Preventing Chemical Exposure in Auto Repair Shops is a top priority for ensuring worker health, safety, and regulatory compliance.
Mechanics are routinely exposed to hazardous substances like solvents, oils, brake fluids, and cleaning agents, which pose risks ranging from skin irritation to long-term respiratory damage.
Without the right controls and awareness, these chemicals can harm not only workers but also the environment.
- Why Chemical Safety Matters in Auto Repair Environments
- Recognizing Common Hazardous Chemicals in Repair Shops
- Best Practices for Preventing Chemical Exposure in Auto Repair Shops
- Training and Safety Data Sheets (SDS)
- Implementing a Chemical Hygiene Plan
- Protecting the Environment
- Internal Link Suggestions
- Conclusion: Prioritize Chemical Safety to Protect Your Team
Why Chemical Safety Matters in Auto Repair Environments
Auto repair shops use a wide range of chemicals daily. These substances—while essential—can introduce serious occupational hazards. Prolonged or unprotected exposure to chemicals like benzene, toluene, and acetone may cause nervous system damage, skin disorders, respiratory illness, and even cancer.
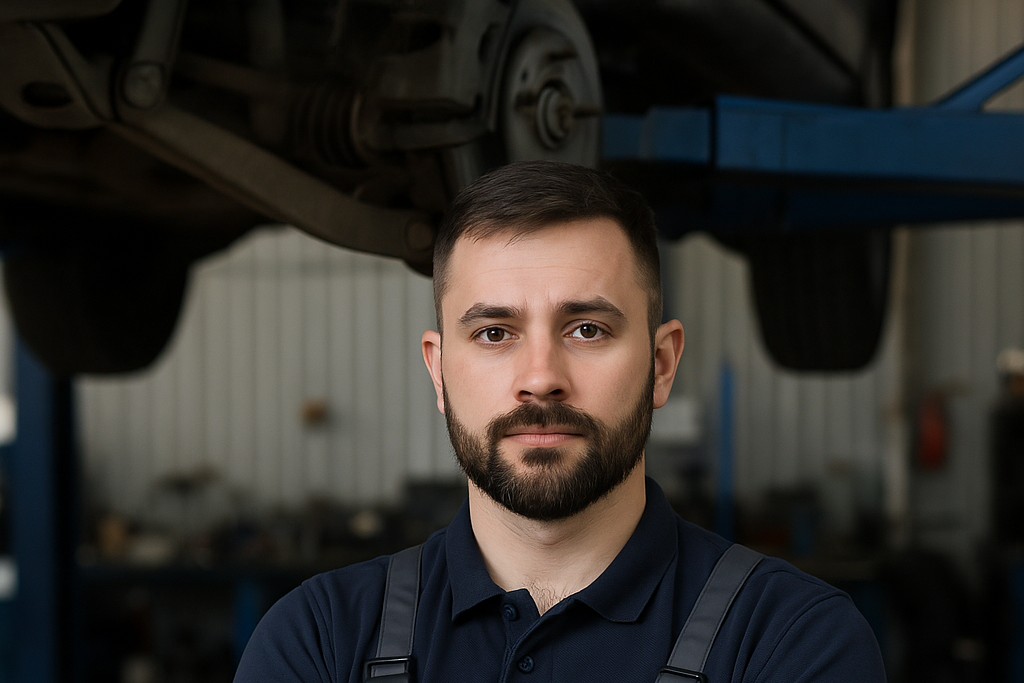
Workers may not always recognize the long-term risks of minor spills, fumes, or splashes. According to Canadian Centre for Occupational Health and Safety (CCOHS), employers are legally required to protect workers from exposure to hazardous products under WHMIS (Workplace Hazardous Materials Information System).
Recognizing Common Hazardous Chemicals in Repair Shops

Some of the most common chemical hazards in repair environments include:
- Solvents (used in degreasers and cleaners)
- Brake fluids and antifreeze
- Paints and hardeners
- Battery acids
- Welding fumes
- Fuel vapors and engine oils
Each of these can pose inhalation, ingestion, or skin absorption risks.
Best Practices for Preventing Chemical Exposure in Auto Repair Shops
Proper Storage and Labeling
Ensure all hazardous chemicals are stored in labeled, sealed containers away from heat or open flames. Use flame-resistant cabinets for flammable products.
Under WHMIS 2015, all containers must have appropriate supplier and workplace labels.
