An effective workplace safety training program is essential for reducing accidents, minimizing risks, and ensuring compliance with health and safety regulations.
Whether you’re managing a manufacturing plant, a construction site, or an office environment, a well-designed safety training program empowers employees to recognize hazards, follow safety protocols, and protect themselves and others.
This article outlines 12 key steps to building a successful workplace safety training program that keeps employees safe and engaged.
- 1. Conduct a Workplace Risk Assessment
- 2. Set Clear Safety Objectives
- 3. Develop a Comprehensive Training Plan
- 4. Tailor Training to Specific Roles
- 5. Use a Variety of Training Methods
- 6. Ensure Compliance with Regulations
- 7. Provide Personal Protective Equipment (PPE) Training
- 8. Make Training Interactive and Engaging
- 9. Conduct Regular Safety Drills
- 10. Evaluate and Update the Training Program
- 11. Encourage a Safety Culture
- 12. Track and Document Training Progress
1. Conduct a Workplace Risk Assessment
Before developing a safety training program, it’s important to conduct a thorough risk assessment of the workplace. This will help identify potential hazards, risks, and areas where safety training is needed.
Key Considerations:
- Analyze past accident and injury reports.
- Assess both physical and environmental hazards (e.g., equipment, chemical exposure, ergonomics).
- Identify specific training needs for different roles or departments.
2. Set Clear Safety Objectives
Once you’ve identified the risks, set clear objectives for the safety training program. The objectives should align with your company’s overall safety goals and regulatory compliance requirements.
Examples of Objectives:
- Reduce workplace injuries by 20% within a year.
- Ensure 100% compliance with PPE usage.
- Train all employees on emergency evacuation procedures.
3. Develop a Comprehensive Training Plan
Create a training plan that includes the content, schedule, and delivery method for each aspect of the safety program. The plan should cover both general safety topics and job-specific risks.
Components of a Training Plan:
- Topics: General safety, emergency procedures, equipment use, ergonomics, chemical handling, etc.
- Frequency: Annual safety refreshers, onboarding training, and additional sessions for new equipment or processes.
- Format: Classroom, e-learning, on-the-job training, or a combination.
4. Tailor Training to Specific Roles
Different roles within an organization face different risks. Tailoring safety training to the specific duties and hazards of each role ensures that employees receive relevant, practical information.
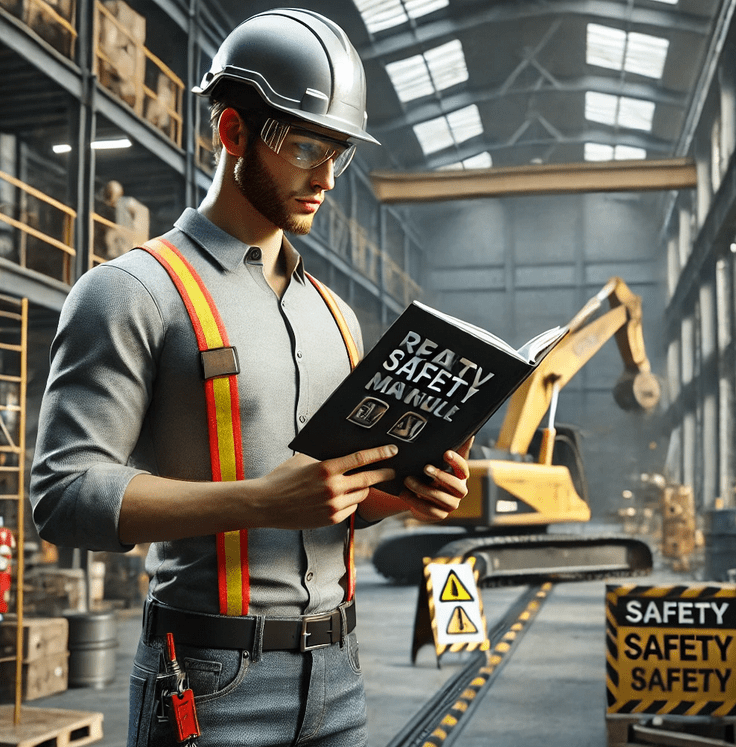
Tailoring Tips:
- Train machine operators on lockout/tagout procedures.
