- What is Escalation in Occupational Health?
- 1. The Importance of Escalation in Occupational Health
- 2. Common Scenarios Requiring Escalation
- 3. Steps in the Escalation Process
- 4. Best Practices for Effective Escalation
- 5. The Role of Leadership in Escalation
- 6. Measuring the Effectiveness of Escalation Processes
- Prioritizing Escalation in Occupational Health
What is Escalation in Occupational Health?
Escalation in occupational health refers to the process of identifying, addressing, and managing critical health-related issues in the workplace before they become severe.
It involves recognizing early warning signs, implementing appropriate interventions, and involving the necessary personnel to resolve health and safety concerns.
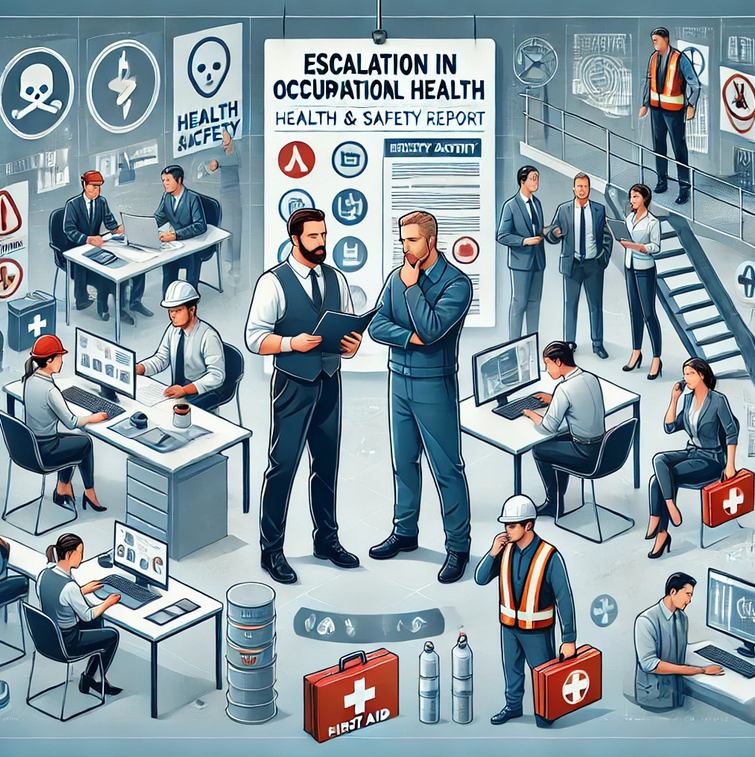
A well-structured escalation process ensures employee well-being, compliance with regulations, and the smooth functioning of workplace operations.
This article explores the importance of escalation in occupational health, common scenarios where escalation is required, and best practices for managing such situations effectively.
1. The Importance of Escalation in Occupational Health
1.1. Protecting Employee Well-being
Early identification and escalation of occupational health issues protect employees from prolonged exposure to hazards and minimize the risk of chronic illnesses or injuries.
1.2. Ensuring Regulatory Compliance
Workplace health regulations, such as those set by OSHA or local occupational health authorities, mandate the prompt addressing of health concerns. Failure to escalate issues can result in penalties and legal repercussions.
1.3. Enhancing Workplace Productivity
Unresolved health issues can lead to absenteeism, reduced morale, and decreased productivity. Escalation ensures timely resolutions, maintaining operational efficiency.
2. Common Scenarios Requiring Escalation
Escalation in occupational health is essential in various workplace scenarios, including:
2.1. Medical Emergencies
- Sudden incidents such as heart attacks, strokes, or severe injuries.
- Action: Call emergency services and notify on-site medical personnel immediately.
2.2. Exposure to Hazardous Substances
- Accidental spills, leaks, or prolonged exposure to chemicals.
- Action: Evacuate the area, use spill kits, and alert the occupational health team.
2.3. Ergonomic Issues
- Repeated employee complaints about musculoskeletal pain due to poor workstation setups.
- Action: Involve ergonomic specialists to assess and redesign the workspace.
2.4. Mental Health Concerns
- Signs of stress, burnout, or workplace bullying.
- Action: Refer the employee to mental health resources or Employee Assistance Programs (EAPs).
2.5. Infectious Disease Outbreaks
- Sudden cases of contagious illnesses like flu or COVID-19.
- Action: Implement isolation protocols, notify public health authorities, and escalate to management.
3. Steps in the Escalation Process
Step 1: Identification
- Recognize the issue early through incident reports, employee feedback, or routine health screenings.
- Use data from wearable devices or workplace monitoring systems to identify trends.
Step 2: Initial Response
- Provide first aid or temporary solutions to contain the situation.
- Inform the immediate supervisor or health and safety officer.
Step 3: Communication and Documentation
- Report the issue to relevant departments, including HR, occupational health, and senior management.
- Maintain detailed records of the incident and initial actions taken.
Step 4: Investigation and Resolution
- Conduct a root cause analysis to determine the underlying problem.
