Heavy equipment hazards pose some of the most serious threats to construction workers’ safety. From cranes and bulldozers to loaders and excavators, this machinery plays a vital role in getting the job done — but it also comes with significant risks if not operated, maintained, and supervised correctly.
Understanding these hazards and implementing practical safety strategies can mean the difference between life and death.
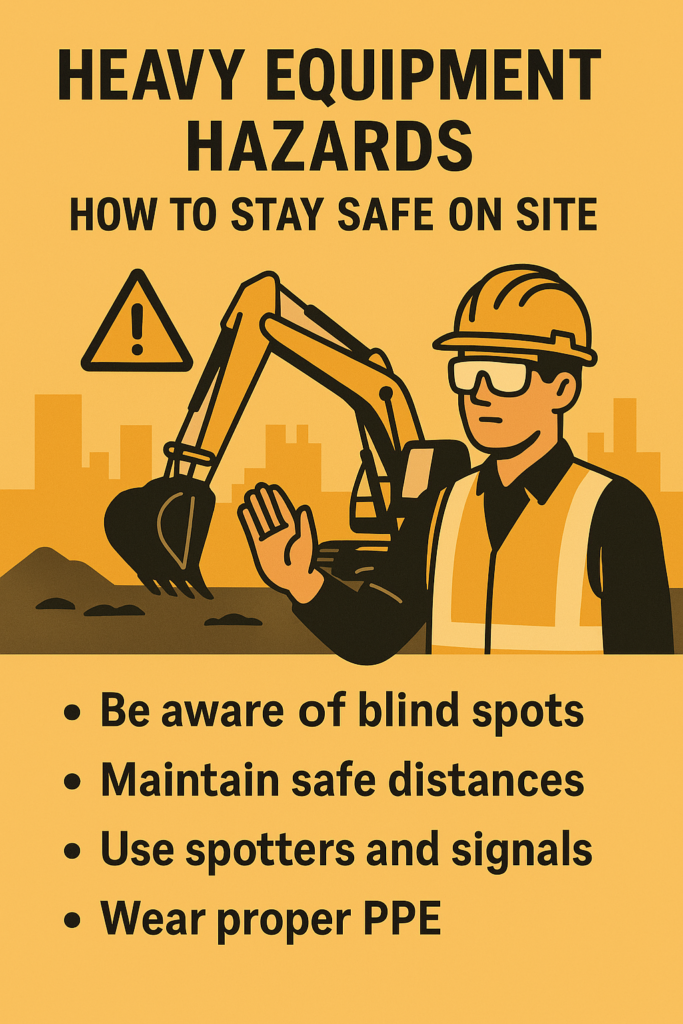
In this article, we’ll explore common heavy equipment dangers, key prevention tips, and compliance standards that protect workers from harm.
- Understanding Heavy Equipment Hazards on Construction Sites
- Types of Heavy Equipment and Their Associated Risks
- Proven Safety Measures for Heavy Equipment Use
- Personal Protective Equipment (PPE) for Heavy Equipment Zones
- Case Study: Preventing a Rollover Incident
- Legal Compliance and Canadian OHSE Standards
- Conclusion: Heavy Equipment Hazards Must Be Taken Seriously
Understanding Heavy Equipment Hazards on Construction Sites
Heavy equipment hazards are not limited to the operators alone. Ground workers, nearby tradespeople, and supervisors can all be affected by poor planning, communication, or equipment failure.

Some of the most common hazards include:
- Struck-by incidents involving swinging booms, rotating parts, or reversing vehicles.
- Caught-in/between accidents, such as getting pinned between machinery and walls.
- Rollovers due to uneven ground or improper loading.
- Machine malfunctions because of poor maintenance or worn-out parts.
- Blind spots that obscure nearby workers and materials.
According to WorkSafeBC, struck-by accidents involving mobile equipment account for a significant portion of fatalities in the construction sector.
Types of Heavy Equipment and Their Associated Risks
Cranes and Hoists
Cranes pose a risk of collapses, dropped loads, and electrical hazards if they come into contact with power lines. Poor rigging or overloading can cause equipment failure.
Excavators and Backhoes
These powerful digging machines present crushing and rollover hazards. Trenching work adds the danger of cave-ins and suffocation.
Loaders and Bulldozers
Used for pushing and lifting heavy materials, these machines can easily run over workers in blind spots or cause tipping on sloped terrain.
Forklifts
Common in both indoor and outdoor construction, forklifts are involved in struck-by, tip-over, and material spill accidents when operated unsafely or with heavy, imbalanced loads.
