Controlling static electricity in hazardous environments is crucial to avoiding deadly fires, explosions, and injuries.
Static discharge may seem harmless, but in industries dealing with flammable vapors, dusts, or gases, it can be catastrophic.
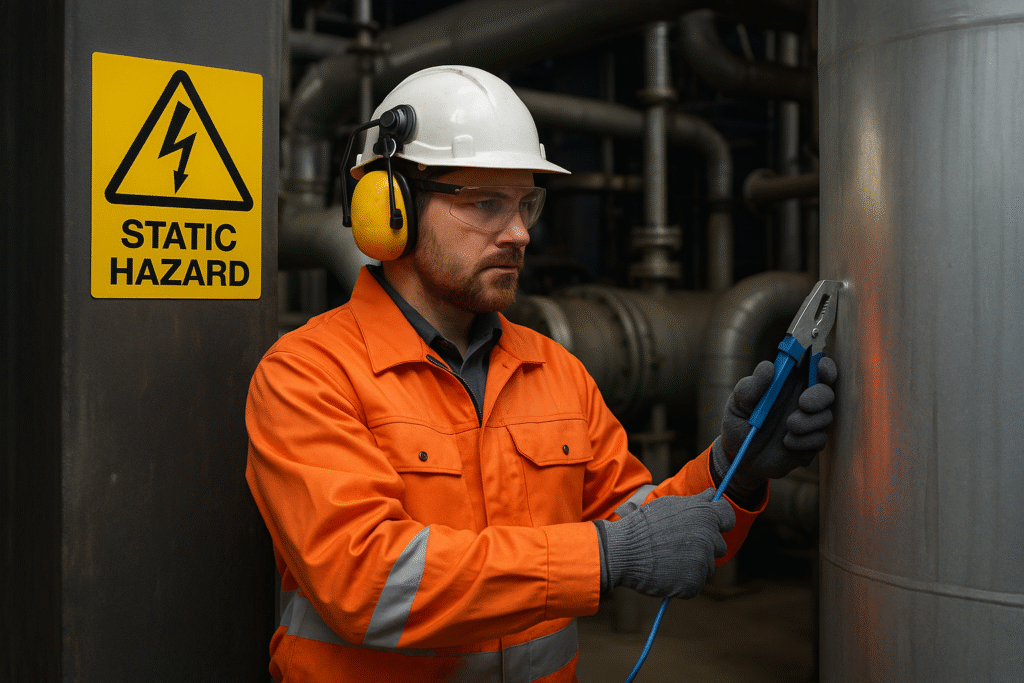
Understanding the risks and implementing proper control measures can mean the difference between routine operations and disaster.
- Understanding Static Electricity: More Than Just a Shock
- Common Sources of Static Electricity in Workplaces
- Why Controlling Static Electricity in Hazardous Environments Is Critical
- Proven Strategies for Controlling Static Electricity
- Personnel Safety: Controlling Human-Generated Static
- Risk Assessment and Static Control Plans
- Training and Awareness
- Regulatory Guidelines and Standards
- Technology Spotlight: Static Dissipation Systems
- Note: Always Re-Evaluate After a Near Miss or Incident
- Resources
- Conclusion: Controlling Static Electricity in Hazardous Environments Saves Lives
Understanding Static Electricity: More Than Just a Shock
Static electricity is the result of an imbalance between positive and negative charges on a surface.
When two materials come into contact and are then separated, electrons can transfer from one to the other, creating a charge. If not safely discharged, this buildup can release suddenly as a spark.
In everyday life, this might mean a mild zap when touching a doorknob.
But in hazardous environments—such as chemical plants, grain silos, or paint spray booths—this spark can ignite airborne particles or vapors, causing explosions or fires.
Common Sources of Static Electricity in Workplaces
Static buildup can occur from a surprising number of routine operations, especially in high-risk industries.
