Safety Checks for Heavy Equipment Operators are essential steps that protect lives, prevent costly damage, and keep projects on schedule. At the very start of every shift, operators who perform thorough checks help eliminate hazards before they become tragedies.
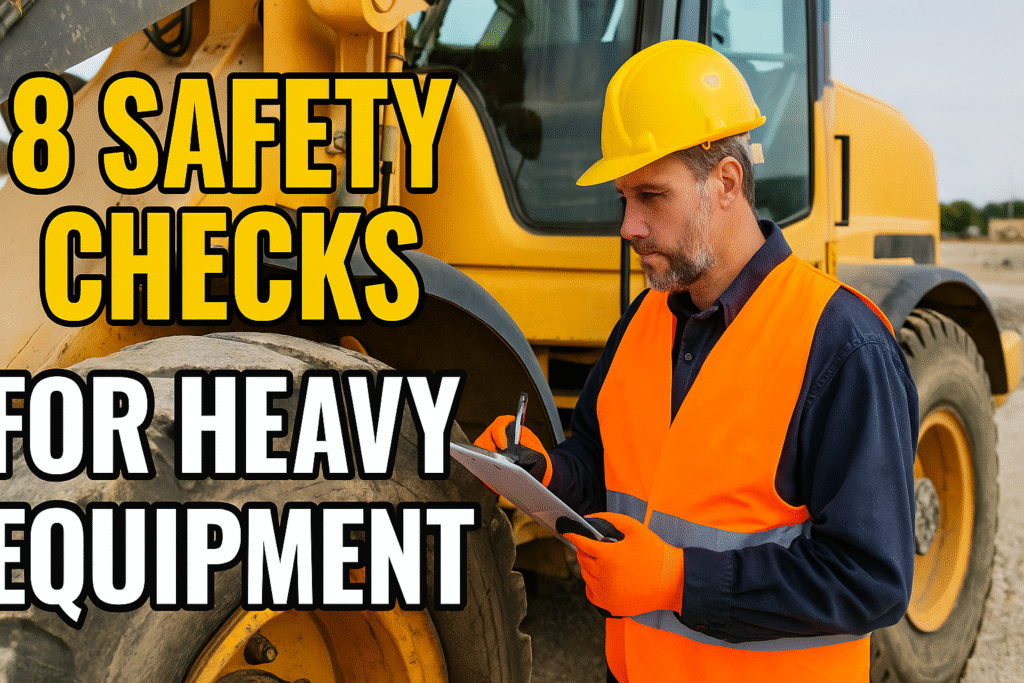
Heavy equipment—from excavators and bulldozers to forklifts and cranes—is critical to many industries. But with that power comes risk. Operating without proper checks can result in equipment failure, collisions, rollovers, and serious injuries.
This guide outlines 8 Safety Checks for Heavy Equipment Operators you can implement immediately to reduce incidents and build a strong safety culture on your site.
- Why Safety Checks for Heavy Equipment Operators Matter
- ✅ 1. Pre-Start Walk-Around Inspection
- ✅ 2. Check Fluid Levels and Leaks
- ✅ 3. Inspect Safety Devices and Alarms
- ✅ 4. Test Brakes and Steering Controls
- ✅ 5. Verify Load Charts and Capacity Limits
- ✅ 6. Assess Surrounding Work Area
- ✅ 7. Review Operator Manual and Safety Procedures
- ✅ 8. Log and Report Inspection Findings
- Best Practices for Safety Checks
- Regulatory Requirements
- Benefits of Safety Checks for Heavy Equipment Operators
- Final Thoughts on Safety Checks for Heavy Equipment Operators
Why Safety Checks for Heavy Equipment Operators Matter
Heavy equipment is involved in some of the most serious workplace incidents.
- Equipment failures can cause rollovers or crushing injuries.
- Missing safety features can expose operators and bystanders to hazards.
- Inadequate inspections can lead to regulatory violations and fines.
According to OSHA (DoFollow), regular inspections and maintenance are core requirements for safe operation.
By making Safety Checks for Heavy Equipment Operators a daily habit, you can reduce risks, improve equipment lifespan, and keep your team safe.
