Digital twins are revolutionizing safety planning in oil and gas facilities, transforming how the industry mitigates risks, improves operational efficiency, and enhances worker safety.
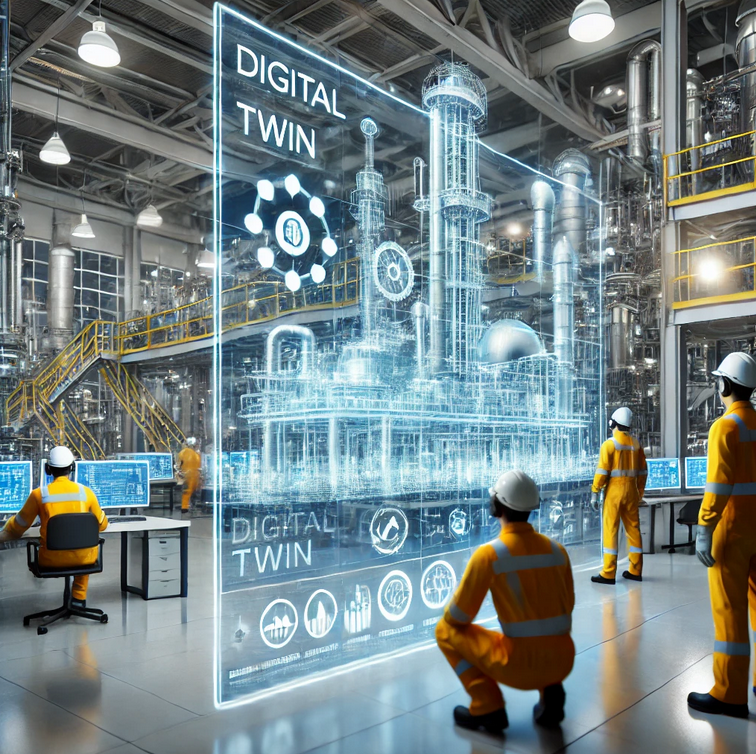
This groundbreaking technology creates virtual replicas of physical assets, enabling real-time monitoring, predictive analysis, and informed decision-making.
In this article, we explore how digital twins are reshaping safety planning in oil and gas facilities, their benefits, implementation strategies, and future potential.
- What Are Digital Twins in the Oil and Gas Industry?
- Why Digital Twins are Revolutionizing Safety Planning in Oil and Gas Facilities
- Benefits of Digital Twins in Oil and Gas Safety Planning
- Applications of Digital Twins in Oil and Gas Facilities
- How to Implement Digital Twins in Safety Planning
- Challenges in Adopting Digital Twins
- Future Trends in Digital Twins for Oil and Gas Safety
- Conclusion
What Are Digital Twins in the Oil and Gas Industry?
Digital twins are virtual models that mirror physical assets, processes, or systems in real-time. By integrating data from sensors, Internet of Things (IoT) devices, and advanced analytics, digital twins simulate real-world operations, allowing companies to visualize, monitor, and optimize their processes.
How Digital Twins Work:
- Data Collection: Sensors installed on equipment or processes collect real-time data.
- Simulation: The collected data feeds into a digital model that replicates physical conditions.
- Analysis: Predictive analytics identify potential safety risks and operational inefficiencies.
- Optimization: Insights from the digital twin inform proactive safety measures and process improvements.
Why Digital Twins are Revolutionizing Safety Planning in Oil and Gas Facilities
1. Proactive Hazard Identification
Digital twins enable companies to identify risks before they become incidents. For instance, a digital twin can simulate a pipeline’s behavior under varying pressure levels, predicting potential failures.
2. Enhanced Emergency Response
By visualizing real-time scenarios, digital twins help plan and execute effective emergency responses. Workers and management can rehearse responses to hypothetical situations, such as gas leaks or equipment failures.
3. Real-Time Monitoring
Digital twins provide continuous insights into equipment performance and environmental conditions. This allows for immediate intervention if safety thresholds are breached.
4. Cost-Effective Safety Improvements
Implementing safety enhancements through virtual simulations reduces the need for expensive physical testing, saving resources while ensuring thorough risk assessment.
Learn more about the potential of digital twins in the oil and gas sector at IBM Digital Twin Solutions (DoFollow link).
Benefits of Digital Twins in Oil and Gas Safety Planning
1. Improved Worker Safety
By predicting hazards and optimizing work environments, digital twins minimize risks to workers.
2. Enhanced Asset Integrity
Regular monitoring through digital twins ensures equipment remains in optimal condition, reducing the likelihood of failures.
3. Streamlined Compliance
Digital twins help companies adhere to industry safety regulations by simulating compliance scenarios and monitoring key performance indicators.
4. Reduced Downtime
Predictive maintenance enabled by digital twins prevents unplanned shutdowns, ensuring safer and uninterrupted operations.
Applications of Digital Twins in Oil and Gas Facilities
1. Equipment Monitoring
Digital twins monitor the health of critical machinery, such as pumps and compressors, flagging anomalies before they escalate.
2. Facility Design and Optimization
During the design phase of a facility, digital twins simulate layouts to ensure ergonomic and safe working conditions.
3. Pipeline Safety
By replicating pipeline networks, digital twins identify vulnerabilities such as corrosion or pressure fluctuations, enhancing pipeline integrity.
4. Environmental Safety
Digital twins track environmental parameters, such as emissions and temperatures, ensuring compliance with environmental safety standards.
Discover more about pipeline safety innovations at National Energy Technology Laboratory (DoFollow link).
How to Implement Digital Twins in Safety Planning
1. Define Objectives
Determine specific safety goals, such as reducing incidents or improving compliance, to guide the digital twin’s implementation.
2. Collect Accurate Data
Install IoT sensors and devices to gather comprehensive data on equipment and processes.
3. Integrate with Existing Systems
Ensure the digital twin integrates seamlessly with current safety management systems for centralized monitoring.
4. Train Personnel
Educate staff on interpreting digital twin data and incorporating insights into safety practices.
5. Monitor and Evolve
Regularly update the digital twin with new data to maintain accuracy and relevance.
Challenges in Adopting Digital Twins
1. High Initial Investment
Developing and deploying digital twins requires significant financial resources. However, the long-term benefits often outweigh the upfront costs.
2. Data Security Concerns
Protecting the vast amounts of data generated by digital twins is essential to avoid cyber threats.
3. Integration Complexity
Combining digital twin systems with legacy infrastructure may present technical challenges.
Future Trends in Digital Twins for Oil and Gas Safety
1. Integration with Artificial Intelligence
AI-powered digital twins will provide deeper insights and automate safety interventions.
2. Expansion into Renewable Energy
As the industry shifts towards renewables, digital twins will play a pivotal role in managing wind farms and solar power plants.
3. Enhanced Visualization Tools
Advanced 3D and virtual reality features will improve the usability and accessibility of digital twins.
Explore the evolving role of AI in digital twin technology at Microsoft AI and IoT Solutions (DoFollow link).
Conclusion
Digital twins are revolutionizing safety planning in oil and gas facilities by providing unprecedented visibility into operations, predicting hazards, and optimizing safety measures. As the industry embraces this transformative technology, the potential for safer, more efficient operations continues to grow.
Investing in digital twins not only safeguards workers and assets but also drives innovation and sustainability in the oil and gas sector.
Start leveraging digital twins today to ensure a safer and smarter future for your facilities.
No comments yet