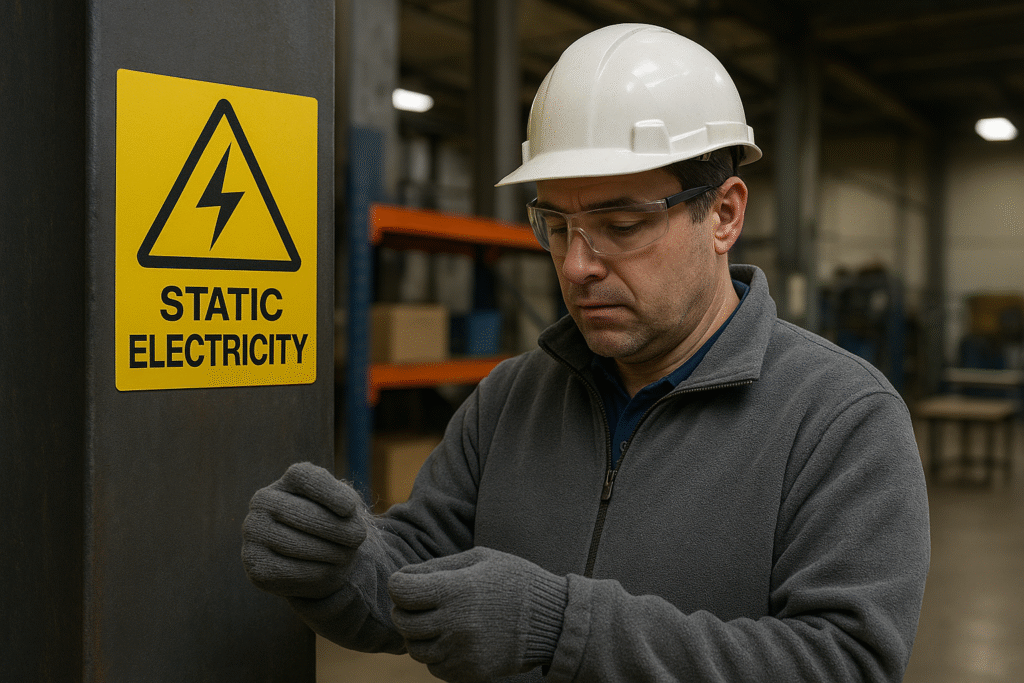
Here are a few examples:
- Pneumatic conveying of powders
- Pouring or mixing flammable liquids
- Spraying or coating operations
- Use of non-conductive containers or tools
- Personnel movement on certain flooring types
- Unbonded hoses or equipment
Each of these actions can generate enough static to create an ignition source if left uncontrolled.
Why Controlling Static Electricity in Hazardous Environments Is Critical
The consequences of uncontrolled static discharge include:
- Dust explosions in food processing or milling industries
- Ignition of flammable vapors in paint, petroleum, or chemical environments
- Damage to sensitive electronic equipment
- Worker injuries or fatalities
A well-known incident is the 1998 flour mill explosion in the USA, where static discharge ignited flour dust, leading to a massive fire and multiple fatalities.
This and many other incidents underline the importance of strict static control practices.
Proven Strategies for Controlling Static Electricity
Bonding and Grounding
One of the most effective methods is bonding and grounding. Bonding connects two conductive objects with a wire to equalize their electrical potential.
Grounding connects equipment to the earth to safely dissipate any charge.
