Measure Safety Training Effectiveness at the very beginning of your safety program planning to ensure that time, money, and effort truly lead to safer outcomes.
Too often, companies deliver training sessions, check a compliance box, and move on—without knowing if workers actually learned anything, changed behavior, or reduced risk.

In this guide, we’ll show you why measuring training effectiveness matters, how to do it, and which proven strategies lead to meaningful improvements in workplace safety.
Why You Must Measure Safety Training Effectiveness
A strong safety culture depends on workers understanding and following safe practices. Simply delivering training isn’t enough.
By committing to Measure Safety Training Effectiveness, you can:
- Identify gaps in knowledge or skills
- Improve future training design
- Reduce incidents and injuries
- Boost compliance with OHS regulations
- Demonstrate due diligence to regulators and insurers
Without measurement, you’re guessing whether training works. That’s a risky approach in high-hazard environments where mistakes can cost lives.
Key Principles to Measure Safety Training Effectiveness
1. Set Clear, Measurable Objectives
Begin every training program by defining exactly what you want workers to learn or do differently.
Examples of clear objectives:
- Identify hazardous chemicals by WHMIS labels
- Demonstrate correct lockout/tagout procedures
- Use fall protection equipment properly
By setting measurable objectives, you create benchmarks against which you can assess effectiveness.
2. Use Multiple Levels of Evaluation
The classic Kirkpatrick Model offers four levels to Measure Safety Training Effectiveness:
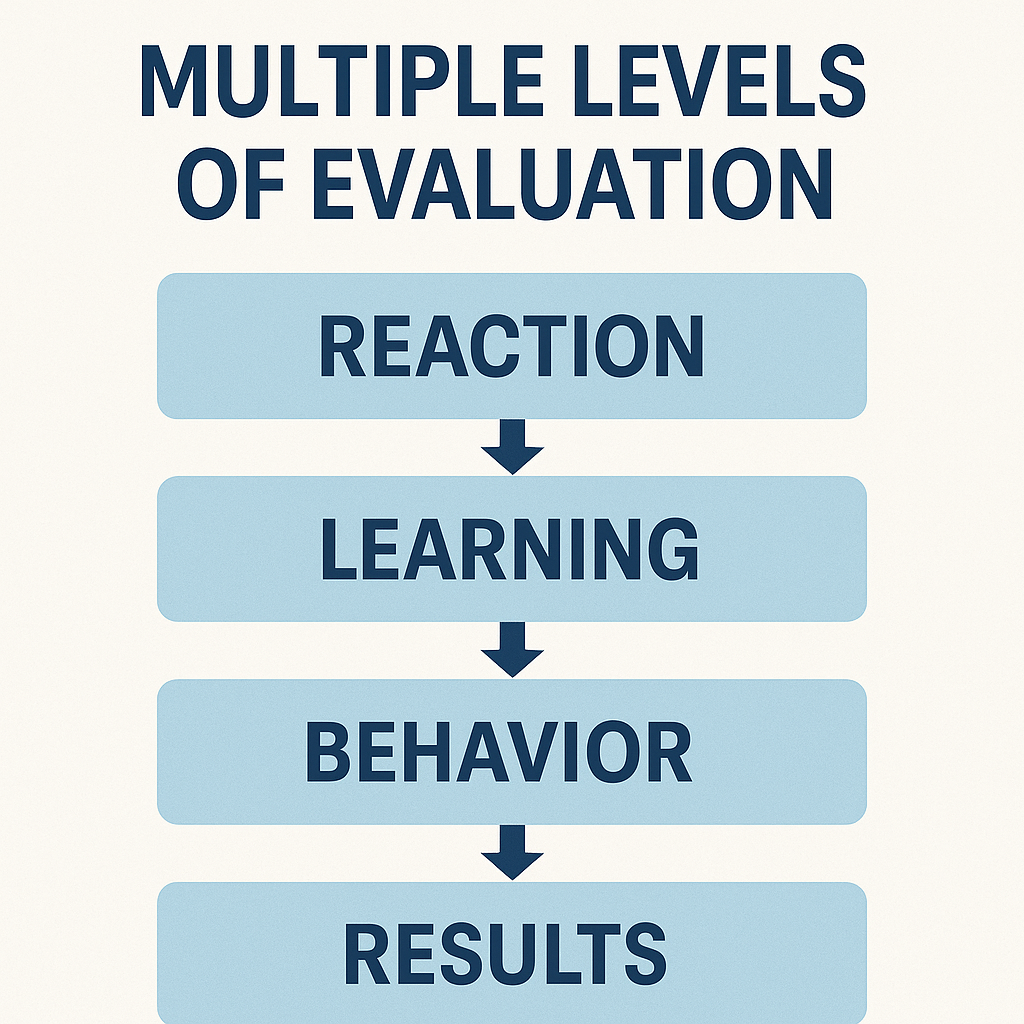
- Reaction: Did participants like the training?