- Implement corrective actions, such as policy changes or equipment upgrades.
Step 5: Follow-Up and Monitoring
- Regularly check on the affected employees or systems to ensure the resolution’s effectiveness.
- Update training programs and safety protocols to prevent recurrence.
4. Best Practices for Effective Escalation
4.1. Establish Clear Protocols
- Develop and communicate a step-by-step escalation plan tailored to the organization’s specific risks.
4.2. Train Employees
- Conduct regular training on recognizing and reporting health concerns.
- Emphasize the importance of timely escalation to reduce stigma around reporting issues.
4.3. Leverage Technology
- Use health monitoring tools, incident reporting software, and automated alert systems to streamline escalation.
4.4. Foster a Culture of Safety
- Encourage open communication where employees feel comfortable reporting concerns without fear of retaliation.
- Recognize and reward proactive behavior in addressing health and safety issues.
5. The Role of Leadership in Escalation
5.1. Empowering Teams
- Leaders must empower employees to take immediate action when health concerns arise.
5.2. Providing Resources
- Ensure access to first aid, medical personnel, and emergency equipment.
5.3. Setting an Example
- Leaders should model adherence to health and safety protocols to reinforce their importance.
6. Measuring the Effectiveness of Escalation Processes
Evaluate the efficiency of escalation protocols by tracking key performance indicators (KPIs):
- Response times to health incidents.
- Reduction in repeat occurrences of similar issues.
- Employee satisfaction with resolution processes.
- Compliance rates with safety regulations.
Prioritizing Escalation in Occupational Health
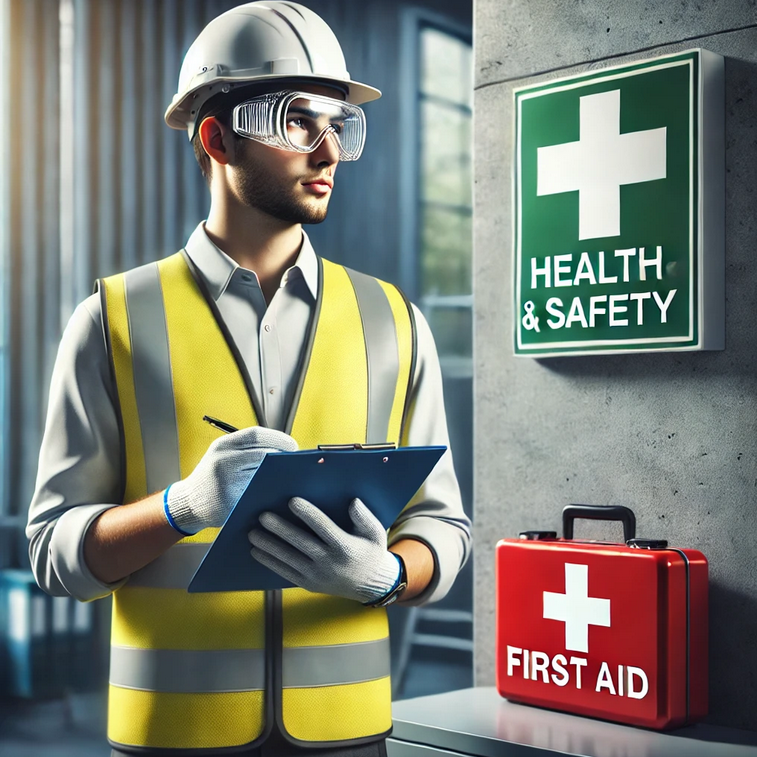
Escalation in occupational health is essential for maintaining safe, healthy, and productive workplaces. By recognizing warning signs, acting promptly, and fostering a culture of safety, organizations can effectively manage health-related challenges.
Leaders, employees, and technology all play vital roles in ensuring escalation processes are efficient and impactful.
For additional resources and expert insights, visit NIOSH, OSHA, or OHSE.ca.
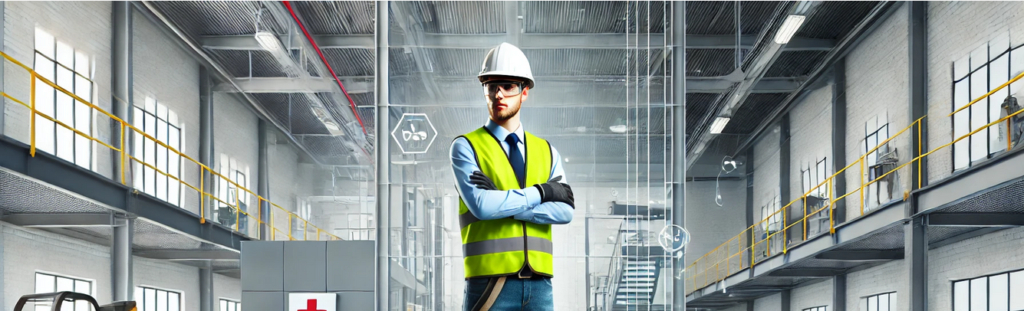
No comments yet