Maintaining good indoor air quality (IAQ) is crucial in any workplace, but it is especially important in manufacturing environments. Dust, which is often produced as a byproduct of various manufacturing processes, can present significant health risks to workers and even damage sensitive machinery.
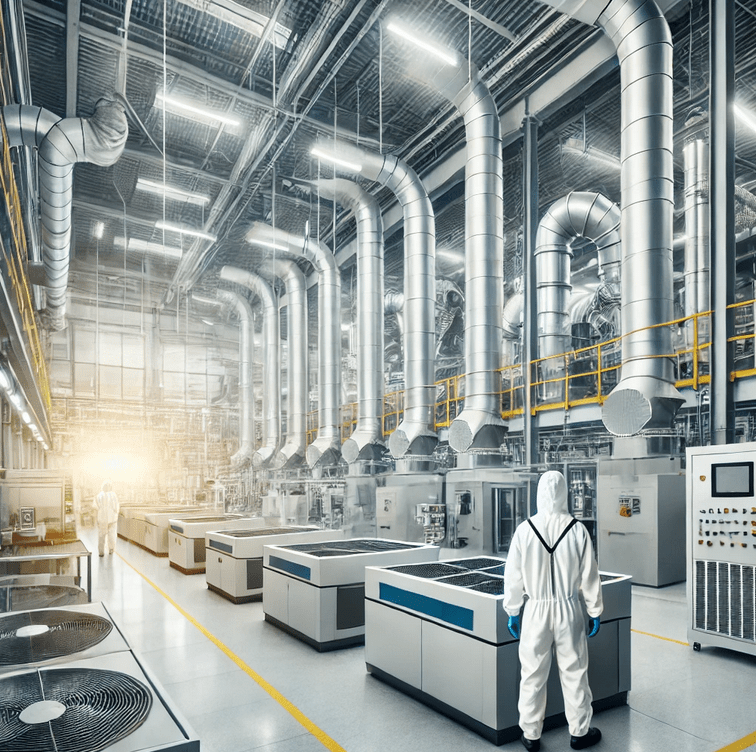
As manufacturing environments become more complex, routine dust testing is a vital component in identifying air quality issues and ensuring compliance with occupational safety and environmental regulations.
In this article, we will explore how dust testing can improve indoor air quality in manufacturing settings, why it is necessary, and how implementing proper dust control strategies can promote worker health, reduce operational costs, and enhance overall productivity.
1. The Importance of Indoor Air Quality in Manufacturing
Indoor air quality in a manufacturing facility can be compromised by various contaminants, including dust, chemicals, fumes, and other airborne particles. Dust, in particular, can have a detrimental effect on both the environment and workers’ health. It can accumulate quickly in confined spaces, reduce air circulation, and contribute to respiratory issues, allergies, and other long-term health concerns.
Dust also poses significant risks to the facility itself. When it settles on equipment, it can affect machinery performance, increasing wear and tear and leading to more frequent maintenance or even equipment failure. Dust that is not properly managed can also contribute to fire and explosion hazards, especially in industries handling combustible materials like wood, metal, or chemicals.
The solution to these problems starts with accurate dust testing and air quality monitoring, which provide insight into potential hazards and inform necessary preventive measures.
2. Understanding Dust Testing
Dust testing involves the collection and analysis of air samples to identify the presence and concentration of airborne dust particles. This is typically done through a variety of methods:
- Gravimetric Sampling: This method involves using filters to capture dust particles from the air. The filters are weighed before and after sampling to determine the dust concentration in the air.
- Optical Particle Counters: These devices count and measure the size of dust particles by using light scattering. They provide real-time data on dust particle levels, offering an immediate overview of air quality conditions.
- Real-Time Dust Monitors: These are automated systems that continuously monitor dust levels in real-time. They can trigger alerts when dust concentrations exceed safe limits, allowing for swift action.
Dust testing results can be compared against occupational exposure limits set by regulatory bodies like the Occupational Safety and Health Administration (OSHA) or the National Institute for Occupational Safety and Health (NIOSH). By regularly testing the dust levels in the workplace, facility managers can ensure compliance with safety standards, prevent worker exposure to harmful particles, and improve overall air quality.
