Occupational health and safety (OHS) is essential in all workplaces, particularly for general labour workers who face unique risks in physically demanding environments.
This Article will explore the fundamental principles of OHS, discuss specific hazards that general labour workers may encounter, and provide practical strategies for maintaining a safe workplace.

Additionally, it will include a knowledge quiz and a table summarizing key OHS practices for general labour workers.
- 1. Introduction to Occupational Health and Safety
- 2. Understanding OHS for General Labour Workers
- 3. Key Components of OHS for General Labour Workers
- 4. Legal Responsibilities and OHS Regulations
- 5. Importance of Safety Culture
- 6. OHS Knowledge Quiz
- Answer Key:
- 7. OHS Summary Table for General Labour Workers
1. Introduction to Occupational Health and Safety
Occupational Health and Safety (OHS) refers to the set of laws, regulations, procedures, and practices designed to protect the health, safety, and well-being of employees in the workplace.
OHS is critical for preventing workplace injuries, illnesses, and fatalities, especially in industries that require manual labour, such as construction, manufacturing, and warehousing.
The primary objectives of OHS are:
- To ensure that workplaces comply with safety regulations.
- To provide training and resources that enable workers to identify, assess, and mitigate hazards.
- To foster a culture of safety where both employers and employees take proactive steps to reduce risks.
2. Understanding OHS for General Labour Workers
General labour workers include individuals who perform tasks that require physical effort, such as construction workers, warehouse personnel, landscapers, and factory workers.
These jobs often involve the use of heavy machinery, repetitive movements, exposure to chemicals, and the risk of falls or other accidents. As a result, general labour workers face a higher likelihood of work-related injuries compared to office-based employees.
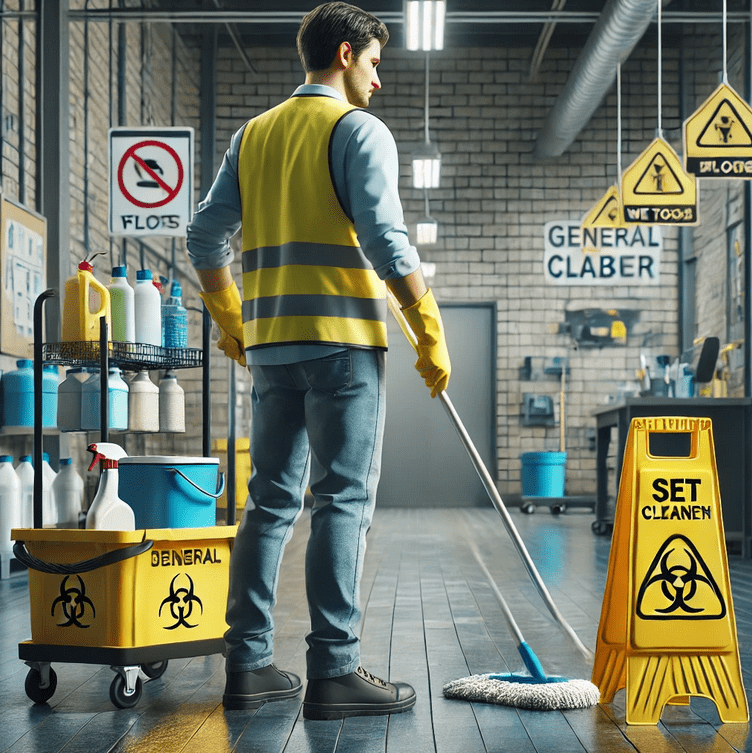
The risks for general labourers include:
- Musculoskeletal Injuries (MSIs): Repetitive movements, heavy lifting, and awkward postures can lead to strains, sprains, and other musculoskeletal injuries.
- Falls: Working at heights or on slippery surfaces increases the risk of falls, which can result in serious injuries or even fatalities.
- Chemical Exposure: In certain industries, general labourers may be exposed to hazardous chemicals that can cause skin irritations, respiratory issues, or long-term health effects.