- Learning: Did they acquire knowledge or skills?
- Behavior: Are they applying it on the job?
- Results: Has the training reduced incidents or improved KPIs?
Many companies stop at “Did they like it?” That’s not enough. Aim to evaluate learning, behavior, and results for a true picture.
3. Incorporate Pre- and Post-Tests
Knowledge testing is a direct way to Measure Safety Training Effectiveness.
- Pre-tests show what workers know before training.
- Post-tests demonstrate knowledge gains.
For example, in a WHMIS training session, ask participants to identify hazard pictograms before and after training to measure knowledge growth.
Testing doesn’t have to be formal exams—it can include quizzes, interactive polling, or group activities.
4. Observe On-the-Job Behavior
Classroom training is only valuable if it changes real-world behavior. Supervisors and safety professionals should:
- Conduct field observations
- Use checklists to assess compliance
- Provide coaching and feedback
For instance, after fall protection training, check whether workers actually use harnesses correctly at heights.
Behavioral observation is one of the most powerful tools to Measure Safety Training Effectiveness because it connects learning to safety outcomes.
5. Track Incident and Near Miss Data
Your safety metrics can tell you if training is making a difference.
Compare incident and near-miss reports before and after training on specific hazards. Examples:
- Reduced manual handling injuries after ergonomics training
- Fewer chemical spills following WHMIS refreshers
Safety data is a direct, quantifiable way to Measure Safety Training Effectiveness over time.
For guidance on hazard tracking, see our article on Incident Investigation Best Practices.
6. Use Worker Feedback
Your workers are the best judges of whether training is relevant and understandable. Gather feedback through:
- Post-training surveys
- Focus groups
- Anonymous suggestion boxes
Ask questions like:
- Was the training clear and engaging?
- Do you feel safer or more confident?
- What would improve the training?
Including workers in the evaluation process improves buy-in and relevance.
7. Conduct Safety Audits
Audits and inspections can reveal whether workers follow safe practices and whether training covered critical risks.
For example, during a warehouse safety audit, check if workers:
- Use proper lifting techniques
- Maintain clear aisles
- Follow safe vehicle-pedestrian separation
Safety audits let you Measure Safety Training Effectiveness as part of continuous improvement efforts.
8. Review and Refresh Training Regularly
Regulations and hazards change over time, and so does your workforce. Even effective training can lose impact without reinforcement.
Commit to:
- Annual or biannual refresher training
- Updates when new equipment or procedures are introduced
- Short toolbox talks to reinforce critical topics
Refresher sessions help maintain safety knowledge and reduce complacency.