Proven Safety Measures for Heavy Equipment Use
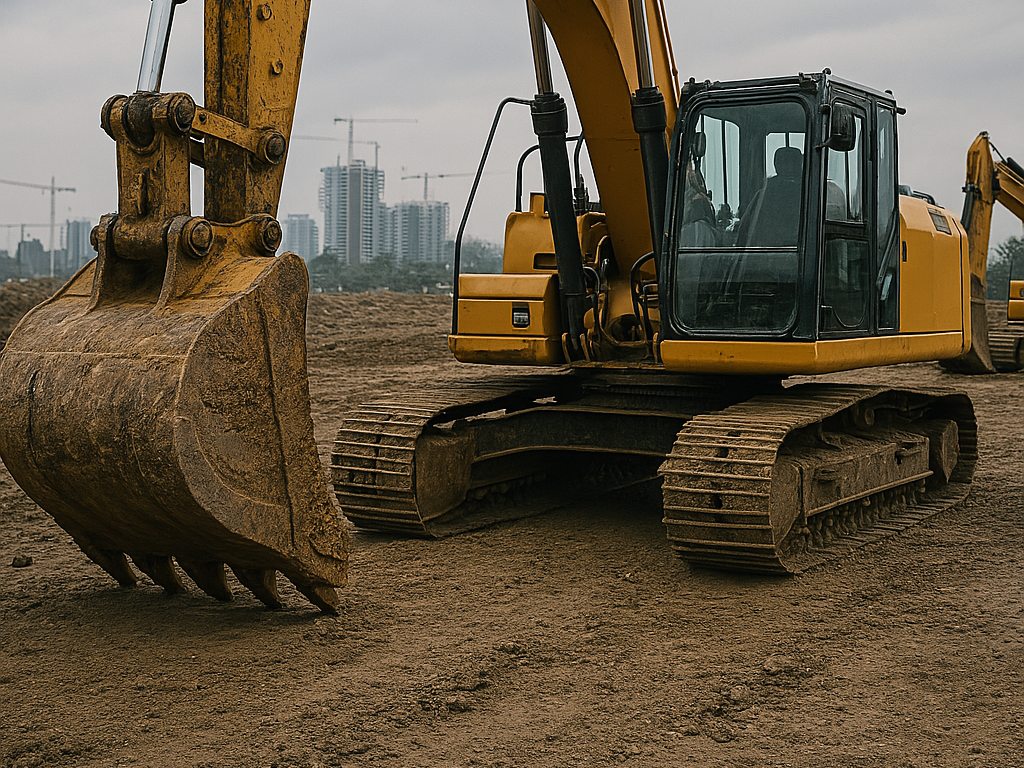
1. Operator Certification and Training
Every operator must be properly trained and certified in the equipment they handle. This includes understanding manufacturer instructions, recognizing site hazards, and maintaining full control during operation.
- Use resources from Canadian Centre for Occupational Health and Safety (CCOHS) to find training standards.
- Employers should implement refresher training programs regularly.
2. Pre-Operation Inspections
A thorough daily equipment inspection is crucial. This includes:
- Checking tires/tracks, hydraulics, brakes, lights, and alarms.
- Ensuring safety guards are intact.
- Reporting and tagging any faulty equipment as “Out of Service.”
3. Use of Spotters and Signalers
On noisy or crowded sites, spotters help guide machinery and ensure blind spots are cleared before any movement. Standardized hand signals should be used to prevent miscommunication.
4. Site Planning and Traffic Control
Establish clear traffic flow routes for equipment and workers. Designated walkways and restricted zones help prevent collisions. Use barriers, cones, and flaggers where necessary.
5. Lockout/Tagout Procedures
If equipment is being serviced, a strict Lockout/Tagout (LOTO) system must be enforced to prevent unexpected startup. This is especially critical during maintenance or repair.
Personal Protective Equipment (PPE) for Heavy Equipment Zones
Construction workers around heavy equipment must wear:
- High-visibility vests to stay visible.
- Hard hats for overhead protection.
- Steel-toe boots to guard against crushing injuries.
- Hearing protection in noisy environments.
- Eye and face protection when debris is present.
Workers should never assume the operator sees them—maintain eye contact or communicate through a spotter.
Case Study: Preventing a Rollover Incident
At a large urban excavation site, a loader operator began work without performing a slope assessment. Mid-task, the machine tipped sideways into a trench, injuring the driver and nearby worker.