- Provide office workers with ergonomic safety and fire evacuation training.
- Ensure chemical handlers receive detailed training on handling hazardous materials and using protective gear.
5. Use a Variety of Training Methods
Different employees learn in different ways, so it’s important to incorporate a mix of training methods to engage everyone. Consider using a combination of classroom-style training, hands-on demonstrations, videos, and e-learning modules.
Popular Training Methods:
- Instructor-led training: Effective for large groups and interactive discussions.
- E-learning: Provides flexibility and allows employees to learn at their own pace.
- On-the-job training: Great for hands-on tasks and practical safety demonstrations.
- Simulations and role-playing: Useful for emergency drills and real-life hazard scenarios.
6. Ensure Compliance with Regulations
Ensure that your safety training program is in compliance with all relevant industry regulations and standards, such as OSHA (Occupational Safety and Health Administration) in the U.S. or similar regulatory bodies in your region.
Steps for Compliance:
- Review local, state, and national safety regulations.
- Update training content regularly to reflect changes in safety laws or regulations.
- Document all training sessions and keep records of employee certifications and attendance.
7. Provide Personal Protective Equipment (PPE) Training
Training employees on the correct use of PPE is essential, especially in industries where hazardous materials, chemicals, or machinery are used. Employees should understand when PPE is necessary, how to wear it properly, and how to maintain it.
Key Points for PPE Training:
- Demonstrate the correct way to wear PPE (e.g., gloves, masks, goggles).
- Explain how to inspect PPE for damage before use.
- Provide guidelines for cleaning and storing PPE to maintain its effectiveness.
8. Make Training Interactive and Engaging
Interactive and engaging training sessions help employees retain information better. Encourage active participation through group discussions, quizzes, safety scenarios, and hands-on practice.
Engagement Tips:
- Use quizzes or tests to reinforce key safety concepts.
- Encourage employees to share safety concerns and experiences.
- Conduct safety demonstrations with real tools, equipment, or PPE.
- Gamify certain elements of the training with rewards for participation.
9. Conduct Regular Safety Drills
Emergency preparedness is a crucial part of any safety program. Regularly conducting safety drills, such as fire evacuation or chemical spill response drills, ensures that employees know how to react in the event of an emergency.
Examples of Safety Drills:
- Fire drills: Practice evacuations to ensure everyone knows the exit routes.
- Chemical spill drills: Teach employees the correct steps to contain and report hazardous spills.
- First aid response: Ensure that employees are familiar with the location of first aid kits and how to use them.
10. Evaluate and Update the Training Program
A successful safety training program is never static. Regularly evaluate the effectiveness of the program and make necessary updates based on employee feedback, changes in workplace hazards, and updates to safety regulations.
Evaluation Methods:
- Use surveys or feedback forms after training sessions.
- Monitor workplace injury reports and near-misses to assess training effectiveness.
- Review and revise training materials to address any new hazards or regulations.
11. Encourage a Safety Culture
Building a culture of safety starts with leadership. Encourage managers and supervisors to set an example by following safety protocols, attending training, and promoting safety as a core company value.
Ways to Build a Safety Culture:
- Celebrate safety achievements (e.g., accident-free days or departments).
- Integrate safety goals into performance reviews.
- Recognize and reward employees who demonstrate a commitment to safety.
12. Track and Document Training Progress
To ensure accountability and compliance, it’s essential to keep detailed records of all safety training activities. Document who attended, what topics were covered, and when follow-up training is scheduled.
Tracking Tips:
- Use a Learning Management System (LMS) to track employee progress and certifications.
- Maintain records of training attendance and assessments.
- Set reminders for refresher training to ensure ongoing compliance.
A successful workplace safety training program is a crucial investment in the health, safety, and productivity of your workforce.
By following these 12 steps, safety managers can develop a comprehensive program that reduces risks, fosters a culture of safety, and ensures that employees are prepared to handle workplace hazards.
Regular evaluations and updates will keep the program effective, ensuring that employees stay informed and protected.
No comments yet