Flammable substances are found in many workplaces across a wide range of industries, from manufacturing and construction to laboratories and offices. While these substances are often necessary for day-to-day operations, they also pose significant risks if not properly managed.
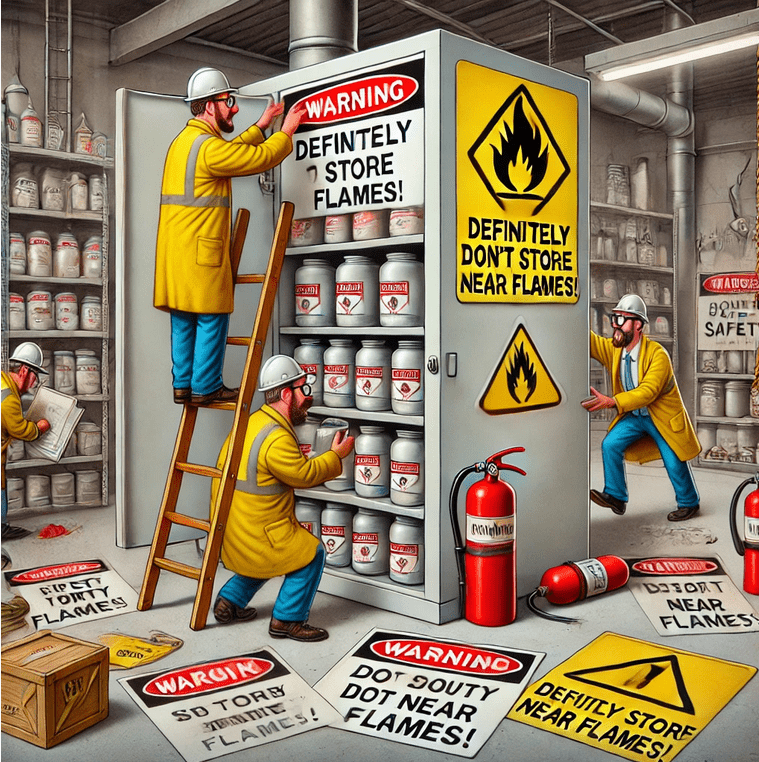
Improper storage and handling of flammable substances can lead to fires, explosions, and other severe hazards that can endanger lives, damage property, and disrupt business operations. Ensuring the safe storage and handling of these materials is critical for maintaining a safe workplace and complying with Occupational Health and Safety (OHSE) regulations.
This article outlines the best practices for the safe storage and handling of flammable substances in the workplace.
1. Understanding Flammable Substances
Flammable substances are materials that can easily ignite and burn when exposed to heat, sparks, or flames. These substances can be in the form of gases, liquids, or solids. Some common examples include:
- Flammable Gases: Propane, acetylene, and hydrogen.
- Flammable Liquids: Gasoline, solvents, paints, alcohols, and cleaning chemicals.
- Flammable Solids: Certain types of dust (such as grain or metal dust), wood, and paper products.
Each type of flammable substance presents unique hazards and requires specific storage and handling protocols to minimize the risk of fire or explosion.
