Behavior-Based Safety (BBS) is a process-driven approach to improving workplace safety by focusing on the behaviors of employees rather than relying solely on traditional hazard identification and control.
It promotes a proactive culture where workers observe, report, and adjust unsafe actions before they lead to accidents.
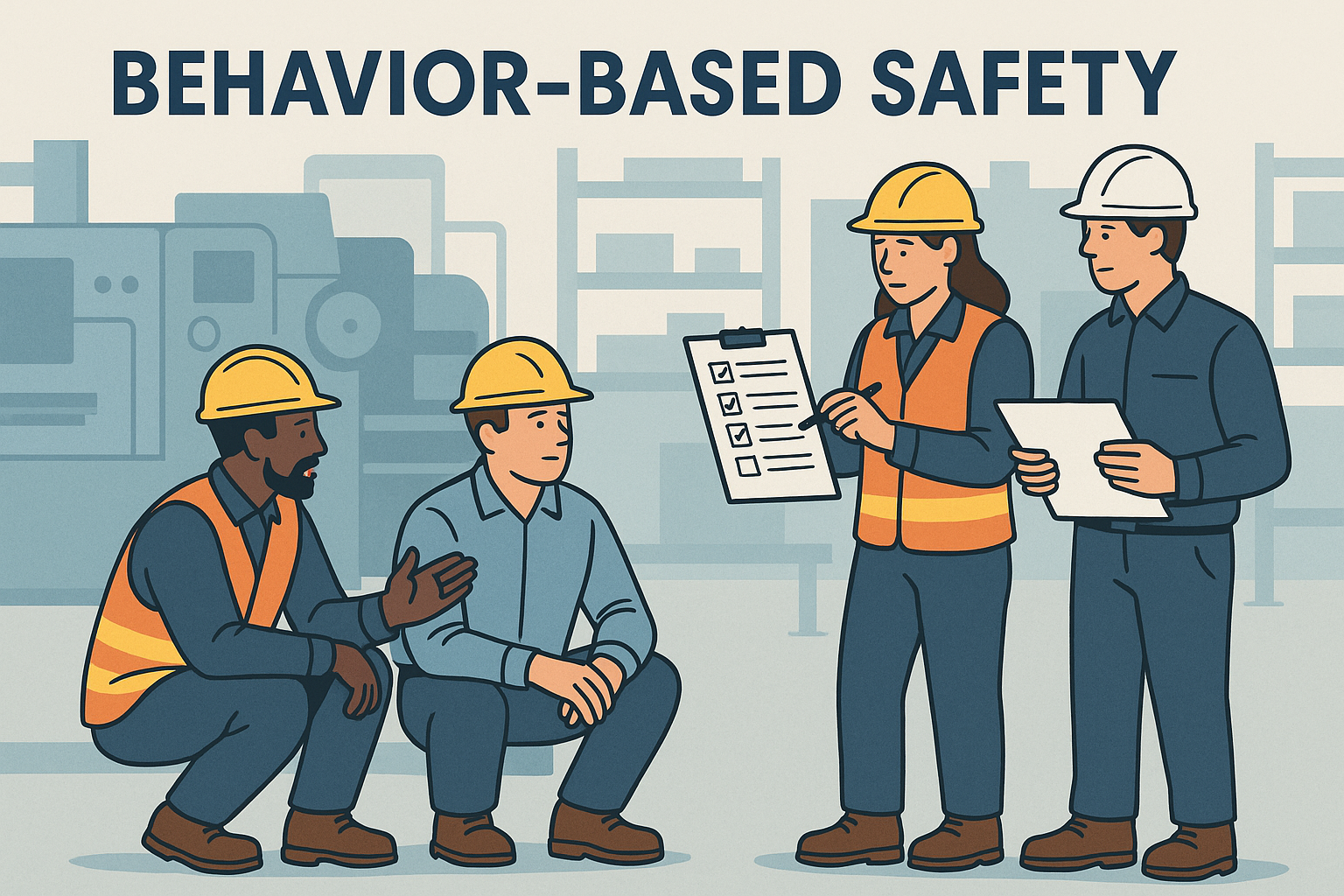
The philosophy behind BBS is grounded in behavioral science: by understanding why people act the way they do in certain workplace environments, organizations can design better safety interventions. The core principle is simple—identify critical behaviors, observe them regularly, give constructive feedback, and reinforce safe actions.
