The automotive manufacturing industry is a complex and fast-paced environment that requires the use of heavy machinery, robotics, and various forms of energy to assemble vehicles. Among the many risks that workers face, hazardous energy has been identified as one of the most significant dangers.
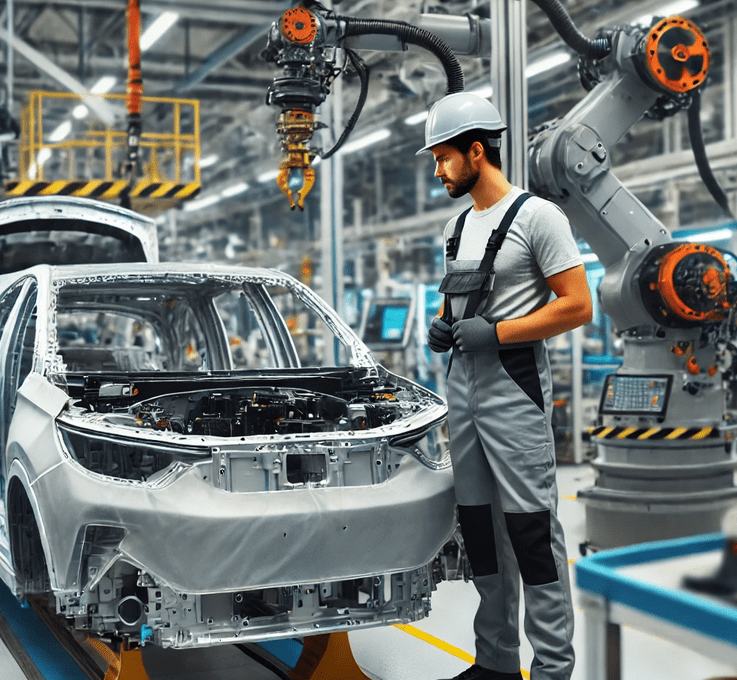
Improper control of hazardous energy, also known as “lockout/tagout” (LOTO) failures, can lead to severe injuries, including amputations, electrocutions, and fatalities. In fact, according to safety agencies, hazardous energy is responsible for thousands of workplace injuries each year, many of which are preventable.
This article explores the risks associated with hazardous energy in automotive manufacturing, the importance of proper energy control procedures, and best practices for keeping workers safe.
- 1. What Is Hazardous Energy?
- 2. The Dangers of Hazardous Energy in Automotive Manufacturing
- 3. Lockout/Tagout (LOTO) Procedures: The Key to Controlling Hazardous Energy
- 4. Challenges in Managing Hazardous Energy in Automotive Manufacturing
- 5. Best Practices for Controlling Hazardous Energy
- 6. Case Study: Preventing Hazardous Energy Accidents in Automotive Manufacturing
1. What Is Hazardous Energy?
Hazardous energy refers to the energy sources found in industrial machines and equipment that could harm workers during maintenance, servicing, or repairs. These energy sources include electrical, mechanical, hydraulic, pneumatic, chemical, and thermal energy. When energy is released or activated unexpectedly—while equipment is undergoing maintenance, for instance—it can result in catastrophic accidents.
Types of Hazardous Energy in Automotive Manufacturing:
- Electrical Energy: Power from machinery, robotics, and control systems.
- Mechanical Energy: Energy stored in moving parts or systems under tension, such as belts, gears, and springs.
- Hydraulic and Pneumatic Energy: Pressure-driven systems that power various mechanical components.
- Chemical Energy: Energy stored in substances that can be released during chemical reactions, such as in batteries or during chemical processes.
- Thermal Energy: Heat from furnaces, welding, or cutting operations.
2. The Dangers of Hazardous Energy in Automotive Manufacturing
In an industry reliant on automation, robotics, and heavy equipment, workers are constantly interacting with machinery that uses hazardous energy. One small mistake in controlling this energy—such as improper lockout/tagout procedures or equipment not being properly de-energized—can result in severe injuries or fatalities.
Common Hazards:
- Unexpected Machine Activation: Machinery that starts unexpectedly during maintenance can cause crush injuries or amputations.
- Release of Stored Energy: Hydraulic systems or springs under tension can suddenly release energy, causing machinery to move without warning.
- Electrical Shocks or Electrocution: Live electrical systems not properly de-energized during servicing can lead to fatal electrocution.
- Burns from Hot Surfaces: Thermal energy stored in welding or furnace operations can cause burns if equipment is not properly cooled before maintenance.