- Machinery Accidents: Operating or working near heavy machinery introduces the risk of getting caught in or struck by moving parts.
- Heat and Cold Stress: Outdoor labourers face extreme temperatures, which can lead to heat stroke, hypothermia, or other environmental-related health problems.
3. Key Components of OHS for General Labour Workers
3.1. Hazard Identification and Risk Assessment
One of the most important elements of OHS is identifying hazards in the workplace and assessing the associated risks. A hazard is any situation or condition that can cause harm, such as faulty equipment, slippery floors, or improper handling of chemicals.
Employers are responsible for conducting regular inspections and risk assessments to identify potential hazards. Once hazards are identified, they should be classified based on the severity of the risk they pose, and control measures should be implemented to minimize or eliminate them.
3.2. Personal Protective Equipment (PPE)
Personal protective equipment (PPE) plays a crucial role in protecting workers from injuries and illnesses. General labour workers should use appropriate PPE depending on the tasks they perform. Common types of PPE include:
- Hard Hats: Protect the head from falling objects or debris.
- Safety Glasses or Goggles: Protect the eyes from dust, chemicals, or flying particles.
- Ear Protection: Shields the ears from loud machinery noise, preventing hearing loss.
- Gloves: Protect the hands from cuts, burns, or chemical exposure.
- Steel-Toe Boots: Provide foot protection from falling objects, sharp items, or machinery.
- High-Visibility Clothing: Ensures that workers are easily visible to others, especially in low-light or high-traffic areas.
3.3. Safe Lifting Techniques
One of the most common causes of injury for general labour workers is improper lifting. Workers should be trained to use proper body mechanics when lifting heavy objects. Safe lifting techniques include:
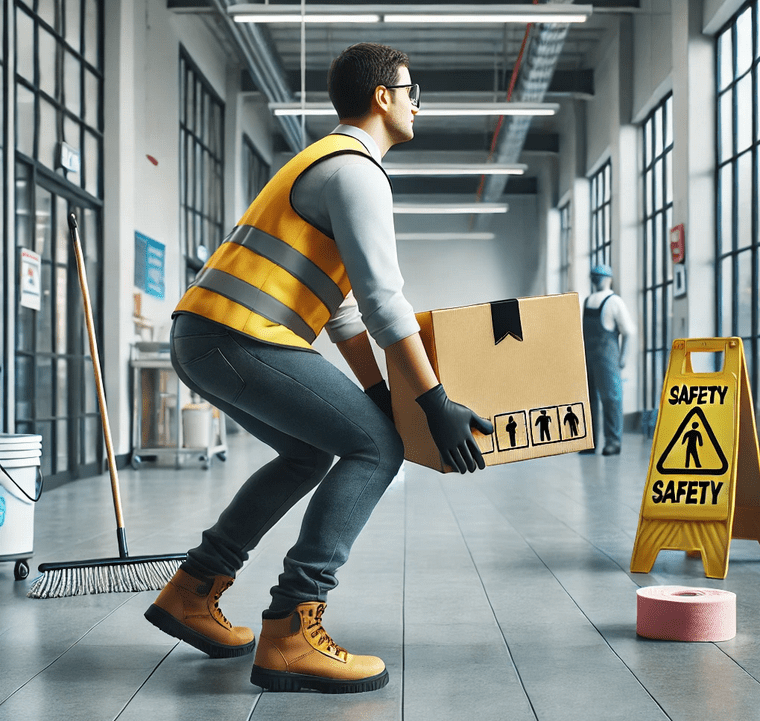
- Bending the Knees: Always bend at the knees, not the waist, to lift heavy items.
- Maintaining a Neutral Spine: Keep the back straight to avoid straining the lower back.
- Using Leg Muscles: Lift with the strength of the legs, not the back.
- Team Lifting: For heavy or awkward objects, team lifting (with two or more workers) may be necessary.