3. Health Risks of Dust Exposure
Dust exposure in manufacturing can lead to a variety of health risks for workers. Some of the key health issues related to dust exposure include:
- Respiratory Issues: Dust particles, especially fine particulate matter (PM2.5 and PM10), can be inhaled deeply into the lungs, leading to conditions such as asthma, bronchitis, and chronic obstructive pulmonary disease (COPD).
- Allergic Reactions: Workers exposed to certain types of dust, such as organic or chemical dust, may develop allergic reactions. Symptoms can include eye irritation, skin rashes, sneezing, and respiratory discomfort.
- Long-Term Health Risks: Prolonged exposure to certain types of dust, like silica dust, wood dust, or asbestos fibers, can increase the risk of more severe health problems, including lung cancer, silicosis, and other occupational diseases.
By conducting routine dust testing, manufacturing facilities can identify hazardous levels of airborne particles early and take steps to protect workers from these health risks.
4. Improving Indoor Air Quality with Dust Control Measures
Once dust testing identifies potential issues with indoor air quality, manufacturers can implement various dust control measures to mitigate the risks and improve air quality:
1. Local Exhaust Ventilation (LEV) Systems
LEV systems are designed to capture dust at its source before it spreads throughout the facility. These systems use hoods, ducts, and filters to trap and remove dust from the air, preventing it from reaching workers or equipment.
2. Air Filtration and Purification
Installing high-efficiency particulate air (HEPA) filters and other advanced air purification systems can significantly reduce the concentration of dust particles in the air. These filters can capture up to 99.97% of particles as small as 0.3 microns, ensuring a cleaner and safer working environment.
3. Regular Housekeeping and Cleaning
Routine cleaning and dust removal are essential to maintaining air quality in manufacturing settings. Dust can accumulate on floors, walls, and machinery if left unchecked, contributing to poor air quality. Implementing strict cleaning protocols helps reduce dust buildup and prevents it from becoming airborne.
4. Humidity Control
Dust tends to remain airborne longer in dry conditions, so controlling humidity levels can help mitigate dust issues. By maintaining optimal humidity (typically between 40-60%), dust particles are more likely to settle, reducing the amount of inhalable dust in the air.
5. Personal Protective Equipment (PPE)
In environments where dust levels cannot be fully controlled, providing workers with PPE such as dust masks, respirators, or protective clothing is essential. This helps reduce their direct exposure to harmful dust particles, safeguarding their health while longer-term control measures are implemented.
5. Regulatory Compliance and Benefits of Dust Testing
Dust testing is not just about improving worker health; it’s also a key element in ensuring regulatory compliance. Government agencies like OSHA and the Environmental Protection Agency (EPA) have stringent guidelines on dust levels in the workplace. Failure to meet these standards can result in fines, penalties, or even facility shutdowns.
By conducting regular dust testing and implementing effective dust control strategies, manufacturing facilities can not only avoid costly regulatory violations but also enjoy numerous operational benefits:
- Enhanced Worker Productivity: Workers in environments with cleaner air tend to be more productive, with fewer sick days related to respiratory issues and other health problems caused by dust exposure.
- Reduced Equipment Downtime: Dust buildup on machinery can cause overheating, mechanical failure, and reduced efficiency. Dust control measures help maintain equipment in good working condition, reducing maintenance costs and downtime.
- Improved Facility Safety: Dust, especially combustible dust, poses a fire and explosion risk. Proper dust testing and control help minimize these hazards, creating a safer workplace for everyone.
Dust testing is a crucial aspect of maintaining indoor air quality in manufacturing facilities. By identifying the sources and levels of dust in the workplace, manufacturers can implement control measures that protect workers’ health, improve equipment performance, and ensure regulatory compliance.
Routine dust monitoring and proactive dust control strategies will help create a safer, cleaner, and more productive manufacturing environment.
Ultimately, investing in air quality testing and dust management can lead to long-term benefits, including improved employee well-being, operational efficiency, and financial savings.
No comments yet