2. Hazards Associated with Flammable Substances
The risks associated with flammable substances include fire, explosion, toxic fumes, and environmental damage. If these materials are stored improperly or handled carelessly, they can ignite quickly and cause significant harm. Common hazards include:
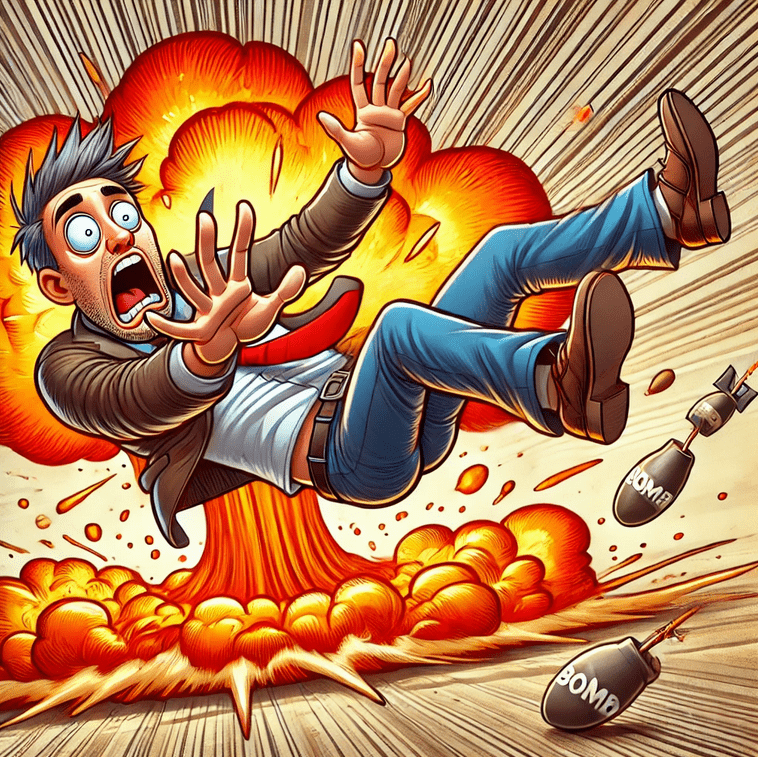
- Ignition Sources: Sparks from machinery, open flames, static electricity, and faulty electrical equipment can ignite flammable materials.
- Chemical Reactions: Flammable substances can react with other chemicals, leading to hazardous byproducts or increased fire risks.
- Vapor Accumulation: Flammable liquids often emit vapors that can accumulate in confined spaces and be easily ignited.
- Inadequate Ventilation: Poor ventilation can cause the buildup of dangerous fumes, increasing the likelihood of an explosion.
3. OHSE Regulations and Standards
In many countries, regulatory bodies such as the Occupational Safety and Health Administration (OSHA) and similar organizations around the world set guidelines for the safe handling and storage of flammable substances. Employers are legally required to comply with these regulations to protect their workers and prevent accidents.
Some key regulations include:
- Chemical Labeling: Proper labeling of flammable substances under the Globally Harmonized System of Classification and Labeling of Chemicals (GHS) is mandatory. This includes hazard symbols and clear instructions for safe handling.
- Storage Limits: OHSE regulations often specify limits on the quantity of flammable materials that can be stored in certain areas to reduce fire risks.
- Ventilation Requirements: Adequate ventilation is required to prevent the buildup of flammable vapors in storage areas.
- Fire Safety Equipment: Employers must provide fire extinguishers, sprinklers, and other fire suppression systems in areas where flammable substances are stored or used.
4. Best Practices for the Safe Storage of Flammable Substances
Proper storage of flammable substances is crucial to minimizing the risk of fire or explosion. Implementing the following best practices ensures compliance with safety regulations and reduces hazards:
a. Use of Approved Storage Containers
Flammable liquids and gases should be stored in containers that are specifically designed and approved for their use. These containers should be constructed from materials that prevent leaks, corrosion, and chemical reactions. Safety cans and containers certified by regulatory bodies, such as the Underwriters Laboratories (UL), are recommended.
b. Segregation of Incompatible Materials
Certain flammable substances can react dangerously with other chemicals. To prevent accidents, it is important to segregate incompatible materials during storage. For example, flammable substances should not be stored near oxidizing agents, acids, or reactive metals.
c. Proper Labeling and Signage
Clearly label all flammable substances with their chemical names, hazard symbols, and storage requirements. Storage areas should also be marked with appropriate safety signage, such as “Flammable – Keep Away from Ignition Sources,” to alert workers of the potential danger.
d. Ventilated Storage Areas
Flammable liquids emit vapors that can accumulate and ignite if not properly ventilated. Storage areas should have adequate ventilation to disperse vapors and prevent them from reaching dangerous concentrations. This is especially important in enclosed spaces.