Tools and Techniques to Measure Safety Training Effectiveness
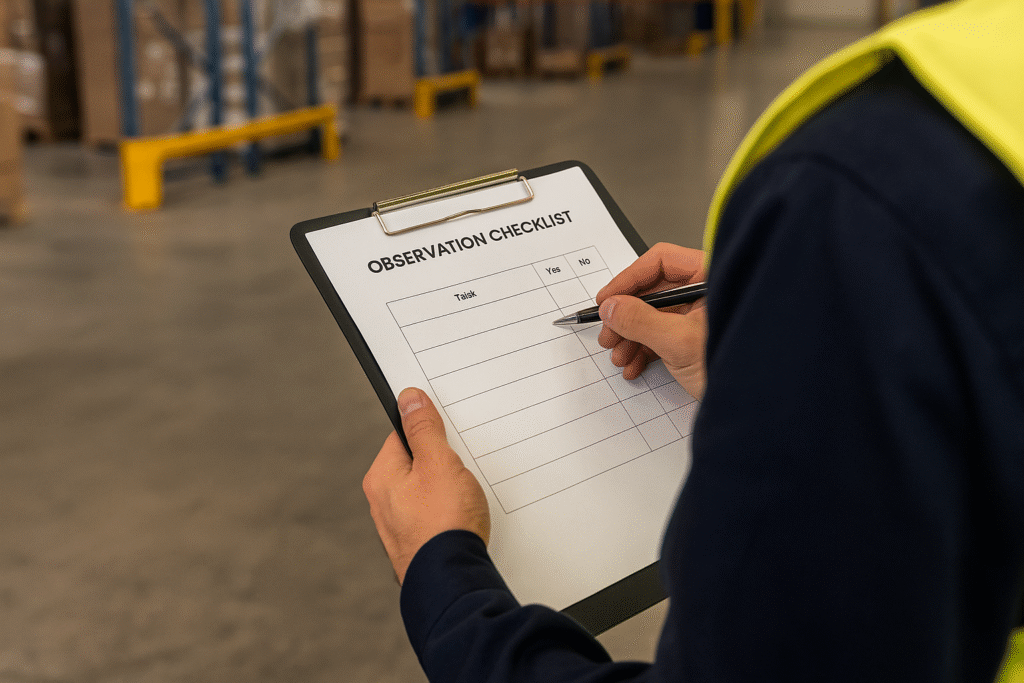
To support your evaluation efforts, consider these tools:
- Learning Management Systems (LMS) to track test scores and participation
- Observation checklists for supervisors
- Incident reporting software
- Survey and feedback tools
- Safety dashboards that integrate multiple data sources
Using technology helps you collect, analyze, and act on data more effectively.
For more on digital tools in safety programs, see Modern Materials Handling and CCOHS Resources.
Common Pitfalls to Avoid
When you set out to Measure Safety Training Effectiveness, watch for these mistakes:
- Over-reliance on attendance records: Showing up doesn’t mean learning happened.
- Ignoring real-world behavior: Classroom success is meaningless without field application.
- Failing to act on data: Gathering feedback is only valuable if you use it to improve training.
- One-size-fits-all approach: Tailor training and measurement to your specific hazards and workforce.
Continuous Improvement in Safety Training
Effective safety programs don’t treat training as a checkbox. They embrace a cycle of:
- Assessing needs
- Delivering high-quality training
- Measuring effectiveness
- Adapting and improving
By making Measure Safety Training Effectiveness a core part of your safety management system, you reduce risk, improve morale, and demonstrate your commitment to worker well-being.
For more on building effective safety training programs, check out:
- Training and Safety Awareness
- OSHA’s Training Requirements (DoFollow external)
- Canadian Centre for Occupational Health and Safety (DoFollow external)
Final Thoughts on How to Measure Safety Training Effectiveness
Measure Safety Training Effectiveness not as an afterthought but as an integral part of your safety culture.
By using clear objectives, multiple evaluation levels, observation, feedback, and data tracking, you can ensure your training truly protects workers and supports operational excellence.
Measure Safety Training Effectiveness today to build a safer, more resilient workplace for tomorrow.
No comments yet