- Ensure all transfer containers are properly grounded
- Bond all conductive parts when moving flammable substances
- Use verified grounding clamps and check resistance regularly
Humidity Control
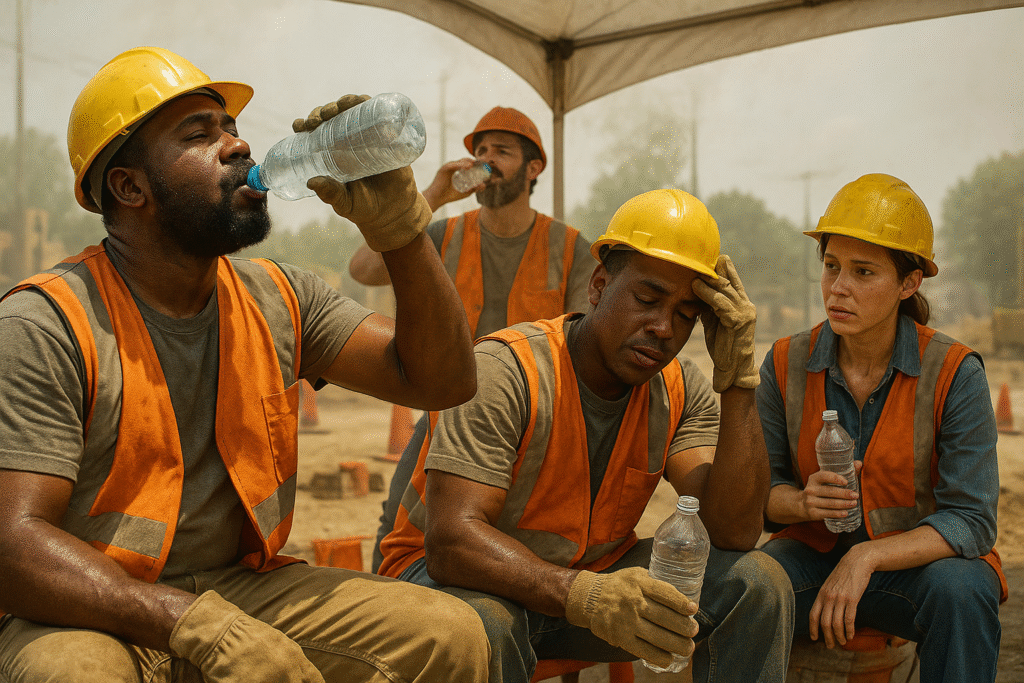
Dry air promotes static buildup. Maintaining a relative humidity of above 50% in indoor environments can drastically reduce static generation.
- Use industrial humidifiers in dry environments
- Monitor humidity levels continuously
Anti-Static Equipment and Materials
Using equipment designed to prevent static generation can make a major difference.
- Use anti-static mats, floors, and clothing
- Equip machinery with static dissipative belts and rollers
- Choose low-resistance materials for containers and tools
Proper Housekeeping
Dust and fine particles can easily become airborne and ignite. Good housekeeping reduces static and lowers explosion risks.
- Vacuum using explosion-proof or intrinsically safe vacuums
- Avoid sweeping or blowing dust into the air
- Schedule regular cleaning of ducts, conveyors, and machinery
Personnel Safety: Controlling Human-Generated Static
Humans can also become charged through friction (walking, removing gloves, etc.). In sensitive areas, personnel should:
- Wear conductive or anti-static footwear
- Use dissipative garments and gloves
- Avoid synthetic clothing that promotes charge buildup
- Step on anti-static mats before entering hazardous areas
Risk Assessment and Static Control Plans
Every workplace should conduct a static electricity risk assessment as part of their overall hazard management system. Key steps include:
- Identifying all areas with flammable or combustible materials
- Pinpointing sources of static generation
- Evaluating grounding and bonding systems
- Creating a static control plan with routine inspections and staff training
Training and Awareness
Employees should receive regular training on static electricity hazards, control measures, and emergency response procedures.
