How to design a safety checklist for your industry is a vital question for ensuring workplace safety and compliance. A well-designed safety checklist serves as a powerful tool to identify potential hazards, streamline processes, and protect employees from accidents.
By tailoring a checklist to your specific industry, you can address unique risks and foster a culture of safety.
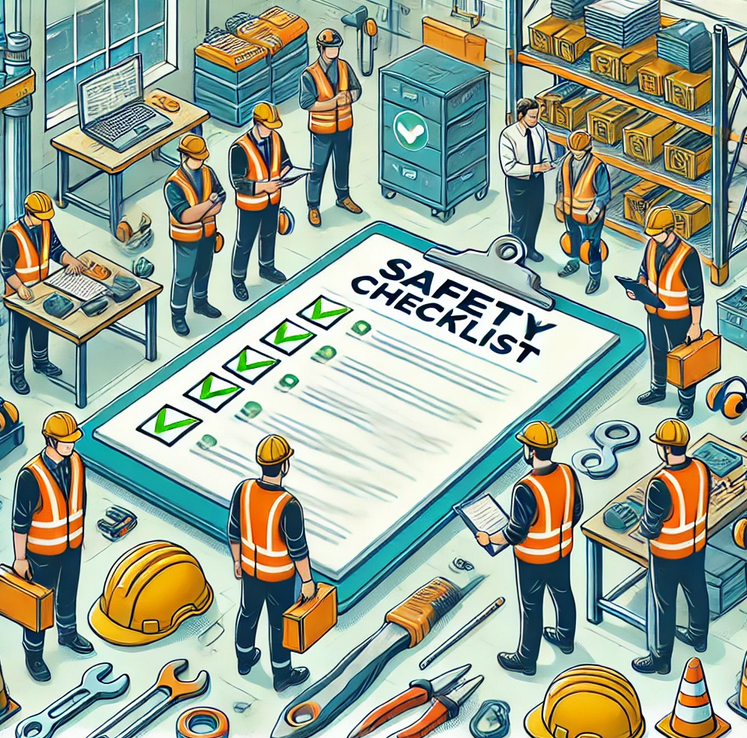
In this comprehensive guide, we’ll explore the key steps to create an effective safety checklist and how to implement it for maximum impact.
- 1. Understanding the Importance of a Safety Checklist
- 2. Assessing Your Industry’s Unique Safety Needs
- 3. Structuring Your Safety Checklist
- 4. How to Customize Your Safety Checklist
- 5. Common Elements in a Safety Checklist
- 6. Benefits of a Safety Checklist
- 7. Common Mistakes to Avoid When Designing a Safety Checklist
- 8. Implementing Your Safety Checklist Effectively
- 9. Digital Tools for Safety Checklists
- 10. Reviewing and Updating the Checklist
- 11. Examples of Industry-Specific Checklists
- 12. Conclusion: How to Design a Safety Checklist for Your Industry
1. Understanding the Importance of a Safety Checklist
Safety checklists are essential documents that outline tasks, inspections, or behaviors necessary to maintain a safe work environment.
- Prevent Accidents: Checklists ensure critical safety measures are followed consistently.
- Enhance Compliance: They help organizations meet regulatory requirements, such as OSHA or ISO standards.
- Improve Efficiency: By streamlining safety inspections, checklists save time and reduce the risk of oversight.
