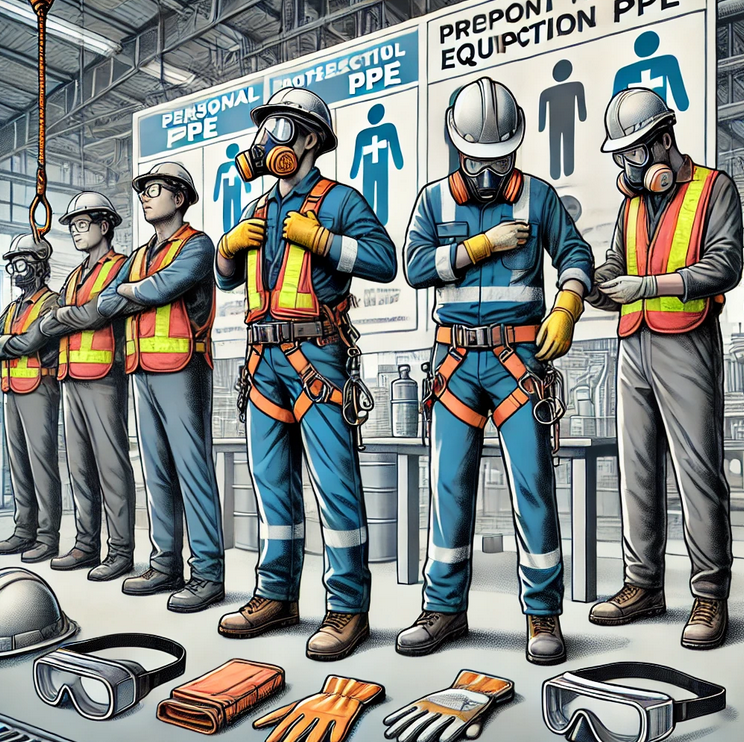
However, common PPE mistakes can undermine its effectiveness, putting workers at risk. This article examines these mistakes and provides actionable strategies to avoid them, ensuring PPE serves its intended purpose effectively.
Choosing the Wrong PPE
One of the most frequent mistakes is using the wrong type of PPE for a specific task. For example, wearing gloves designed for chemical protection while handling sharp objects may result in cuts or injuries. Similarly, using safety glasses instead of goggles in environments with splash risks can expose the eyes to hazards.
To address this, organizations must conduct thorough hazard assessments to determine the appropriate PPE for each job. Providing a range of PPE options tailored to different workplace risks ensures employees have access to the right equipment for their tasks.
Improper Fit of PPE
Another prevalent issue is the improper fit of PPE. Ill-fitting equipment, such as loose helmets that can fall off or oversized gloves that reduce dexterity, compromises both safety and comfort. Poor fit can also lead to non-compliance, as workers may find ill-fitting PPE too cumbersome to wear consistently.
Employers should offer PPE in various sizes and conduct fitting sessions to ensure all employees have gear that fits correctly. Adjustments for individual needs, such as straps for helmets or adjustable respirators, can further enhance the fit and usability of PPE.
Lack of Training on PPE Usage
Even the best PPE is ineffective if employees do not know how to use it properly. A common example is workers failing to seal respirators correctly, allowing harmful particles to bypass the protection. Similarly, mishandling earplugs or improperly donning safety harnesses can negate their protective benefits.
Comprehensive training programs are essential. These should include practical demonstrations, hands-on practice, and clear instructions on correct usage, maintenance, and storage. Periodic refresher courses can reinforce proper practices and address any gaps in knowledge.
Failure to Inspect PPE Regularly
PPE can degrade over time, and using damaged equipment is a common mistake. Cracked helmets, torn gloves, or clogged respirator filters fail to provide adequate protection, leaving workers vulnerable to hazards.
To mitigate this risk, organizations should establish routine inspection protocols. Employees should check their PPE before each use for visible signs of damage, and employers should schedule periodic comprehensive inspections. Any equipment showing signs of wear or damage must be replaced immediately.
Neglecting PPE Maintenance
Failing to clean and maintain PPE can significantly reduce its lifespan and effectiveness. For instance, dirty respirators can become clogged, and unwashed gloves may harbor harmful substances that could irritate the skin.
Regular maintenance routines, including cleaning and proper storage, are crucial. Employees should be trained on these routines, and employers should provide the necessary cleaning supplies and facilities. PPE should be stored in clean, dry areas away from exposure to chemicals, moisture, or excessive sunlight.
Over-Reliance on PPE
While PPE is essential, it should not be the sole safety measure. A common mistake is using PPE as the first line of defense instead of implementing engineering controls, administrative measures, or safer work practices.
Employers should adopt a hierarchy of controls, with PPE as the last resort. For example, instead of relying solely on respirators in a dusty environment, installing proper ventilation systems reduces the reliance on PPE while creating a safer workspace.
Benefits of Addressing PPE Mistakes
Correcting common PPE mistakes has far-reaching benefits. Employees are better protected from workplace hazards, reducing injury rates and improving overall safety. Organizations also benefit through increased productivity, reduced downtime due to injuries, and lower costs related to workers’ compensation and regulatory fines. Additionally, maintaining a strong safety culture enhances employee morale and fosters trust in management.
External Resources for Further Learning
For more information on PPE standards and best practices, visit OSHA’s PPE page or NIOSH’s guide to PPE. These resources offer detailed guidelines for implementing effective PPE programs.
Internal Links for Additional Insights
Learn more about creating a safe work environment in our guide on Hazard Identification and Risk Assessment. For insights on fostering a culture of safety, check out our article on Safety Committees in Organizations.
By addressing these common PPE mistakes and implementing the suggested solutions, organizations can enhance workplace safety, protect their employees, and foster a culture of responsibility and compliance. Proper PPE use is not just a regulatory requirement but a fundamental aspect of employee well-being and operational success.
No comments yet