The use of heavy equipment, such as cranes, bulldozers, excavators, and forklifts, is essential in industries like construction, manufacturing, and logistics. However, these powerful machines pose significant safety risks if not operated correctly.
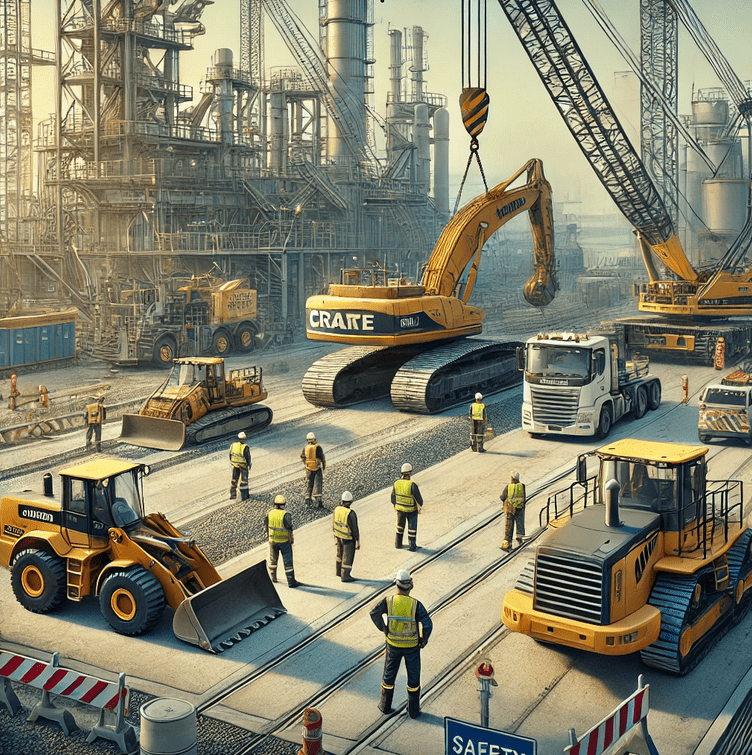
The Occupational Health, Safety, and Environment (OHSE) framework plays a critical role in ensuring that employees working with or around heavy equipment are adequately protected from hazards.
This article delves into the best practices for ensuring safety in heavy equipment operations and explores how employers and workers can mitigate the risks associated with these machines.
1. Hazards Associated with Heavy Equipment
The operation of heavy equipment comes with a variety of hazards that can endanger both operators and bystanders. Some of the most common risks include:
- Struck-by accidents: Workers on foot or operating nearby can be struck by moving equipment or objects dropped by cranes.
- Caught-in/between hazards: Workers can become caught in machinery or pinned between equipment and fixed objects.
- Equipment rollovers: Equipment such as bulldozers and excavators can tip over, posing a serious threat to the operator and nearby workers.
- Falling loads: Cranes and forklifts often lift heavy materials, which can fall if not properly secured, potentially causing fatal injuries.
- Electrocution: Heavy equipment such as cranes can come into contact with overhead power lines, leading to electrocution hazards.
2. OHSE Best Practices for Heavy Equipment Safety
To mitigate the risks associated with heavy equipment, industries must adhere to a variety of OHSE best practices that emphasize prevention, training, and environmental safety.
a. Comprehensive Training Programs
One of the most important elements in reducing accidents is ensuring that operators receive comprehensive and ongoing training. Workers should be trained in:
- Proper operation: Operators must be trained in the specific type of heavy equipment they will be using. This includes understanding the controls, functions, and limitations of the machinery.
- Hazard recognition: Operators and workers on the ground should be able to identify potential hazards, such as unstable terrain, weather conditions, and the presence of power lines.
- Safe load handling: Proper training in how to lift, transport, and unload materials safely is essential to prevent equipment tip-overs and falling objects.
b. Pre-Operation Inspections and Maintenance
Before any heavy equipment is put into use, operators should perform a thorough inspection to ensure the machine is in safe working condition. Key inspection points include:
- Brakes, steering, and tires: Operators should check for proper functionality to prevent equipment malfunctions during operation.
- Hydraulic systems: Inspect hoses, cylinders, and fluid levels to avoid hydraulic failures that can lead to uncontrolled movement.
- Safety devices: Ensure that seatbelts, rollover protection systems (ROPS), and other safety features are in place and functioning correctly.
- Attachments: Verify that all attachments, such as crane hooks or excavator buckets, are secure and in good condition.