BBS gained popularity in the 1990s as companies began shifting from compliance-only strategies to more human-centered approaches to safety.
- Core Elements of a Behavior-Based Safety Program
- Why Do Companies Use Behavior-Based Safety?
- But Does Behavior-Based Safety Really Work?
- Common Criticisms of Behavior-Based Safety
- Key Conditions for Effective BBS Implementation
- Behavior-Based Safety vs. Other Approaches
- Best Practices for a Behavior-Based Safety Program
- Real-Life Example: BBS in Action
- The Future of Behavior-Based Safety
- Conclusion: Does Behavior-Based Safety Work?
- Resources and Further Reading
Core Elements of a Behavior-Based Safety Program
A successful BBS program typically includes:
- Defined Critical Behaviors: Based on job safety analysis (JSA) and risk assessments
- Peer Observations: Workers observe each other using checklists and safety guides
- Immediate Feedback: Observers provide instant, respectful feedback
- Data Collection & Analysis: Trends in behaviors are tracked and addressed
- Recognition: Positive reinforcement of safe actions
- Employee Involvement: Full participation from frontline workers to leadership
This creates a feedback loop that empowers employees and builds a strong safety culture—one where safety isn’t enforced to them, but practiced by them.
Why Do Companies Use Behavior-Based Safety?
1. Reduces Incident Rates
BBS helps identify behaviors that lead to near-misses or injuries. A reduction in these behaviors often correlates to fewer incidents.
For instance, a major logistics company using BBS recorded a 58% reduction in recordable injuries within 18 months.
2. Encourages Accountability
By making safety everyone’s responsibility, BBS creates peer accountability. Employees are more likely to speak up when they feel ownership over safety outcomes.
3. Improves Communication
Constructive, two-way safety conversations during observations help build relationships, trust, and mutual respect among teams.
4. Focuses on Leading Indicators
Rather than only reacting to incidents (lagging indicators), BBS gives real-time insights into leading indicators—early warnings based on behavior patterns.
But Does Behavior-Based Safety Really Work?
The answer isn’t straightforward.
✅ Yes, When Implemented Properly
Companies with strong leadership, clear communication, and active participation often report:
- 30–70% fewer incidents
- Higher employee engagement
- Better compliance with safety protocols
Example: A refinery in Alberta integrated BBS with its safety management system and saw lost-time injury frequency drop by 60% in just one year.
❌ No, When Poorly Designed or Misused
However, poorly implemented BBS programs can backfire. Some workers feel that such programs:
- Focus too much on blaming individuals
- Ignore root causes (equipment, workload, systems)
- Feel like surveillance instead of support
- Are inconsistent and lack follow-up
Common Criticisms of Behavior-Based Safety
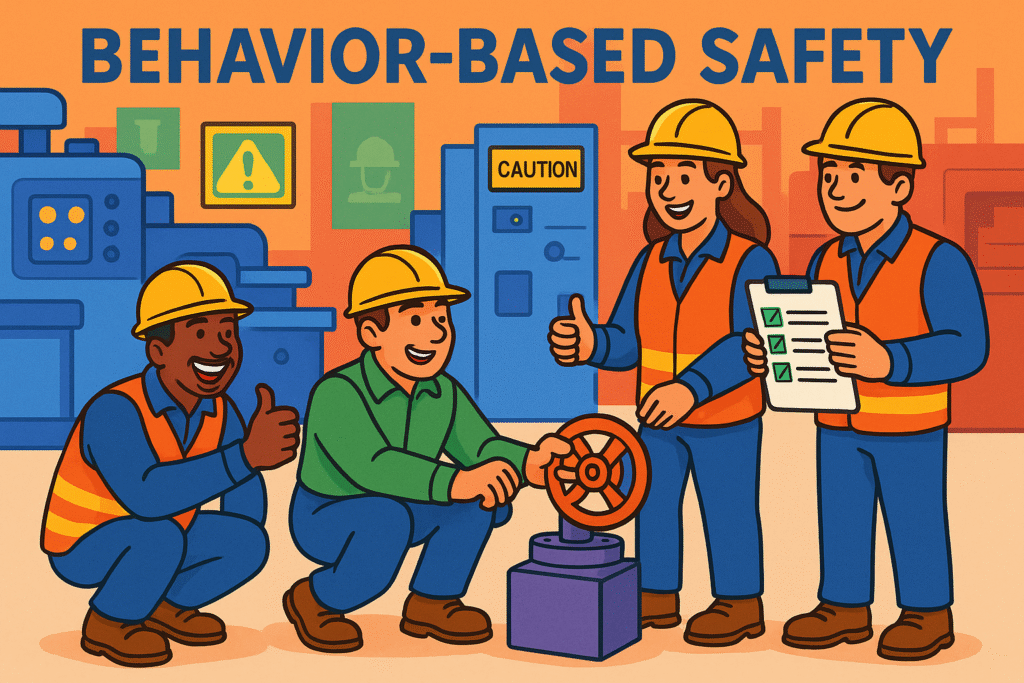
1. “Blame the Worker” Culture
If a program focuses solely on changing individual behavior, it may overlook systemic issues like outdated procedures, poor equipment design, or unreasonable workloads. This creates resentment among workers and erodes trust.