Use of Personal Protective Equipment (PPE)
Mechanics should wear:
- Chemical-resistant gloves
- Safety goggles or face shields
- Coveralls or aprons
- Respiratory protection (when working with sprays or vapors)
Provide PPE training and routine equipment checks to prevent failure during use.
Effective Ventilation Systems
Install local exhaust ventilation (LEV) near workbenches, paint booths, or welding stations. Ensure general ventilation meets indoor air quality standards.
In closed garages, carbon monoxide and vapor build-up can become lethal without proper airflow.
Spill Management and Disposal
Spill kits with absorbents and neutralizers should be available in every bay. Train employees on spill response procedures.
Waste fluids must be stored in labeled drums and picked up by certified disposal services, as per Environment and Climate Change Canada guidelines.
Training and Safety Data Sheets (SDS)
All employees must have access to and be trained in the use of Safety Data Sheets (SDS).
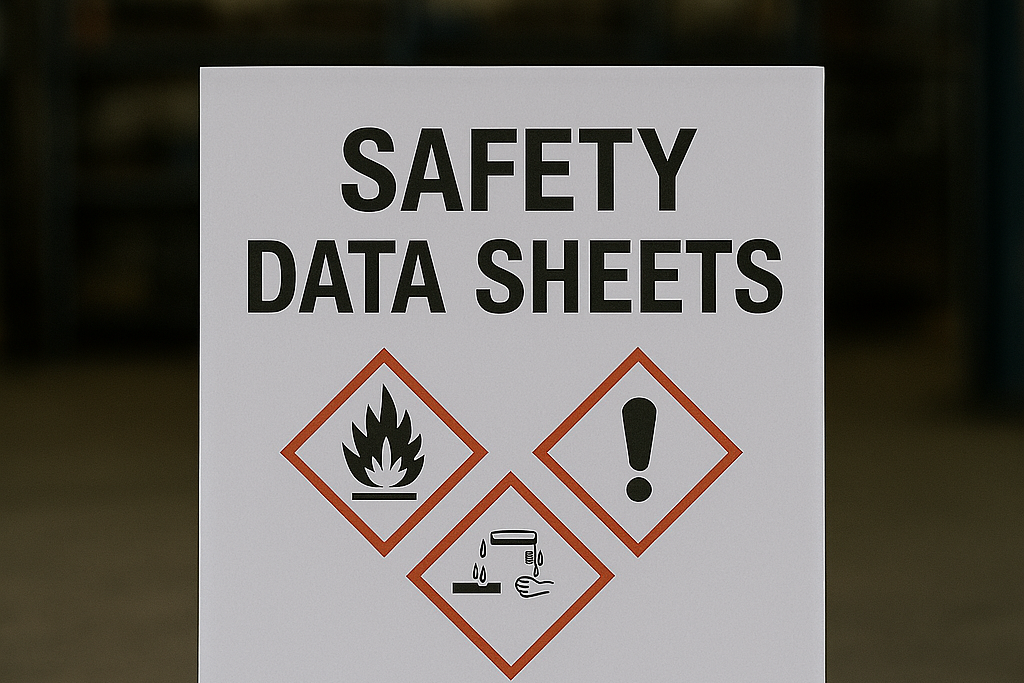
These documents provide critical information on safe handling, PPE requirements, first aid, and disposal of chemicals. Conduct refresher training yearly or when introducing new substances.
Implementing a Chemical Hygiene Plan
A well-documented Chemical Hygiene Plan should include:
- A list of hazardous substances used on-site
- Responsibilities of supervisors and employees
- Procedures for safe handling and emergency response
- PPE maintenance and inspection schedules
- WHMIS training logs
Such a plan is not only a best practice but can protect employers from liability during inspections by regulatory bodies like WorkSafeBC or OHSA Ontario.
Protecting the Environment
Chemical spills can pollute local water systems if not contained. Installing oil-water separators, using drip pans, and following environmental safety protocols can help shops avoid fines and protect the community.
For Canadian readers, OHSE.ca offers resources on environmental safety practices and local training providers.
Internal Link Suggestions
- Learn more about Safe Lifting Techniques for Mechanics
- Explore our guide on Fire Safety for Auto Repair Shops
Conclusion: Prioritize Chemical Safety to Protect Your Team
Preventing Chemical Exposure in Auto Repair Shops is a non-negotiable part of occupational health and safety.

By implementing proper controls, providing training, and fostering a safety culture, shop owners can protect their teams from immediate harm and long-term health issues.
A proactive approach saves lives, prevents legal issues, and creates a workplace workers can trust.
No comments yet