3. Lockout/Tagout (LOTO) Procedures: The Key to Controlling Hazardous Energy
One of the most effective ways to control hazardous energy and protect workers is through lockout/tagout (LOTO) procedures. LOTO ensures that machinery is properly shut off and cannot be started up again until maintenance or repair work is completed.
Key Elements of LOTO:
- Lockout Devices: Physical locks that prevent machinery from being powered on.
- Tagout Devices: Warning tags that inform workers the machinery is being serviced and must not be activated.
- Energy Isolation: Disconnecting machinery from its energy sources, including electrical power, hydraulic pressure, or mechanical tension.
- Verification: Testing to ensure that the energy has been successfully isolated and the machinery is not functional.
Importance of Proper LOTO Procedures:
LOTO procedures are vital in preventing accidental machine startup or the release of stored energy while repairs or maintenance are being performed. Proper training, clear communication, and strict enforcement of LOTO protocols can significantly reduce the risk of accidents caused by hazardous energy.
4. Challenges in Managing Hazardous Energy in Automotive Manufacturing
Despite the effectiveness of LOTO procedures, many manufacturers face challenges in consistently enforcing safety protocols. Fast-paced production environments and complex machinery can lead to shortcuts or complacency, which increases the risk of accidents.
Common Challenges:
- Pressure to Meet Production Deadlines: Workers may feel rushed and skip safety protocols, such as LOTO, to reduce downtime and meet production targets.
- Inconsistent Training: Workers or contractors may not receive consistent or adequate training on LOTO procedures, leading to unsafe practices.
- Complex Machinery: Automated and robotic systems in automotive manufacturing are complex, and properly de-energizing them for maintenance can be challenging.
- Failure to Verify De-Energization: Even if LOTO procedures are in place, failing to verify that the equipment has been fully de-energized can lead to serious accidents.
Tip: Regular safety audits, ongoing LOTO training, and a strong safety culture are essential for overcoming these challenges and maintaining a safe working environment.
5. Best Practices for Controlling Hazardous Energy
Managing hazardous energy effectively in automotive manufacturing requires a combination of robust safety policies, comprehensive training, and a commitment to continuous improvement. Below are some best practices for reducing the risk of hazardous energy accidents.
a. Develop a Written LOTO Program
Every facility should have a written lockout/tagout program that outlines specific procedures for isolating energy, applying locks and tags, and verifying de-energization. This program should be regularly reviewed and updated to reflect changes in equipment or processes.
b. Conduct Regular LOTO Training
Training is critical to ensuring that all employees, including maintenance workers, operators, and contractors, understand how to safely control hazardous energy. Training should include:
- How to recognize hazardous energy sources.
- How to properly lock and tag machinery.
- How to verify that energy has been isolated.
c. Use Advanced Safety Technology
Consider incorporating advanced safety technologies, such as remote energy isolation devices or automated lockout systems. These technologies can streamline the LOTO process and make it easier to de-energize machinery safely.
d. Perform Routine Inspections and Audits
Conduct regular inspections and audits of your LOTO procedures to ensure compliance. Look for gaps in the program, such as outdated procedures or equipment that hasn’t been maintained, and take corrective action where necessary.
e. Involve Employees in Safety Planning
Encourage workers to participate in safety committees or hazard identification programs. Employees who are directly involved in operating machinery are often the first to identify potential hazards or areas where safety can be improved.
6. Case Study: Preventing Hazardous Energy Accidents in Automotive Manufacturing
An automotive manufacturing plant that specializes in producing vehicle parts experienced several near-miss incidents involving hazardous energy. The root cause was traced back to inconsistent LOTO practices and inadequate training of maintenance personnel.
To address the issue, the plant implemented the following changes:
- Revised LOTO Program: The company updated its LOTO procedures to include more detailed steps for energy isolation and verification.
- Increased Training: All employees received refresher training on hazardous energy control, with an emphasis on hands-on demonstrations.
- Safety Leadership: A safety team was created to conduct weekly LOTO audits and ensure compliance.
After implementing these changes, the plant saw a significant reduction in near-miss incidents and no reported injuries related to hazardous energy for 18 months.
Hazardous energy is a top risk in automotive manufacturing, but it can be effectively managed through proper lockout/tagout procedures, comprehensive training, and a strong safety culture. By taking proactive steps to control hazardous energy, manufacturers can protect their workers from severe injuries and improve overall operational safety.
The automotive industry must prioritize hazardous energy control as a critical part of their health and safety strategies. By staying vigilant, ensuring that workers are well-trained, and committing to continuous improvement, workplaces can minimize the risk of accidents and keep hazardous energy incidents to a minimum.
No comments yet