2. Observer Bias
Peer observers are not always trained psychologists. Misinterpretation of intent or behavior can lead to flawed feedback and skewed data.
3. No Real Action from Data
Many programs collect observations but fail to analyze or act on them meaningfully. Behavior data without intervention leads to wasted effort.
4. Temporary Compliance
When workers know they’re being observed, they often temporarily act safer—a phenomenon known as the Hawthorne Effect—which doesn’t guarantee long-term improvement.
Key Conditions for Effective BBS Implementation
For BBS to truly work, it must be designed and implemented as part of a broader OHSE strategy—not as a standalone initiative.
🔑 1. Leadership Commitment
Management must champion the process, participate in observations, and model the behaviors they expect.
🔑 2. Integration with Systemic Controls
BBS must complement—not replace—engineering controls, safety audits, and hazard elimination. For example, if workers frequently climb on unstable surfaces, the fix might be better ladders—not just “behave more carefully.”
🔑 3. Empowered Workers
When workers are trained, involved, and valued in the program, they feel ownership. BBS works best as a bottom-up approach, not a top-down mandate.
🔑 4. Transparent Feedback Loops
Make observation data visible and discuss trends openly. Use the data to inform toolbox talks, SOP reviews, and equipment upgrades.
🔑 5. Focus on Positive Reinforcement
Punishment rarely leads to lasting behavior change. Reward safe behavior openly, and coach unsafe behavior privately.
Behavior-Based Safety vs. Other Approaches
Approach | Focus | Strength | Limitation |
---|---|---|---|
Behavior-Based Safety (BBS) | Individual behaviors | Engages employees, tracks leading indicators | May ignore system-level hazards |
Traditional Safety | Policies, procedures, compliance | Focuses on standards and documentation | Often reactive; lagging indicators |
Human Factors Engineering | Design and usability | Reduces errors by improving systems/equipment | Requires expert involvement, higher costs |
Safety Management Systems | Holistic, policy-driven | Integrated and scalable | Can be bureaucratic or slow to implement |
For best results, BBS should be combined with other OHSE strategies like ergonomic assessments, safety training, and continuous improvement initiatives.
Best Practices for a Behavior-Based Safety Program
- Choose the Right Behaviors
Base them on job hazard analyses, past incidents, and critical risk activities. - Keep Checklists Simple and Specific
Complex or vague checklists reduce observation quality and consistency. - Train Observers Thoroughly
Teach respectful feedback, nonverbal cues, and unbiased reporting. - Review Data Weekly or Monthly
Look for trends. Is PPE non-use increasing? Are hand safety incidents climbing? - Involve Safety Committees
Let cross-functional teams assess and adjust the BBS process regularly. - Celebrate Success
Recognize individuals, teams, and sites for improvements in safe behavior trends.
Real-Life Example: BBS in Action
A manufacturing plant in Ontario faced frequent minor injuries due to improper lifting and rushing tasks. By launching a Behavior-Based Safety program focused on:
- Peer observations around lifting technique
- Feedback on time pressure and planning
- Adjusted work pace policies
…they reduced strain-related injuries by 40% in 9 months and improved overall job satisfaction in employee surveys.