✅ 1. Pre-Start Walk-Around Inspection
One of the most important Safety Checks for Heavy Equipment Operators is the walk-around inspection before starting any equipment.
Look for:
- Leaks (oil, hydraulic fluid, coolant)
- Damage to body or structure
- Loose or missing bolts or pins
- Worn tires or tracks
- Obstructions around the machine
A thorough walk-around helps catch visible hazards before operation begins.
✅ 2. Check Fluid Levels and Leaks
Low or leaking fluids can cause catastrophic failures mid-operation.
Operators should check:
- Engine oil level
- Hydraulic fluid
- Coolant level
- Fuel level
- Transmission fluid (if applicable)
Spotting leaks early can prevent expensive repairs and environmental contamination.
Equipment World (DoFollow) offers excellent industry guides on fluid maintenance.
✅ 3. Inspect Safety Devices and Alarms
Safety devices save lives—but only if they work.
Check that:
- Backup alarms are functional
- Horns and lights operate correctly
- Seat belts are present and undamaged
- Mirrors and cameras are clean and adjusted
- Roll-over protection structures (ROPS) are in good condition
Failure of these systems can lead to fatal accidents, especially on busy sites with pedestrian traffic.
✅ 4. Test Brakes and Steering Controls
Before moving any heavy equipment, operators must test:
- Foot and hand brakes
- Parking brake
- Steering for responsiveness
- Hydraulic controls for smooth operation
Unresponsive or uneven braking and steering are red flags that require immediate maintenance.
✅ 5. Verify Load Charts and Capacity Limits
Operators must understand and confirm the machine’s capacity before lifting or moving loads.
Check:
- Load charts are available and legible
- No unauthorized modifications affect capacity
- Boom, forks, or attachments are rated for the task
Exceeding rated limits can lead to tip-overs, dropped loads, and structural failures.
✅ 6. Assess Surrounding Work Area
A Safety Check for Heavy Equipment Operators isn’t just about the machine—it includes the environment.
Before starting work, inspect:
- Ground conditions (soft spots, slopes)
- Overhead obstructions (power lines, structures)
- Nearby workers or vehicles
- Weather conditions that may affect traction or visibility
A quick environmental scan can prevent many accidents.
✅ 7. Review Operator Manual and Safety Procedures
Operators should regularly review the equipment’s manual and site-specific procedures.
Key reminders include:
- Start-up and shutdown steps
- Proper attachment use
- Emergency procedures
- Communication signals with spotters or ground crew
Never assume all equipment is the same—even similar models may have different features or limits.
✅ 8. Log and Report Inspection Findings
Finally, all Safety Checks for Heavy Equipment Operators should be documented.
Use a daily inspection log or checklist to record:
- Inspection results
- Issues found
- Corrective actions taken
Reporting issues immediately ensures maintenance teams can fix problems before they cause accidents. It also provides proof of compliance with safety regulations.
For more on involving your team in safety efforts, see our article on Behavior-Based Safety: Does It Really Work?.