e. Temperature Control
Flammable substances should be stored in areas where the temperature is controlled to prevent heat buildup. Avoid storing these materials in direct sunlight or near heat sources such as boilers, ovens, or furnaces.
f. Fire-Resistant Storage Cabinets
Use fire-resistant storage cabinets or flammable liquid storage rooms that comply with OHSE standards. These cabinets are designed to contain a fire for a specific period, giving employees enough time to evacuate and allowing emergency responders to control the situation before it spreads.
g. Limiting Quantities
Store only the minimum quantity of flammable substances required for your operations. Excessive amounts of flammable materials increase the risk of a larger fire. Stockpiling flammable liquids and gases can be hazardous and may violate regulatory limits.
h. Storage Away from Exit Routes
Flammable substances should not be stored near exit routes or stairwells. In the event of a fire, these substances could obstruct escape routes or worsen the fire, making evacuation more difficult.
5. Safe Handling of Flammable Substances
Proper handling procedures are just as important as safe storage. Employees should be trained in the correct techniques for handling flammable substances to reduce the risk of spills, leaks, and fires.
a. Training and Education
All employees who handle flammable substances should receive training on safe handling practices, including:
- Recognizing hazards associated with flammable substances.
- Proper use of personal protective equipment (PPE), such as gloves and goggles.
- Procedures for safely transferring flammable liquids from one container to another.
- Emergency procedures in case of a spill, leak, or fire.
b. Use of PPE
When handling flammable substances, employees should wear appropriate personal protective equipment to reduce the risk of burns, chemical exposure, and inhalation of hazardous vapors. This may include flame-resistant clothing, gloves, eye protection, and respirators.
c. Static Electricity Precautions
Flammable liquids can accumulate static electricity, which may lead to ignition. To prevent this, use grounding and bonding techniques when transferring flammable liquids between containers. Grounding ensures that the containers and equipment are electrically connected to the ground, preventing the buildup of static charge.
d. Handling in Well-Ventilated Areas
Whenever possible, handle flammable substances in well-ventilated areas to reduce the risk of vapor accumulation. If handling in confined spaces, ensure that appropriate ventilation systems are in place to remove vapors and supply fresh air.
e. Avoiding Ignition Sources
When handling flammable substances, keep them away from open flames, sparks, and other ignition sources. This includes avoiding the use of electrical equipment that is not rated for use in hazardous areas.
f. Proper Disposal
Dispose of flammable waste materials in accordance with local hazardous waste regulations. Never pour flammable liquids down drains, as this can lead to explosions or environmental contamination. Use designated hazardous waste containers for proper disposal.
6. Responding to Incidents Involving Flammable Substances
Despite the best safety measures, accidents can still occur. Having an effective emergency response plan is essential for minimizing the impact of incidents involving flammable substances.
a. Spill Containment and Cleanup
In the event of a spill, employees should know how to contain the flammable liquid and clean it up safely. Spill kits containing absorbent materials, neutralizing agents, and PPE should be readily available in areas where flammable substances are used or stored.
b. Fire Extinguishers and Suppression Systems
Workplaces should be equipped with appropriate fire extinguishers and suppression systems. Employees should be trained to use fire extinguishers, particularly those suited for flammable liquids and gases (e.g., Class B fire extinguishers). Automatic fire suppression systems can help control a fire before it spreads.
c. Evacuation Procedures
Clear evacuation procedures should be in place in the event of a fire or chemical release. Ensure that employees are familiar with emergency exit routes, assembly points, and communication protocols.
Conclusion
Flammable substances are essential for many workplaces, but their presence introduces significant risks. Proper storage, handling, and safety measures are critical for reducing the potential for fire, explosion, or environmental damage.
By following OHSE regulations, implementing best practices, and providing employees with the necessary training, businesses can ensure the safe use of flammable materials and protect their workers, property, and operations.
Safe storage and handling of flammable substances is not just about compliance; it’s about fostering a culture of safety that prioritizes the well-being of everyone in the workplace.
No comments yet