The Future of Behavior-Based Safety
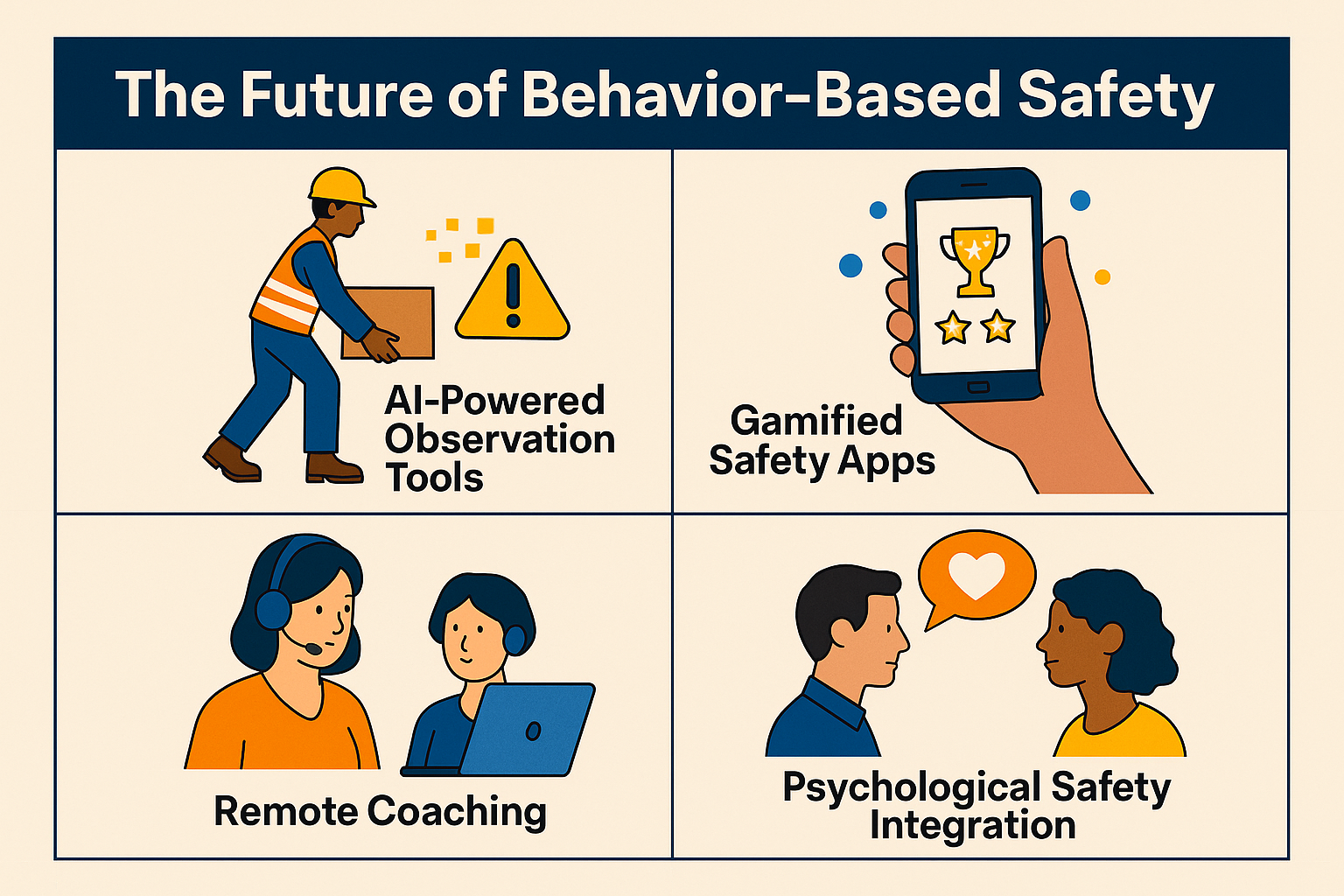
As safety technology advances, BBS is evolving too:
- AI-Powered Observation Tools
Wearables and cameras can automatically detect unsafe postures or PPE violations. - Gamified Safety Apps
Workers earn points or rewards for reporting and exhibiting safe behaviors. - Psychological Safety Integration
BBS programs are increasingly including mental health and emotional wellness to address stress, fatigue, and communication barriers.
Digital dashboards, remote coaching, and virtual observations are making Behavior-Based Safety more scalable and data-driven than ever before.
Conclusion: Does Behavior-Based Safety Work?
Yes—Behavior-Based Safety works when it is built into a well-rounded OHSE system, supported by leadership, embraced by employees, and continuously refined.
It should never replace hazard elimination, proper training, or robust system design. But when applied correctly, BBS empowers workers, predicts risks, and supports a culture of shared accountability.
So, does Behavior-Based Safety really work?
Yes—but only when the behavior of leadership reflects the values they want to see in their teams.
No comments yet