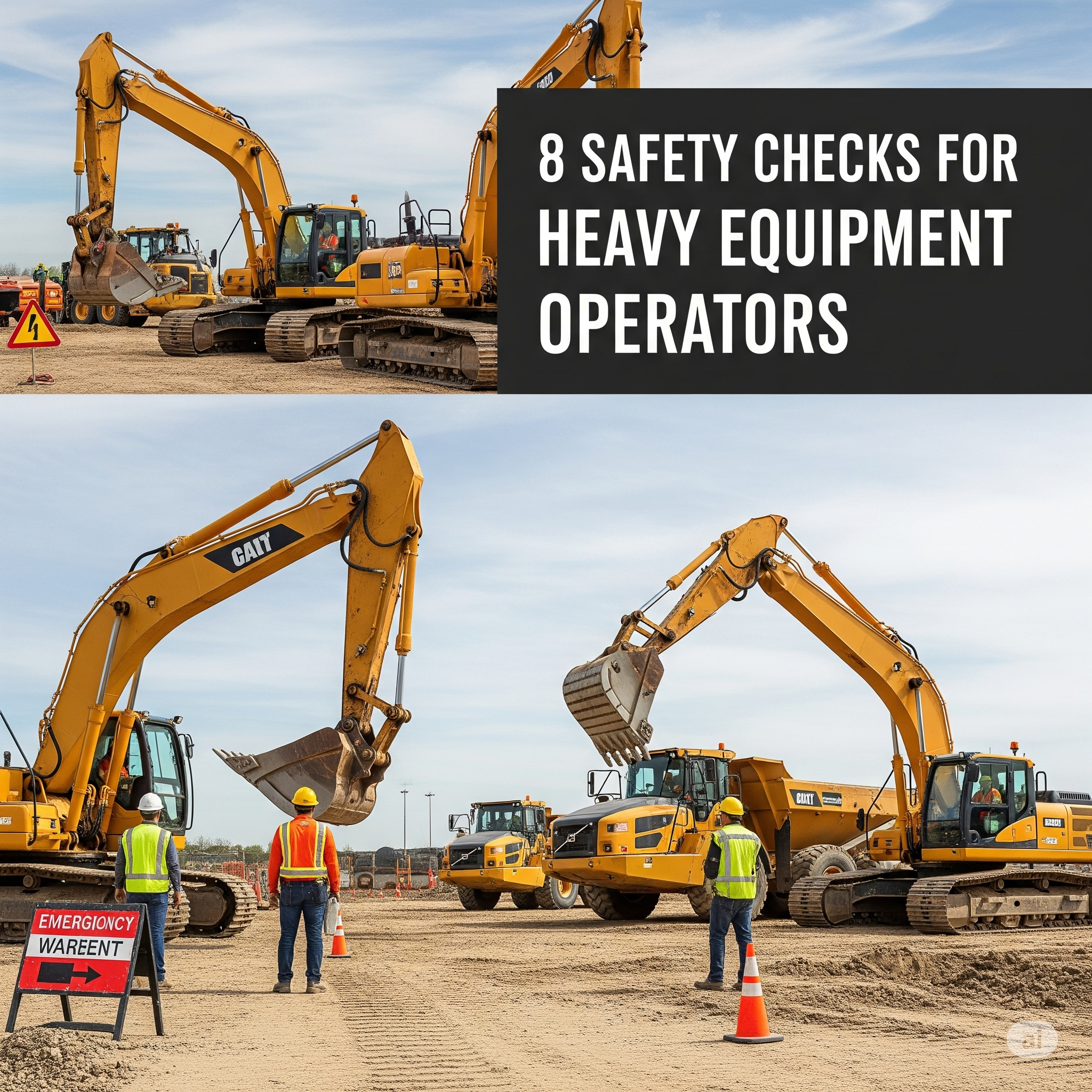
Best Practices for Safety Checks
In addition to the 8 core checks above, consider these best practices to make inspections more effective:
- Provide formal training on inspection procedures.
- Use standardized checklists for consistency.
- Rotate inspectors periodically for a fresh perspective.
- Include safety checks in toolbox talks and safety meetings.
- Encourage workers to speak up about potential issues.
A strong inspection culture is one of the best ways to prevent accidents.
Regulatory Requirements
Many jurisdictions have laws and standards mandating equipment inspections.
For example:
- OSHA 29 CFR 1926.602 (DoFollow) requires daily inspections for earthmoving equipment.
- Canadian OHS regulations require pre-operation checks for powered mobile equipment.
Failure to comply can lead to fines, stop-work orders, or increased liability after an incident.
Benefits of Safety Checks for Heavy Equipment Operators
Adopting these 8 Safety Checks for Heavy Equipment Operators delivers real benefits:
- Fewer incidents and injuries
- Lower repair costs and downtime
- Longer equipment lifespan
- Improved worker confidence and morale
- Demonstrated compliance with regulations
When operators know inspections are expected—and valued—they’re more likely to take them seriously.
Final Thoughts on Safety Checks for Heavy Equipment Operators
Safety Checks for Heavy Equipment Operators are essential, not optional. By making these 8 steps a daily habit, operators can prevent accidents before they happen, protect coworkers, and demonstrate true professionalism.
