Shutdowns are a critical part of industrial and manufacturing operations, providing an opportunity to perform maintenance, upgrades, and safety inspections.
However, these periods come with inherent risks due to high-intensity work environments, multiple concurrent tasks, and compressed timelines. Developing an effective shutdown schedule is essential for ensuring operational efficiency, minimizing downtime, and prioritizing safety.
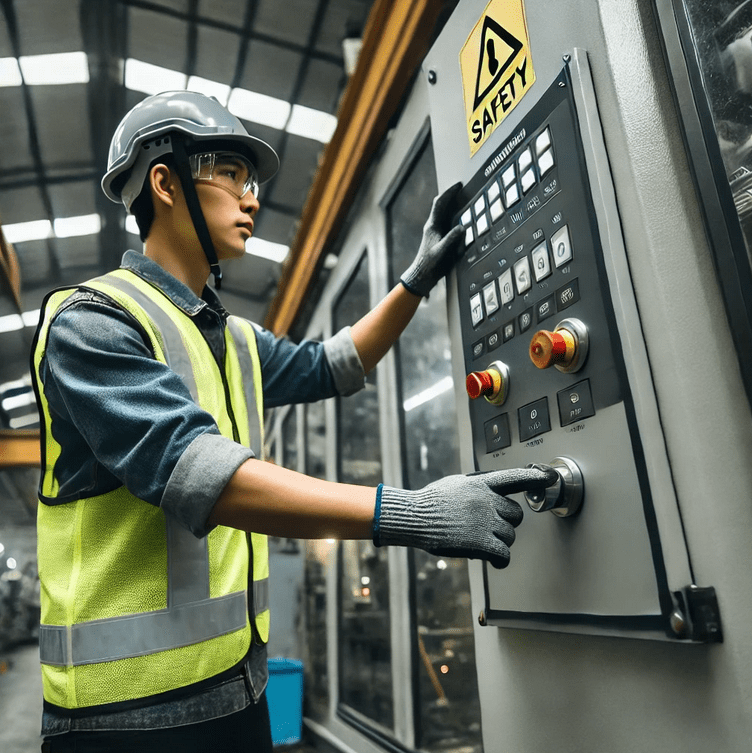
This guide outlines key steps and best practices for creating a shutdown schedule that integrates safety audits and risk management.
Why an Effective Shutdown Schedule Matters
- Minimizes Downtime
A well-structured schedule helps streamline operations, reducing delays and costs associated with unplanned downtime. - Enhances Safety
Incorporating safety audits into the schedule mitigates risks during high-stress shutdown periods. - Improves Efficiency
A detailed plan ensures that all teams know their roles, resources are allocated effectively, and tasks are completed on time. - Ensures Compliance
Regular inspections and adherence to safety protocols keep the organization in line with regulatory requirements.
Steps to Develop an Effective Shutdown Schedule
1. Define Objectives
- Clearly outline the purpose of the shutdown, whether it’s for maintenance, upgrades, inspections, or a combination.
- Identify safety-specific goals, such as completing risk assessments or implementing new safety measures.
2. Assemble a Shutdown Team
- Appoint a shutdown manager to oversee planning and execution.
- Include representatives from operations, maintenance, safety, and management.
- Assign roles for tasks like equipment checks, audits, and emergency response.
3. Conduct a Pre-Shutdown Assessment
- Evaluate equipment, systems, and processes to identify maintenance and safety priorities.
- Review past shutdowns to identify lessons learned and areas for improvement.
4. Develop a Task List
- Break down the shutdown into manageable tasks, including:
- Maintenance activities.
- Safety audits and inspections.
- Equipment upgrades.
- Cleaning and housekeeping.
- Prioritize high-risk tasks and critical repairs.
5. Integrate Safety Audits into the Schedule
- Schedule safety inspections before, during, and after the shutdown.
- Focus on high-risk areas such as confined spaces, electrical systems, and heavy equipment.
- Include time for hazard assessments and implementing corrective actions.
6. Allocate Resources
- Ensure availability of tools, spare parts, and personal protective equipment (PPE).
- Assign skilled personnel for specialized tasks, such as handling hazardous materials or equipment calibration.
7. Establish a Timeline
- Create a timeline with clear milestones and deadlines for each task.
- Include buffer time for unexpected delays or additional repairs.
- Coordinate with all departments to avoid scheduling conflicts.
8. Communicate the Plan
- Share the shutdown schedule with all relevant stakeholders, including employees, contractors, and vendors.
- Provide detailed instructions and safety guidelines.
- Hold pre-shutdown meetings to clarify roles and expectations.
9. Implement Monitoring and Reporting
- Use real-time tracking tools to monitor progress during the shutdown.
- Appoint safety officers to oversee adherence to protocols and conduct on-the-spot inspections.
- Maintain a log of completed tasks and identified issues.
10. Conduct Post-Shutdown Reviews
- Perform a final safety audit to ensure the workplace is hazard-free before resuming operations.
- Debrief the shutdown team to discuss successes and areas for improvement.
- Document findings to inform future shutdowns.
Best Practices for Effective Shutdown Scheduling
- Plan Early
- Start the planning process several months in advance to account for complex tasks and procurement needs.
- Prioritize Safety
- Treat safety audits as integral to the schedule, not as optional add-ons.
- Leverage Technology
- Use scheduling software and digital tools to coordinate tasks and monitor progress.
- Involve All Stakeholders
- Include input from frontline workers who have firsthand experience with equipment and processes.
- Test Emergency Procedures
- Conduct drills during the shutdown to ensure all teams are prepared for potential emergencies.
Key Challenges and How to Overcome Them
- Compressed Timelines
- Mitigation: Break tasks into smaller steps and assign dedicated teams for simultaneous work.
- Resource Constraints
- Mitigation: Cross-train employees and secure external contractors for specialized roles.
- Unanticipated Issues
- Mitigation: Build flexibility into the schedule to accommodate surprises.
Conclusion
An effective shutdown schedule is the backbone of successful maintenance and safety efforts during planned downtime. By incorporating safety audits, prioritizing tasks, and maintaining clear communication, organizations can ensure smooth operations while safeguarding employees and assets. Remember, a proactive approach to planning doesn’t just reduce risks—it sets the stage for long-term operational excellence.
No comments yet