2. Assessing Your Industry’s Unique Safety Needs
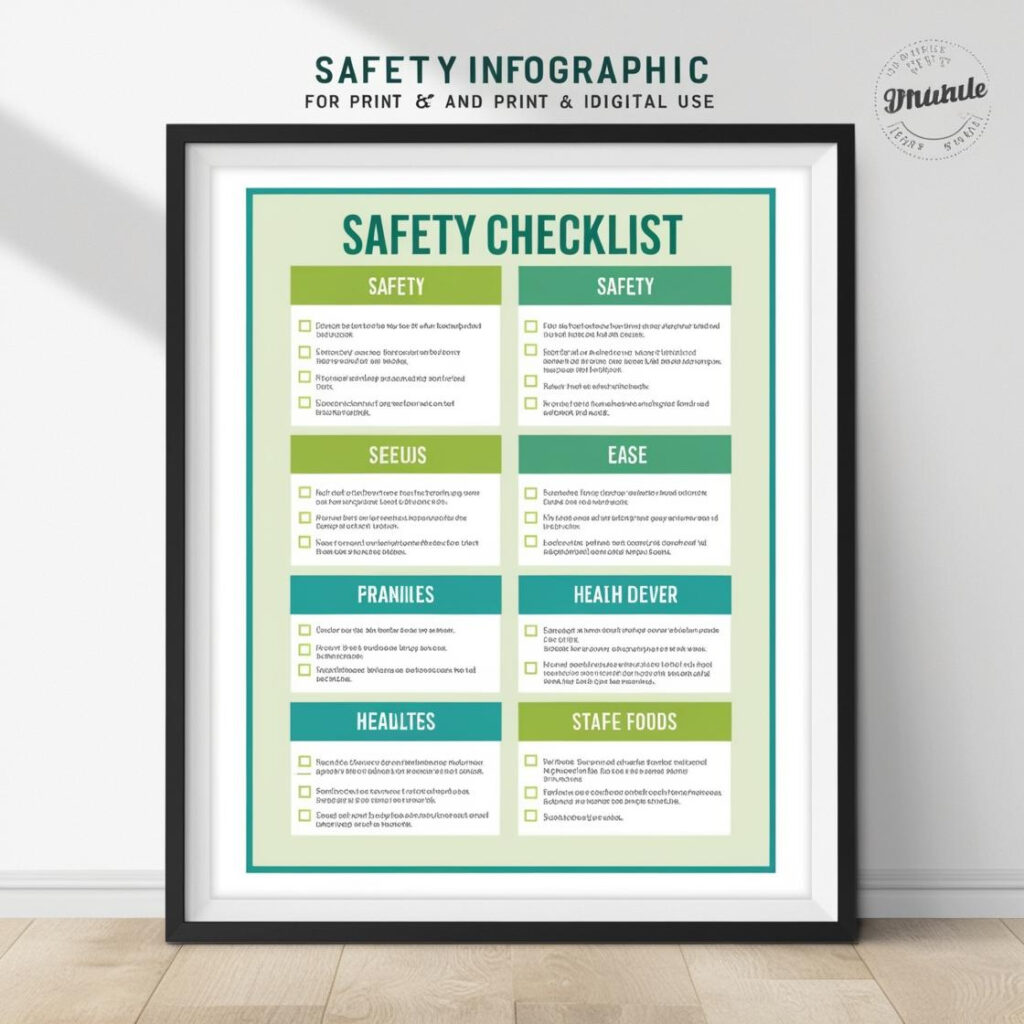
Every industry has distinct hazards that a safety checklist must address. Begin by identifying the specific risks and regulatory requirements in your field.
Steps to Assess Needs:
- Conduct a Risk Assessment:
- Identify hazards, such as machinery, chemicals, or confined spaces.
- Analyze past incidents or near-misses to spot recurring risks.
- Consult Industry Standards:
- Refer to OSHA guidelines, ISO standards, or industry-specific safety regulations.
- Research best practices in your sector.
- Engage Employees:
- Gather feedback from workers who face daily hazards.
- Involve supervisors to understand operational challenges.
For example, a safety checklist for construction might focus on fall protection, while a healthcare checklist would prioritize infection control.
3. Structuring Your Safety Checklist
An effective safety checklist should be easy to understand, logically organized, and specific to your industry.
Key Sections to Include:
- Header Information:
- Date of inspection.
- Location or department.
- Inspector’s name.
- Task Categories:
- Group tasks by type, such as equipment checks, environmental inspections, or employee behaviors.
- Actionable Items:
- Use simple, specific language for each task.
- Include a checkbox for completion status (e.g., “yes,” “no,” or “N/A”).
- Follow-Up Actions:
- Provide space to document hazards or corrective measures.