Invest in training, enforce checklists, and create a culture where safety inspections are non-negotiable. It’s the simplest, most effective way to keep your team safe and your projects on track.
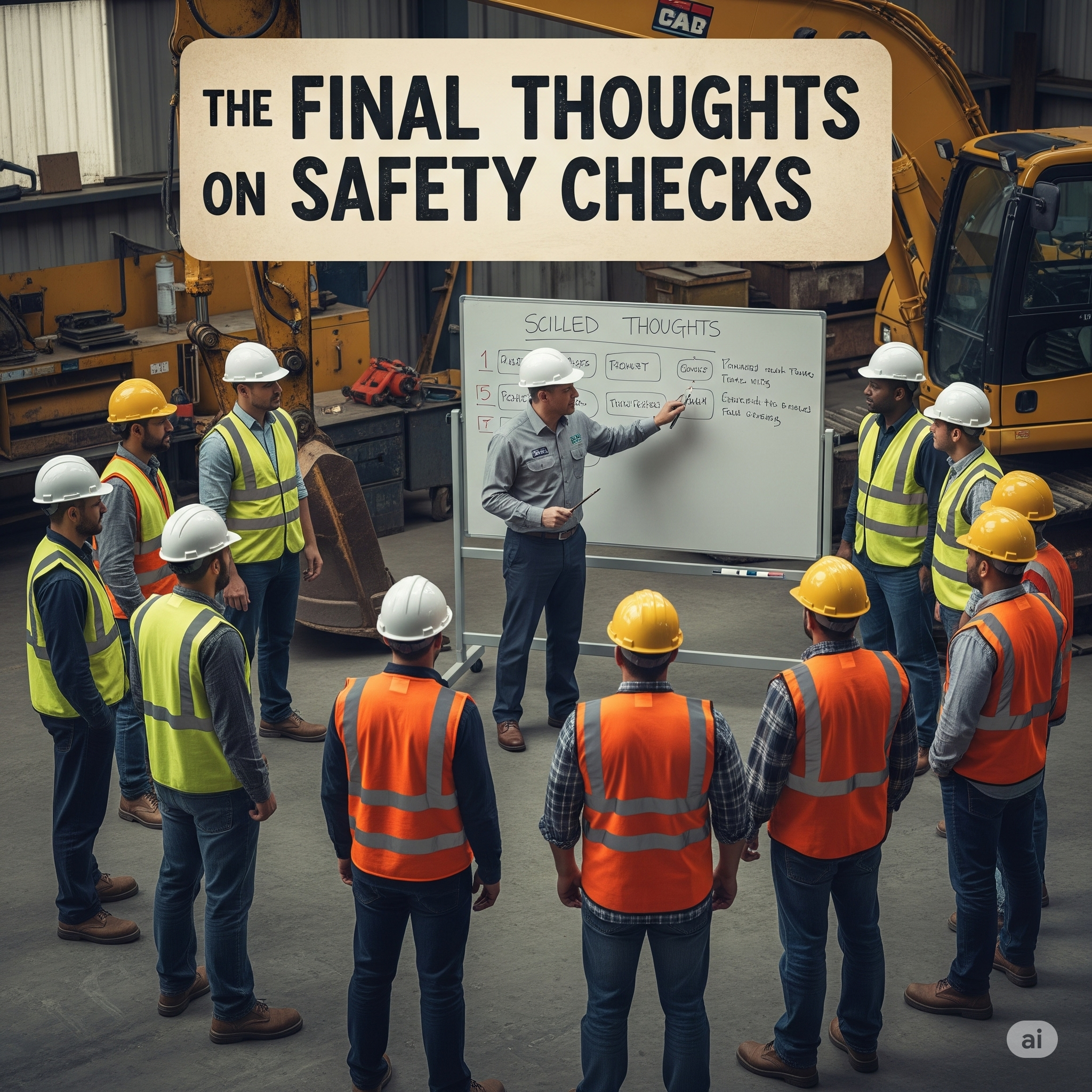
No comments yet