In many industries, the presence of hazardous gases is an inherent risk that must be effectively managed to ensure the safety and well-being of workers and the protection of facilities.
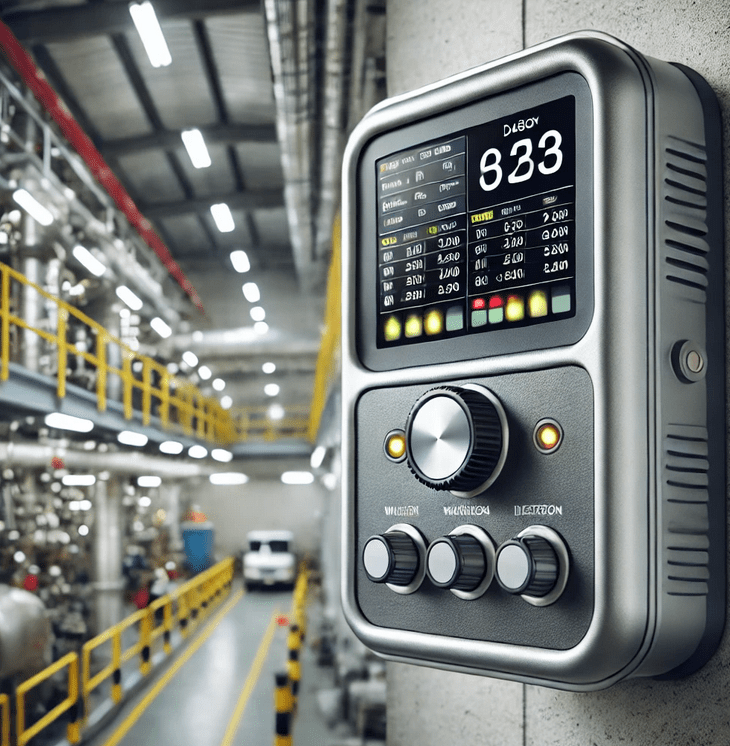
Toxic gases, such as carbon monoxide (CO), hydrogen sulfide (H₂S), ammonia (NH₃), and volatile organic compounds (VOCs), pose serious health hazards when present in high concentrations or through prolonged exposure.
The installation and regular maintenance of toxic gas monitors are essential components of an effective safety management system in workplaces where hazardous gases may be present.
This article explores the critical role that toxic gas monitors play in safeguarding workers and facilities, detailing how they function, their types, and the industries where they are most vital.
1. Understanding Toxic Gas Risks
Toxic gases can originate from various industrial processes, including chemical manufacturing, oil refining, mining, waste treatment, and agricultural operations. These gases can be invisible, odorless, and tasteless, making them difficult to detect without specialized equipment. Exposure to toxic gases can cause immediate health effects ranging from headaches and dizziness to severe respiratory distress, unconsciousness, and even death in extreme cases.
In addition to health risks, toxic gas leaks can lead to facility damage and environmental contamination, resulting in costly repairs and regulatory penalties. For these reasons, continuous monitoring and early detection are key to preventing accidents and ensuring compliance with occupational health and safety regulations.
2. How Toxic Gas Monitors Work
Toxic gas monitors are devices designed to detect the presence of harmful gases in the atmosphere. These monitors use a variety of sensors to measure gas concentrations in real-time, sounding alarms when dangerous levels are detected. The basic working principles include:
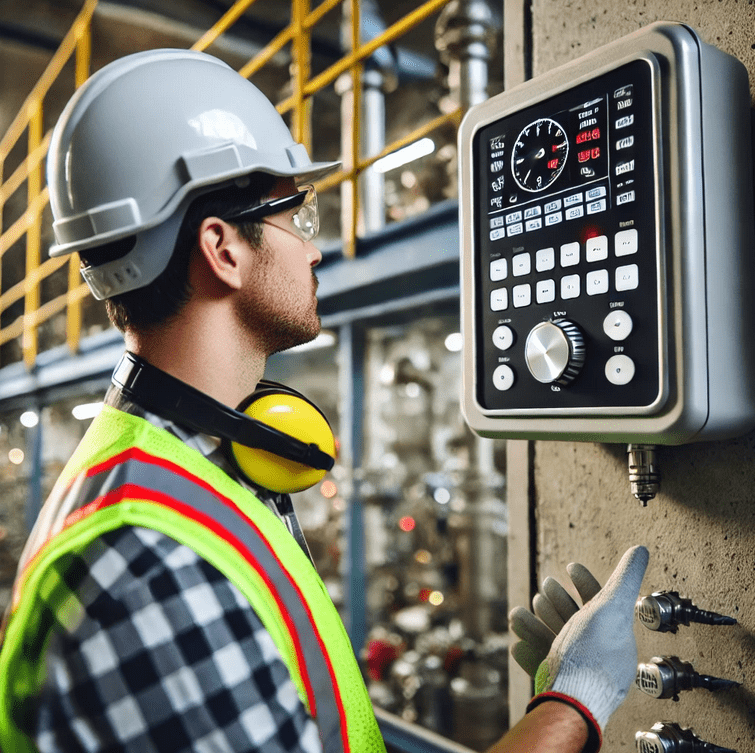
- Electrochemical sensors: Ideal for detecting toxic gases like carbon monoxide and hydrogen sulfide. These sensors rely on chemical reactions between the gas and the sensor’s electrolyte, producing an electric current proportional to the gas concentration.
