Introduction
Occupational Health, Safety, and Environment (OHSE) is a comprehensive discipline dedicated to ensuring the well-being of workers and protecting the environment from the adverse effects of industrial activities. A central focus of OHSE is the identification, assessment, and management of hazards in the workplace. Hazards are the underlying sources of potential harm or adverse effects, and understanding them is crucial for creating a safe and healthy work environment.
Understanding Hazards
In the context of OHSE, a hazard is defined as any source of potential damage, harm, or adverse health effects on something or someone. Hazards can lead to accidents, incidents, and environmental damage if not properly controlled. They are inherent in almost every workplace, whether it’s a construction site, manufacturing plant, office, or laboratory.
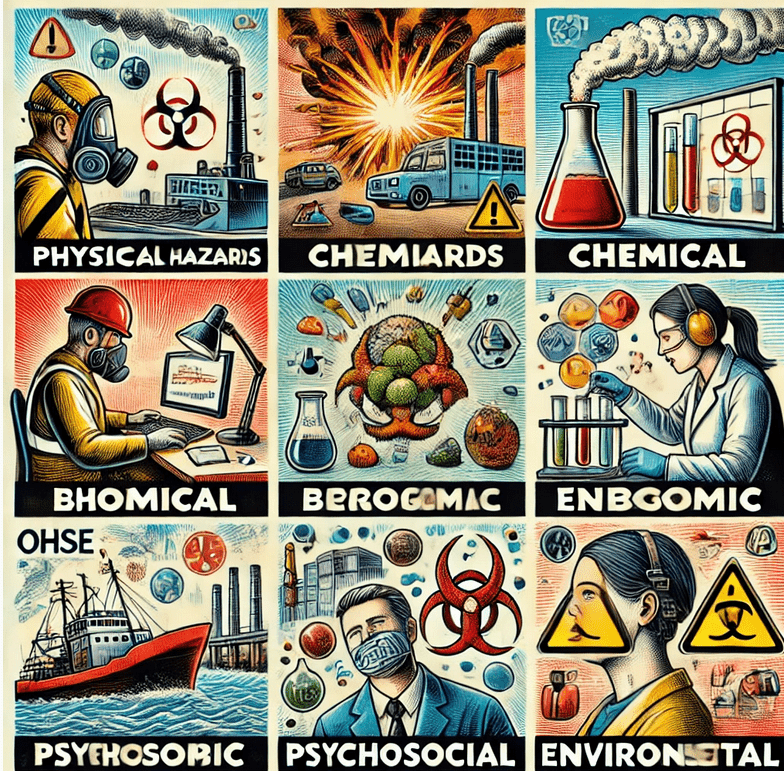
Types of Hazards
Hazards can be broadly categorized into several types based on their nature and the type of harm they may cause:
- Physical Hazards: These are environmental factors that can harm an employee without necessarily touching them. Examples include:
- Noise: High levels of noise can lead to hearing loss.
- Vibration: Continuous vibration can cause long-term damage to the musculoskeletal system.
- Radiation: Exposure to ionizing or non-ionizing radiation can have serious health effects.
- Temperature Extremes: Working in very hot or cold environments can lead to heat stress, hypothermia, or other temperature-related illnesses.
- Chemical Hazards: These involve harmful chemicals that can cause injuries or illnesses through inhalation, ingestion, or skin contact. Examples include:
- Toxic Substances: Chemicals that can cause poisoning or long-term health effects, such as asbestos or lead.
- Flammable Materials: Substances that can easily catch fire, posing risks of burns or explosions.
- Corrosives: Chemicals like acids or bases that can cause severe skin burns or damage to materials.
- Biological Hazards: These involve exposure to harmful biological agents, such as bacteria, viruses, fungi, or other living organisms that can cause infections, allergies, or other health issues. Examples include:
- Bloodborne Pathogens: Such as HIV or hepatitis.
- Molds and Fungi: Which can cause respiratory issues.
- Animal Bites: In some work environments, bites or stings from animals can pose significant risks.
- Ergonomic Hazards: These are related to the design of work tasks, equipment, and workplaces, which can lead to musculoskeletal disorders or repetitive strain injuries. Examples include:
- Improper Workstation Setup: Leading to poor posture and strain.
- Repetitive Movements: Causing tendonitis or carpal tunnel syndrome.
- Manual Handling: Improper lifting techniques that can result in back injuries.
- Psychosocial Hazards: These involve factors that can affect an employee’s mental health and well-being. Examples include:
- Workplace Stress: High levels of stress due to workload or job insecurity.
- Harassment and Bullying: Leading to anxiety, depression, or other mental health issues.
- Workplace Violence: Physical or verbal aggression in the workplace.
- Environmental Hazards: These are hazards that can affect not just the workers but also the environment. Examples include:
- Pollutants: Emissions of harmful substances into the air, water, or soil.
- Waste: Improper disposal of hazardous waste can lead to environmental contamination.
- Natural Disasters: Earthquakes, floods, or other natural events that can disrupt workplace safety.
Hazard Identification and Risk Assessment
The first step in managing hazards under OHSE is identifying them. This involves a systematic process of recognizing, evaluating, and controlling hazards before they can cause harm. The process typically includes:
- Hazard Identification: Identifying all potential hazards present in the workplace.
- Risk Assessment: Evaluating the likelihood and severity of harm that each hazard could cause.
- Control Measures: Implementing measures to eliminate or reduce the risks associated with each hazard.
Control Measures for Hazards
Once hazards are identified and assessed, the next step is to control them to prevent harm. Control measures can be implemented in several ways:
- Elimination: Removing the hazard entirely from the workplace, which is the most effective control measure.
- Substitution: Replacing a hazardous material or process with a less dangerous one.
- Engineering Controls: Isolating people from the hazard through physical changes to the workplace, such as installing ventilation systems or protective barriers.
- Administrative Controls: Changing work practices or procedures to reduce exposure to hazards, such as rotating workers to limit exposure time.
- Personal Protective Equipment (PPE): Providing workers with protective gear, such as helmets, gloves, or respirators, to minimize the impact of hazards.
Conclusion
Hazards are an inherent part of any workplace, but with proper identification, assessment, and control, their risks can be significantly reduced. OHSE plays a vital role in managing these hazards, ensuring the safety, health, and well-being of workers while also protecting the environment. By understanding and addressing the various types of hazards, organizations can create safer and more sustainable workplaces.
No comments yet