4. How to Customize Your Safety Checklist
Customizing the checklist ensures it aligns with your industry’s specific needs and operational workflows.
Customization Tips:
- Tailor to Equipment: Include inspections for tools and machinery unique to your field.
- Focus on High-Risk Areas: Prioritize tasks that address the most common or severe hazards.
- Update Regularly: Revise the checklist periodically to reflect regulatory changes or new risks.
- Include Digital Options: Use mobile apps or software for digital checklists, making it easier to track and store data.
5. Common Elements in a Safety Checklist
While every checklist will differ based on industry, certain elements are universal:
Checklist Example Elements:
- Personal Protective Equipment (PPE):
- Are employees wearing the required PPE?
- Is the PPE in good condition?
- Work Environment:
- Are walkways free of obstructions?
- Is lighting adequate for the task?
- Equipment Maintenance:
- Are tools inspected and functional?
- Are guards and safety features in place?
- Emergency Preparedness:
- Are fire exits accessible?
- Are first aid kits fully stocked?
6. Benefits of a Safety Checklist
The advantages of a well-designed safety checklist go beyond compliance. It creates a proactive approach to workplace safety.
Key Benefits:
- Accountability: Assigns clear responsibilities for safety tasks.
- Consistency: Ensures safety measures are applied uniformly across all teams.
- Cost Savings: Reduces costs associated with workplace injuries or fines for non-compliance.
- Data-Driven Insights: Identifies trends and recurring issues, enabling targeted improvements.
7. Common Mistakes to Avoid When Designing a Safety Checklist
Even with the best intentions, certain pitfalls can reduce the effectiveness of your checklist.
Mistakes to Avoid:
- Too Generic: A checklist that isn’t specific to your industry may overlook critical hazards.
- Overly Complex: Lengthy or overly detailed checklists can overwhelm users and reduce compliance.
- Lack of Follow-Up: Failing to act on findings from a checklist defeats its purpose.
8. Implementing Your Safety Checklist Effectively
Designing the checklist is only the first step. Proper implementation ensures it becomes a routine part of your safety practices.
Steps for Effective Implementation:
- Train Employees:
- Provide clear instructions on how to use the checklist.
- Explain its importance in promoting workplace safety.
- Integrate into Workflows:
- Make the checklist part of daily or weekly routines.
- Assign accountability for completing and reviewing the checklist.
- Monitor Usage:
- Conduct audits to ensure the checklist is being used consistently.
- Gather feedback for continuous improvement.
9. Digital Tools for Safety Checklists
Leverage technology to enhance the efficiency and effectiveness of your safety checklist.
Digital Benefits:
- Automated Reports: Track trends and identify recurring issues with ease.
- Real-Time Updates: Instantly distribute updated checklists across teams.
- Accessibility: Enable employees to access checklists on mobile devices.
Explore software solutions like SafetyCulture or OSHA’s Inspection Apps for industry-specific tools.
10. Reviewing and Updating the Checklist
A static checklist can quickly become outdated. Regular reviews ensure it stays relevant and effective.
Tips for Updates:
- Schedule periodic reviews to align with new regulations.
- Use feedback from employees and supervisors to refine tasks.
- Incorporate lessons learned from incidents or audits.
11. Examples of Industry-Specific Checklists
Construction Industry:
- Fall protection gear checks.
- Scaffold and ladder inspections.
- Hazardous material handling protocols.
Healthcare Industry:
- Sterilization equipment checks.
- Proper disposal of biohazard waste.
- Patient room sanitation protocols.
Manufacturing Industry:
- Machine guarding inspections.
- Emergency stop button functionality.
- Forklift maintenance checks.
12. Conclusion: How to Design a Safety Checklist for Your Industry
Creating an industry-specific safety checklist is a proactive step toward a safer workplace. By understanding your unique hazards, customizing tasks, and leveraging technology, you can design a tool that enhances compliance, efficiency, and employee well-being.
A safety checklist is not just a document—it’s a commitment to safeguarding lives and creating a culture of safety.
No comments yet