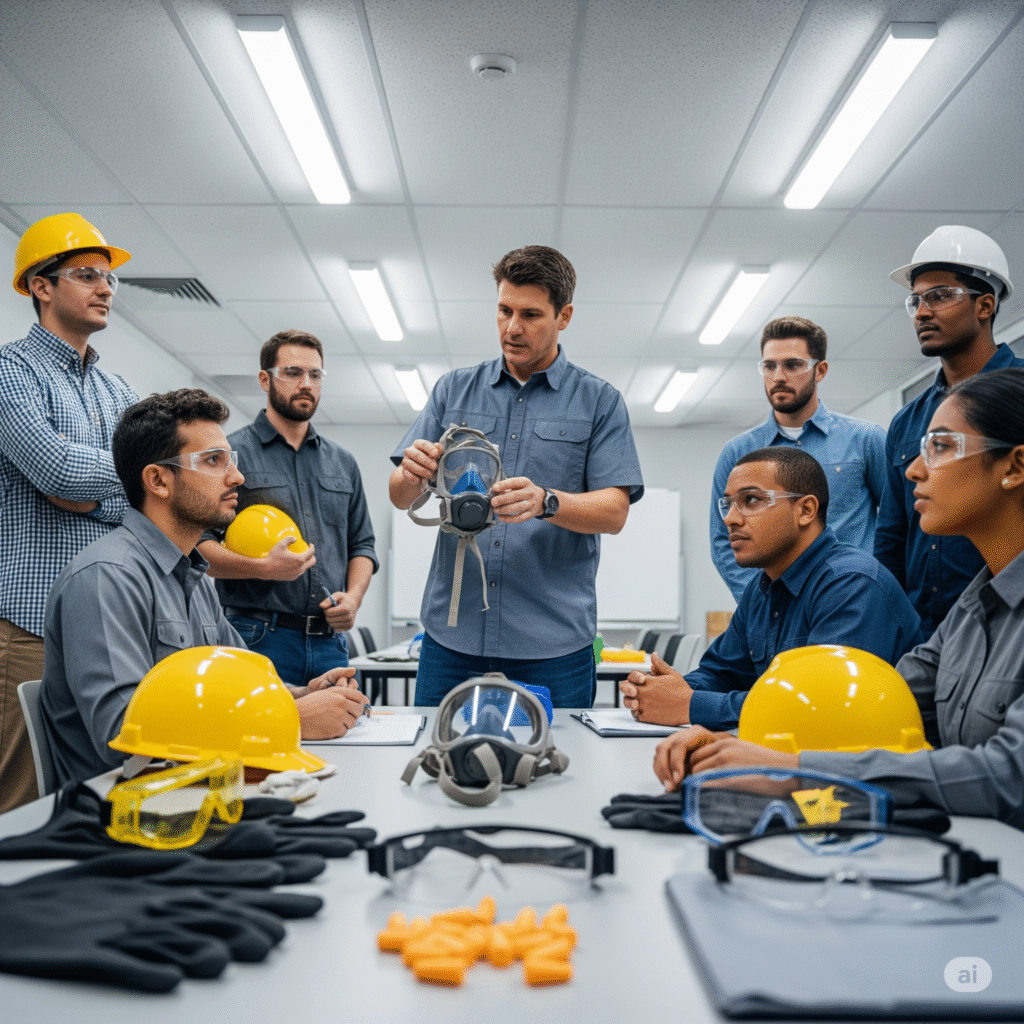
Reinforce the importance of:
- Reporting damaged or missing bonding equipment
- Following proper procedures when transferring flammable materials
- Recognizing warning signs of static buildup (sparks, shocks, etc.)
Interactive Toolbox Talks and scenario-based drills can significantly enhance retention and response capability.
Regulatory Guidelines and Standards
Several safety bodies provide guidelines for controlling static electricity in hazardous environments:
- NFPA 77: Recommended Practice on Static Electricity
- OSHA 29 CFR 1910.106: Flammable Liquids
- ATEX Directive (Europe) for explosive atmospheres
- CSA Z462: Workplace electrical safety standards in Canada
Compliance with these standards not only ensures safety but also protects against regulatory penalties and liabilities.
Technology Spotlight: Static Dissipation Systems
Advanced facilities now use active static control systems, such as:
- Ionizing blowers that neutralize static on surfaces and air
- Static monitoring systems with real-time alerts
- Ground verification devices to ensure bonding is intact before operations begin
These innovations can be integrated into automation systems for continuous protection.
Note: Always Re-Evaluate After a Near Miss or Incident
Any static-related event—even without injury—should trigger an immediate reassessment of controls. This is the ideal time to retrain staff, inspect equipment, and upgrade procedures as needed.