Regular maintenance should also be scheduled according to the manufacturer’s recommendations to keep the equipment in peak operating condition and reduce the likelihood of mechanical failure.
c. Site Safety and Organization
Creating a safe work environment for heavy equipment operation is essential to minimize risks for all employees. Best practices include:
- Establishing exclusion zones: Clearly marked zones should be established where heavy equipment is operating, and access should be restricted to essential personnel only.
- Traffic management: In worksites where multiple pieces of heavy equipment are in operation, traffic management plans should be developed to avoid collisions between machines.
- Ground condition assessments: Before operating heavy equipment, the ground conditions should be assessed to ensure that the surface can support the weight and movement of the machinery, particularly for cranes and bulldozers.
d. Communication and Visibility
Effective communication between equipment operators and other workers is crucial for preventing accidents. Standard practices include:
- Two-way radios or hand signals: Operators and spotters should use two-way radios or standardized hand signals to communicate movements and potential hazards.
- High-visibility clothing: Workers on foot should always wear high-visibility clothing, especially in low-light conditions or areas with heavy equipment in motion.
- Backup alarms and cameras: Many modern pieces of heavy equipment come equipped with backup alarms and cameras to help operators avoid running into blind spots or striking other workers.
3. Personal Protective Equipment (PPE) for Heavy Equipment Operators
Even with proper training and safe work environments, operators and nearby workers must wear appropriate personal protective equipment (PPE) to minimize injuries in the event of an accident. Recommended PPE includes:
- Hard hats: Protect workers from falling objects or equipment.
- High-visibility vests: Ensure that workers are easily seen, especially by operators of large machinery.
- Steel-toed boots: Protect feet from being crushed by heavy materials.
- Hearing protection: Many heavy machines generate noise levels that can cause hearing damage, so operators should wear earmuffs or earplugs when necessary.
- Gloves: Provide protection when handling equipment or materials.
4. The Role of Employers in Heavy Equipment Safety
Employers play a critical role in maintaining the safety of heavy equipment operations. Key responsibilities include:
- Developing a safety plan: Employers should have a clear, written safety plan that addresses the specific risks associated with the heavy equipment being used on-site. This plan should include emergency procedures, equipment maintenance schedules, and protocols for safely handling hazardous materials.
- Providing proper training: Employers are responsible for ensuring that all heavy equipment operators are properly trained and certified to use the machinery.
- Ensuring compliance with regulations: Employers must comply with government regulations, such as those outlined by OSHA, which mandate safety standards for heavy equipment use. Regular audits and inspections should be conducted to ensure compliance.
- Offering ongoing safety training: Safety training should be an ongoing process. Refresher courses and updated training materials help keep employees aware of new hazards and evolving best practices.
5. Heavy Equipment Safety Regulations
Various regulatory frameworks exist to ensure the safety of workers operating heavy equipment. In the United States, the Occupational Safety and Health Administration (OSHA) outlines safety regulations for heavy machinery under several key standards, including:
- OSHA Standard 1926.550: This standard covers the safe use of cranes and derricks, requiring employers to inspect and maintain lifting devices and ensure that operators are trained.
- OSHA Standard 1926.601: This standard addresses motor vehicle safety and includes specific rules for heavy equipment used in construction.
- OSHA Standard 1926.651: Focused on excavations, this standard provides guidelines for safe operation in and around trenches and other excavated sites.
6. New Trends in Heavy Equipment Safety
Technology is playing an increasingly important role in improving heavy equipment safety. Some of the latest innovations include:
- Telematics systems: These systems allow for real-time monitoring of heavy equipment, enabling employers to track equipment performance, monitor operator behavior, and receive alerts when maintenance is required.
- Autonomous machinery: While still in its early stages, autonomous heavy equipment is being developed to reduce human error in high-risk environments, particularly in mining and construction.
- Virtual reality (VR) training: VR-based training programs are providing operators with a safe, immersive environment to practice their skills and learn to respond to emergency situations.
The operation of heavy equipment is an integral part of many industries, but it comes with significant risks. By adhering to OHSE best practices, employers can protect workers from injury and ensure the safe operation of machinery.
Comprehensive training, regular equipment maintenance, proper site organization, and the use of personal protective equipment all contribute to a safer work environment. As technology continues to advance, innovations such as telematics and virtual reality training will further enhance safety in the heavy equipment sector.
Safety in the food production industry must always be a top priority. By committing to continuous improvement and adopting these practices, industries can reduce accidents, protect workers, and maintain efficient, productive operations.
No comments yet