Toolbox talks are a cornerstone of workplace safety, especially in high-risk industries like oil and gas. These brief, focused discussions are designed to reinforce safety protocols, encourage hazard awareness, and foster a culture of safety.
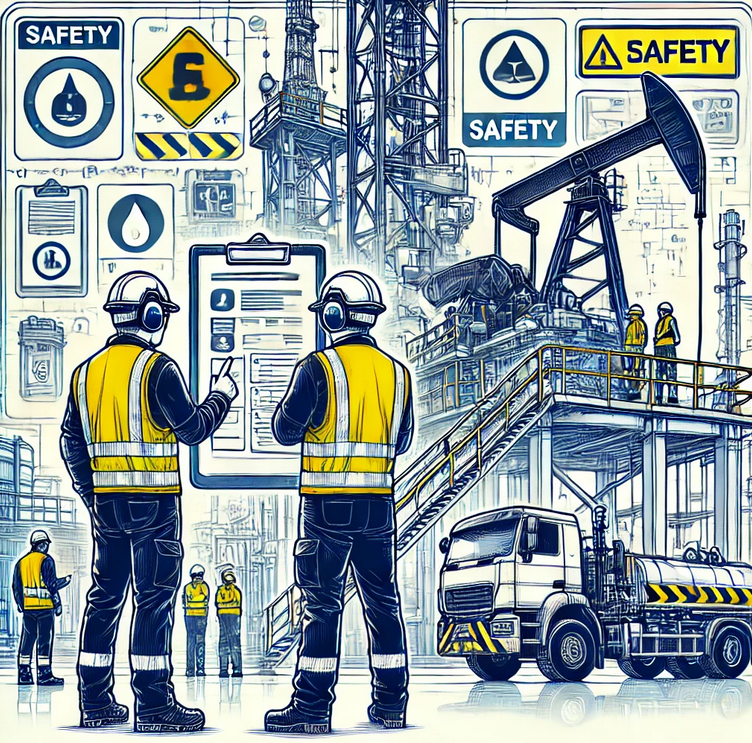
In this comprehensive guide, we’ll explore the importance of toolbox talks, how they promote on-site safety, and best practices for conducting them effectively.
- What Are Toolbox Talks?
- Toolbox Talks in Promoting On-Site Safety
- Key Elements of Effective Toolbox Talks
- Best Practices for Conducting Toolbox Talks
- Common Toolbox Talk Topics in the Oil and Gas Industry
- Measuring the Impact of Toolbox Talks
- Challenges and Solutions in Implementing Toolbox Talks
- Conclusion
What Are Toolbox Talks?
Toolbox talks are informal safety meetings held before the start of a work shift. These sessions, typically lasting 10 to 15 minutes, focus on specific safety issues relevant to the tasks at hand.
They serve as an opportunity for supervisors and workers to discuss potential hazards, share experiences, and review safety procedures.
Benefits of Toolbox Talks
- Improved Hazard Awareness: Regular discussions help workers identify and address risks proactively.
- Enhanced Communication: Encourages open dialogue between team members and supervisors.
- Increased Compliance: Reinforces adherence to safety regulations and company policies.
- Better Team Cohesion: Builds trust and a shared commitment to safety within the team.
Learn more about the importance of regular safety talks from the National Safety Council (DoFollow link).
Toolbox Talks in Promoting On-Site Safety
1. Encouraging a Proactive Safety Culture
Toolbox talks empower workers to take ownership of their safety. By highlighting potential risks and preventive measures, they foster a mindset of vigilance and responsibility.
2. Addressing Site-Specific Hazards
Every worksite has unique safety challenges. Toolbox talks provide an opportunity to address hazards specific to the current project, such as working at heights, handling hazardous chemicals, or operating heavy machinery.
3. Reinforcing Regulatory Compliance
Toolbox talks ensure that workers are familiar with relevant safety regulations, such as OSHA standards. Compliance reduces the likelihood of accidents and legal liabilities.
Key Elements of Effective Toolbox Talks
1. Preparation
- Choose a relevant topic based on the day’s tasks or recent incidents.
- Gather supporting materials, such as safety guidelines, equipment, or real-life examples.
- Ensure the session is concise and focused.
2. Presentation
- Use clear, simple language to ensure everyone understands.
- Engage the audience with questions or discussions.
- Demonstrate safety practices or use visual aids when possible.
3. Follow-Up
- Summarize the key points at the end of the talk.
- Encourage workers to ask questions or share feedback.
- Document the session for compliance purposes.
Best Practices for Conducting Toolbox Talks
1. Choose the Right Setting
Conduct toolbox talks in a quiet, comfortable area where participants can focus without distractions. On-site locations near the task area can enhance relevance.
2. Keep It Interactive
Encourage worker participation by asking questions, sharing scenarios, and inviting feedback. Interaction ensures better engagement and retention of safety information.
3. Make It Routine
Schedule toolbox talks consistently, such as at the start of each shift. Regularity emphasizes their importance and integrates safety into daily workflows.
4. Use Real-Life Examples
Refer to recent incidents or near-misses to make discussions relatable. Workers are more likely to engage when they see the practical application of safety measures.
5. Provide Takeaways
Distribute handouts or summaries of the topics discussed. These resources can reinforce learning and serve as a reference.
Explore effective ways to conduct toolbox talks from Safety+Health Magazine (DoFollow link).
Common Toolbox Talk Topics in the Oil and Gas Industry
1. Working at Heights
Discuss proper use of fall protection equipment, ladder safety, and scaffolding protocols.
2. Hazardous Materials Handling
Review proper storage, handling, and disposal of chemicals, as well as PPE requirements.
3. Fire and Explosion Risks
Highlight fire prevention measures, emergency response plans, and equipment maintenance.
4. Heat Stress and Fatigue
Educate workers on recognizing symptoms of heat-related illnesses and staying hydrated.
5. Machinery and Equipment Safety
Demonstrate safe operation, regular maintenance, and the importance of lockout/tagout procedures.
Measuring the Impact of Toolbox Talks
To ensure toolbox talks are effective in promoting on-site safety, consider the following metrics:
- Worker Feedback: Gather input on the relevance and clarity of the sessions.
- Incident Rates: Monitor changes in the frequency of accidents or near-misses.
- Participation Levels: Track attendance and engagement during talks.
Challenges and Solutions in Implementing Toolbox Talks
1. Lack of Engagement
Workers may view toolbox talks as routine and unimportant. To overcome this, vary the topics and presentation styles to keep sessions interesting.
2. Time Constraints
In fast-paced industries like oil and gas, finding time for safety meetings can be challenging. Keep talks concise and integrate them into pre-shift routines.
3. Language Barriers
In diverse workforces, language differences can hinder understanding. Provide multilingual materials or interpreters when necessary.
Conclusion
Toolbox talks are a powerful tool in promoting on-site safety, fostering communication, and reinforcing a culture of vigilance. By addressing site-specific hazards, encouraging proactive behaviors, and emphasizing regulatory compliance, toolbox talks reduce risks and enhance worker well-being.
When conducted effectively, these brief sessions can make a lasting impact on the safety and efficiency of any workplace. Start incorporating toolbox talks into your routine today—because safety begins with communication.
No comments yet