Industrial hygiene practices play a critical role in reducing workplace illness by identifying, evaluating, and controlling environmental factors that can harm employees’ health.
By implementing these practices, employers can create safer work environments, minimize absenteeism, and enhance overall productivity.
- Importance of Industrial Hygiene Practices in the Workplace
- Assessing Workplace Hazards
- Control Measures for Reducing Workplace Illness
- Monitoring and Improving Air Quality
- Hygiene Practices for Reducing Illness
- Emergency Preparedness and Training
- Measuring the Effectiveness of Industrial Hygiene Practices
- Final Thoughts
Importance of Industrial Hygiene Practices in the Workplace
Industrial hygiene focuses on mitigating risks posed by physical, chemical, biological, and ergonomic hazards. When these hazards are left unaddressed, they can lead to illnesses such as respiratory problems, skin conditions, or chronic diseases.

Key Benefits of Industrial Hygiene Practices
- Health Protection: Reduces exposure to harmful substances like dust, chemicals, and pathogens.
- Regulatory Compliance: Ensures adherence to occupational health and safety standards.
- Enhanced Productivity: Healthy workers are more focused and efficient.
Benefit | Impact on the Workplace |
---|---|
Health Protection | Reduces illness-related absenteeism |
Regulatory Compliance | Avoids legal penalties and fines |
Enhanced Productivity | Boosts morale and efficiency |
Pro Tip: Regularly review workplace conditions to identify emerging hazards.
Assessing Workplace Hazards
1. Conduct Hazard Assessments
A comprehensive hazard assessment is the first step in industrial hygiene practices. This involves identifying potential risks in the work environment.
- Visual Inspections: Regularly inspect work areas for visible hazards.
- Monitoring Tools: Use equipment like gas detectors and noise meters to measure exposure levels.
- Employee Feedback: Engage workers to identify overlooked hazards.
Hazard Type | Example |
Chemical | Solvents, fumes, and aerosols |
Physical | Noise, heat, and radiation |
Biological | Viruses, bacteria, and mold |
Learn how to conduct effective workplace inspections in our Hazard Assessment Guide.
2. Identify High-Risk Areas
Focus on areas where workers are more likely to be exposed to hazards, such as production lines, chemical storage rooms, or confined spaces.
- Mapping Hazards: Create a map of high-risk zones to prioritize interventions.
- Proximity Analysis: Evaluate how close workers are to sources of hazards.
- Usage Patterns: Consider how frequently hazardous areas are accessed.
Control Measures for Reducing Workplace Illness
3. Implement Engineering Controls
Engineering controls are the most effective way to reduce exposure to workplace hazards by eliminating or isolating risks.
- Ventilation Systems: Install local exhaust ventilation to remove airborne contaminants.
- Enclosures: Use physical barriers to contain hazardous materials.
- Substitution: Replace toxic substances with safer alternatives.
Explore innovative ventilation solutions at Amazon.
4. Apply Administrative Controls
Administrative controls focus on modifying work practices and procedures to minimize risks.
- Rotating Shifts: Limit exposure time by rotating workers in high-risk areas.
- Training Programs: Educate employees on hazard identification and safe practices.
- Signage: Use warning signs to alert workers of potential dangers.
Pro Tip: Pair administrative controls with engineering solutions for comprehensive protection.
5. Provide Personal Protective Equipment (PPE)
PPE serves as the last line of defense against workplace hazards. Ensure workers are equipped with the right protective gear for their tasks.
- Respirators: Protect against inhaling toxic substances.
- Gloves: Prevent skin contact with chemicals and biological agents.
- Hearing Protection: Reduce the impact of high noise levels.
PPE Type | Application |
Respirators | Chemical fumes, dust |
Gloves | Chemical handling, biological risks |
Earplugs/Earmuffs | Noisy environments |
Monitoring and Improving Air Quality
6. Test and Monitor Air Quality
Air quality testing is essential to identify and mitigate airborne hazards in the workplace.
- Sampling Techniques: Use air samplers to measure contaminants like dust and gases.
- Real-Time Monitoring: Invest in devices that provide continuous air quality readings.
- Threshold Limits: Compare results with occupational exposure limits (OELs).
For more on air quality management, see our Airborne Hazard Prevention Guide.
7. Maintain Ventilation Systems
Effective ventilation systems are crucial for ensuring clean air circulation in the workplace.