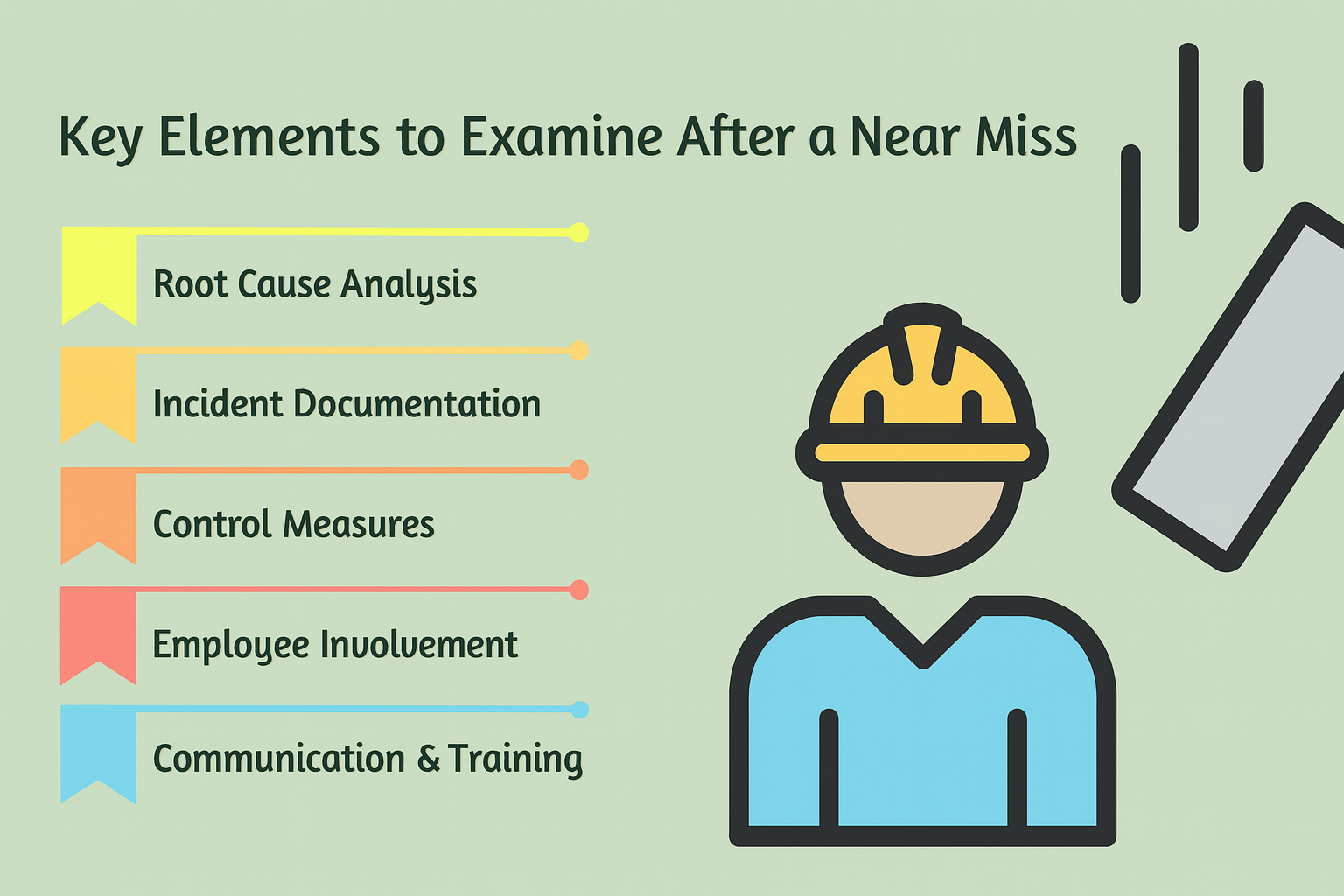
Resources
- Visit our Toolbox Talk Library on OHSE.ca for related topics like flammable liquids, grounding safety, and hazardous materials handling.
- Learn more about static control equipment from EXAIR or Newson Gale – trusted manufacturers with DoFollow links.
- Read NFPA’s official guide: NFPA 77 – Static Electricity.
Conclusion: Controlling Static Electricity in Hazardous Environments Saves Lives
Controlling static electricity in hazardous environments should never be underestimated.
By implementing bonding, grounding, housekeeping, humidity control, and proper training, organizations can effectively eliminate this invisible yet deadly risk.
Make it a non-negotiable part of your safety culture and help your team stay protected.
No comments yet