3.4. Lockout/Tagout Procedures
Machinery-related accidents are common in industries that require general labour. Lockout/tagout (LOTO) procedures ensure that machinery is properly shut off and cannot be started again until maintenance or repairs are completed. Workers should be trained in these procedures to avoid accidental machine activation.
3.5. Emergency Preparedness
Accidents can still happen even when precautions are taken. General labour workers must be prepared to respond to emergencies, including fires, chemical spills, and medical incidents. Emergency preparedness plans should be in place, and workers should be familiar with evacuation routes, first aid procedures, and how to operate fire extinguishers.
3.6. Reporting Hazards
Workers should feel empowered to report unsafe conditions or hazards to their supervisors without fear of reprisal. Effective OHS programs rely on open communication between workers and management to identify and resolve safety concerns.
4. Legal Responsibilities and OHS Regulations
In Canada, occupational health and safety laws are enforced at both the federal and provincial levels. Employers are legally obligated to provide a safe working environment for their employees, and workers have the right to refuse unsafe work.
Employers must:
- Ensure that the workplace complies with OHS standards and regulations.
- Provide appropriate training and education to employees.
- Supply and maintain PPE for workers.
- Conduct regular inspections and risk assessments.
Employees must:
- Follow safety protocols and use PPE as required.
- Report any hazards or unsafe conditions to their employer.
- Participate in safety training and exercises.
5. Importance of Safety Culture
A strong safety culture is essential to maintaining a safe workplace. This culture must be fostered by both management and employees through continuous improvement, ongoing safety training, and open communication.
Key elements of a positive safety culture include:
- Leadership commitment to safety.
- Regular safety training and education.
- Encouraging workers to participate in safety initiatives.
- Rewarding safe work practices.
- Conducting regular safety meetings.
6. OHS Knowledge Quiz
To test your understanding of OHS for general labour workers, take the following quiz:
- What does PPE stand for?
a) Personal Protection Essentials
b) Personal Protective Equipment
c) People Protecting Everyone
d) Protective Personal Essentials - What is the most common cause of musculoskeletal injuries among general labour workers?
a) Repetitive movements
b) Heat exposure
c) Chemical exposure
d) Loud noises - Which of the following is NOT a piece of PPE?
a) Steel-toe boots
b) High-visibility vest
c) Clipboard
d) Hard hat - What is the purpose of a lockout/tagout (LOTO) procedure?
a) To lock up machinery to prevent theft
b) To ensure that machinery is shut off and cannot be accidentally started
c) To lock doors during emergencies
d) To tag machinery for repairs - When lifting heavy objects, which part of the body should be used?
a) The back
b) The arms
c) The legs
d) The shoulders
Answer Key:
- b) Personal Protective Equipment
- a) Repetitive movements
- c) Clipboard
- b) To ensure that machinery is shut off and cannot be accidentally started
- c) The legs
7. OHS Summary Table for General Labour Workers
OHS Practice | Description |
---|---|
Hazard Identification | Regular inspections to identify workplace hazards. |
Risk Assessment | Classify hazards based on severity and implement controls. |
PPE | Use of hard hats, gloves, safety glasses, ear protection, and high-visibility clothing. |
Safe Lifting Techniques | Bend at the knees, maintain a neutral spine, and use leg muscles. |
Lockout/Tagout (LOTO) | Properly shut off machinery before maintenance to prevent accidental start-ups. |
Emergency Preparedness | Familiarize workers with evacuation routes, first aid, and fire extinguisher use. |
Reporting Hazards | Encourage open communication and reporting of unsafe conditions. |
Occupational health and safety for general labour workers is a crucial aspect of any workplace that relies on manual labour. By understanding the hazards specific to these jobs and implementing safety measures such as proper PPE, safe lifting techniques, and emergency preparedness plans, employers can create a safer and healthier environment for their workers.
The continuous education and active participation of workers in OHS practices are key to reducing workplace injuries and ensuring compliance with legal standards.
Establishing a strong safety culture, where every employee is empowered to contribute to safety, can make all the difference in maintaining a productive and injury-free workplace.
No comments yet