- Regular Inspections: Check for blockages or wear in ventilation systems.
- Filter Replacements: Change filters regularly to maintain efficiency.
- Upgrades: Invest in high-efficiency particulate air (HEPA) filters for optimal performance.
Find advanced ventilation systems at Amazon.
Hygiene Practices for Reducing Illness
8. Promote Hand Hygiene
Proper hand hygiene is one of the simplest yet most effective ways to reduce the spread of illnesses.
- Handwashing Stations: Ensure facilities are equipped with soap and running water.
- Sanitizers: Provide alcohol-based sanitizers in high-traffic areas.
- Training: Educate workers on proper handwashing techniques.
9. Encourage Workplace Cleanliness
A clean workplace reduces the risk of infections and allergic reactions caused by dust or mold.
- Regular Cleaning: Schedule frequent cleaning of shared spaces and equipment.
- Waste Management: Dispose of waste properly to avoid contamination.
- Mold Prevention: Address water leaks promptly to prevent mold growth.
Emergency Preparedness and Training
10. Conduct Regular Safety Drills
Preparedness ensures workers know how to respond effectively to emergencies.
- Scenario-Based Training: Simulate incidents like chemical spills or gas leaks.
- Evacuation Drills: Practice safe evacuation procedures regularly.
- First Aid Training: Equip workers to provide immediate assistance during medical emergencies.
11. Create an Emergency Response Plan
An emergency response plan outlines steps to manage workplace incidents effectively.
- Roles and Responsibilities: Assign roles for coordinating responses.
- Communication Systems: Establish channels for alerting employees.
- Resource Allocation: Ensure availability of first aid kits and PPE.
Pro Tip: Keep emergency plans updated to address new workplace hazards.
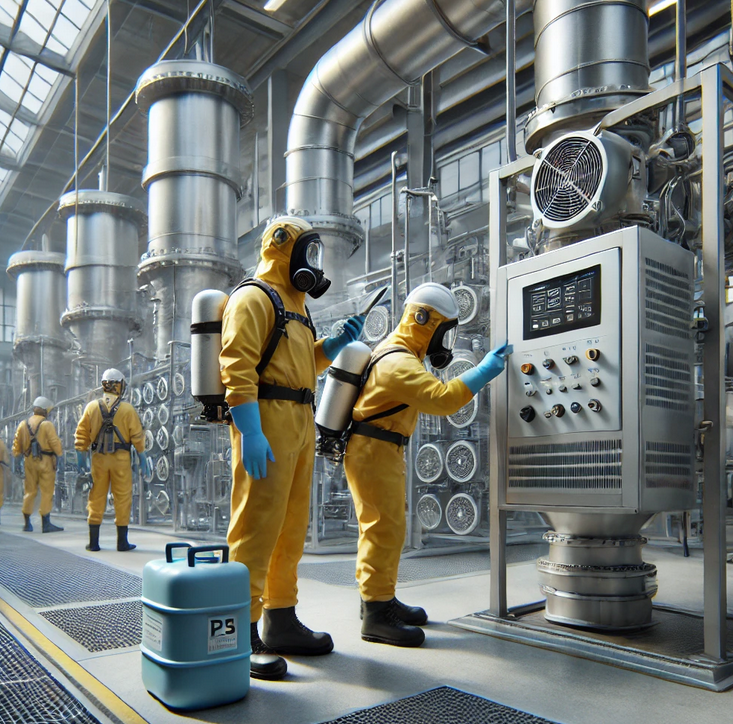
Measuring the Effectiveness of Industrial Hygiene Practices
12. Monitor Health Outcomes
Tracking health metrics helps determine the impact of hygiene practices.
- Medical Surveillance: Conduct periodic health checkups for employees.
- Incident Analysis: Review reports of illnesses and near misses.
- Feedback Mechanisms: Gather employee input on safety measures.
13. Perform Regular Audits
Audits ensure that industrial hygiene practices remain effective and up to date.
- Compliance Checks: Verify adherence to safety standards and regulations.
- Process Evaluations: Assess the efficiency of implemented controls.
- Continuous Improvement: Revise practices based on audit findings.
Final Thoughts
Industrial hygiene practices are essential for reducing workplace illness and promoting a healthy, productive workforce.
By focusing on hazard assessments, control measures, and continuous monitoring, organizations can create safer environments for their employees. Incorporate these strategies into your workplace to build a culture of safety and well-being.
No comments yet