- Infrared sensors: Used primarily for detecting gases like carbon dioxide (CO₂) and methane (CH₄). These sensors measure the absorption of infrared light at specific wavelengths, correlating with the concentration of the target gas.
- Photoionization detectors (PID): Commonly used for detecting volatile organic compounds (VOCs) and other hazardous gases. PIDs work by ionizing gas molecules with ultraviolet light, creating ions that are detected and measured.
- Metal oxide semiconductor (MOS) sensors: Often employed for detecting combustible gases and VOCs. These sensors change their electrical resistance in the presence of target gases, providing an indication of gas concentration.
Modern gas monitors can be handheld or fixed, portable or permanently installed in facilities, and can be integrated into wider safety systems to trigger automated responses, such as ventilation system activation or shutdown of equipment in case of a leak.
3. Types of Toxic Gas Monitors
Toxic gas monitors come in several forms, each suited to different applications and environments. Understanding these types is crucial for selecting the appropriate equipment for a facility:
- Portable Gas Monitors: These are lightweight, mobile devices worn by workers or carried to different areas for spot checks. They are particularly useful for workers in confined spaces or areas where the atmosphere can change rapidly. Examples include mining, wastewater treatment, and chemical handling.
- Fixed Gas Monitors: Installed in strategic locations, fixed gas monitors provide continuous monitoring of ambient air quality. These monitors are critical in facilities where toxic gas leaks are a constant risk, such as refineries, chemical plants, and manufacturing facilities. They are typically connected to control systems that can initiate emergency responses, such as alarms or ventilation.
- Multi-Gas Monitors: These monitors can detect several types of gases simultaneously. They are often used in environments where multiple toxic gases may be present, offering comprehensive protection. Multi-gas monitors are commonly employed in industries such as oil and gas, where both combustible gases and toxic fumes may be encountered.
- Confined Space Gas Monitors: Designed for environments with limited air circulation, these monitors are essential for protecting workers in enclosed spaces like tanks, sewers, and underground tunnels. Confined space monitors are typically portable and can detect oxygen levels in addition to toxic gases.
4. Industries that Rely on Toxic Gas Monitors
Numerous industries depend on toxic gas monitors to ensure workplace safety and regulatory compliance. Some of the key industries include:
- Oil and Gas: In the oil and gas industry, workers are exposed to various hazardous gases such as hydrogen sulfide (H₂S) and methane. Gas monitors are crucial in detecting leaks during extraction, refining, and transportation processes.
- Mining: Mines often contain hazardous gases like methane and carbon monoxide. Toxic gas monitors are essential for maintaining air quality and preventing explosions.
- Chemical Manufacturing: The use of various chemicals in manufacturing can release toxic gases like ammonia and chlorine. Gas monitors help to detect leaks and ensure that these chemicals are contained safely.
- Agriculture: In agricultural settings, fertilizers, pesticides, and animal waste can produce dangerous levels of ammonia, methane, and hydrogen sulfide. Gas monitors protect workers from exposure during the handling and storage of these materials.
- Waste Management: Facilities that process waste materials, especially sewage, landfill sites, and recycling plants, often deal with toxic gases such as methane, carbon dioxide, and hydrogen sulfide. Gas monitors are used to prevent exposure and to mitigate environmental hazards.
5. The Role of Toxic Gas Monitors in Compliance
Many governments and regulatory bodies, such as OSHA (Occupational Safety and Health Administration) in the United States, require industries to have effective gas monitoring systems in place. These regulations are designed to protect workers and the public from hazardous gas exposure. Gas monitors help companies stay compliant by providing real-time data that can be used for reporting and for immediate response to hazardous situations.
Failure to comply with toxic gas regulations can result in severe penalties, including fines, shutdowns, and legal liabilities. Therefore, installing and maintaining a robust toxic gas monitoring system is not only a safety priority but also a legal requirement in many industries.
6. Maintaining and Calibrating Gas Monitors
To ensure the reliability of toxic gas monitors, regular maintenance and calibration are essential. Sensors can degrade over time due to environmental conditions, gas exposure, or normal wear and tear, which can reduce their accuracy. Calibration involves adjusting the sensor to ensure it provides accurate readings. Depending on the device and industry standards, calibration may need to be performed monthly, quarterly, or annually.
Failure to maintain gas monitors can lead to false readings, putting workers and facilities at risk. A poorly calibrated sensor may fail to detect a dangerous gas concentration or may trigger false alarms, leading to unnecessary evacuations and disruptions.
7. Conclusion
Toxic gas monitors play a critical role in protecting workers and facilities from the dangers posed by hazardous gases. By providing real-time detection and enabling prompt responses to gas leaks or elevated gas levels, these monitors reduce the risk of exposure, health hazards, and environmental damage.
For industries where toxic gases are a constant threat, the implementation of reliable gas monitoring systems is a non-negotiable aspect of workplace safety.
Through proper selection, installation, maintenance, and calibration, toxic gas monitors can save lives, prevent accidents, and ensure compliance with health and safety regulations. Their importance cannot be overstated in any workplace where dangerous gases may be present.
No comments yet