Investigation revealed a lack of training and no pre-shift inspection checklist. After this incident, the company introduced mandatory training, slope hazard assessments, and a supervisor sign-off protocol.
This case underlines how heavy equipment hazards can be drastically reduced through planning, training, and supervision.
Legal Compliance and Canadian OHSE Standards
Under Canadian law, including CSA Z150 (Safety Code on Mobile Cranes) and Provincial OH&S Regulations, employers are responsible for:
- Providing proper training.
- Ensuring equipment is inspected and maintained.
- Eliminating or reducing site-specific hazards.
In Ontario, for example, Ontario.ca outlines construction-specific OHSA responsibilities and required controls for mobile equipment.
For more guidance, also visit OHSE.ca – a growing resource for workplace safety across Canada.
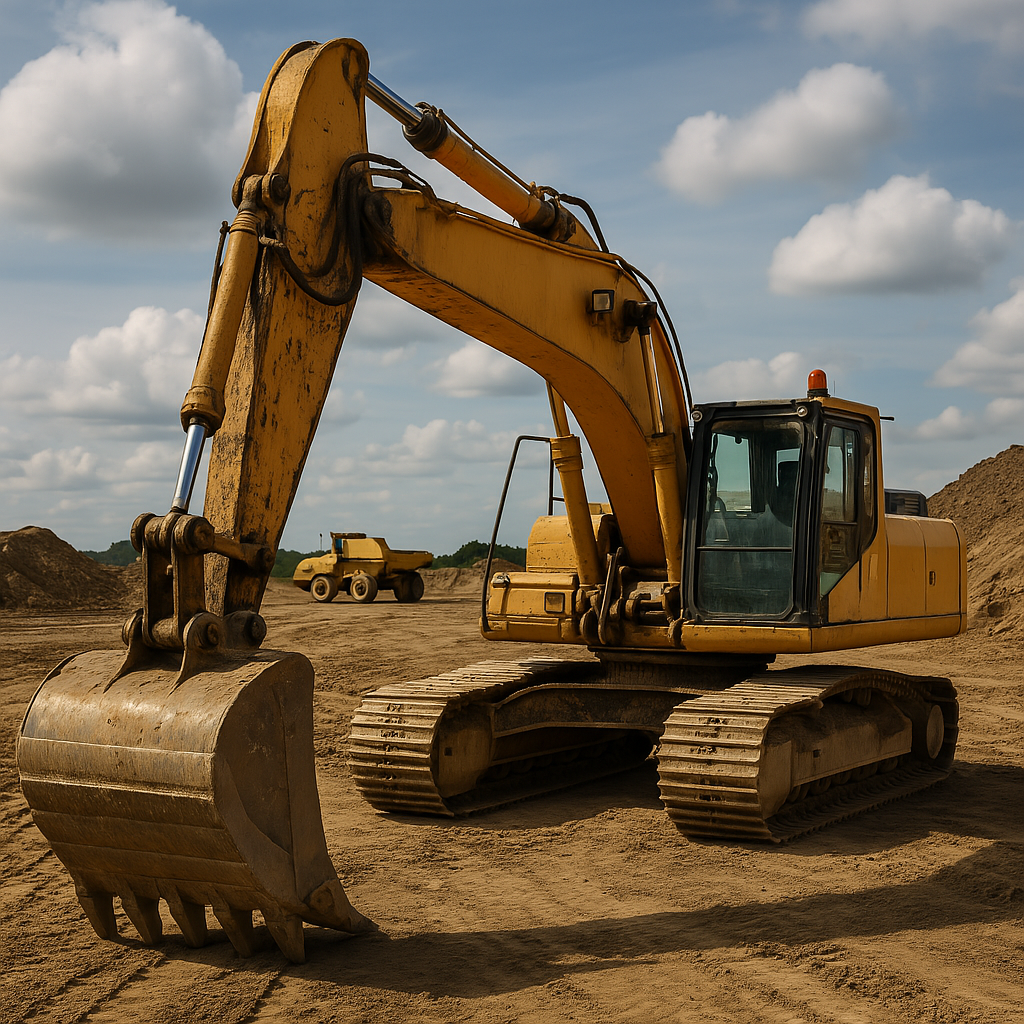
Conclusion: Heavy Equipment Hazards Must Be Taken Seriously
Heavy equipment hazards are among the leading causes of injury and fatality on construction sites. But with robust training, daily inspections, effective communication, and a safety-first mindset, these risks can be mitigated or eliminated entirely.
Investing in safety is not just a legal obligation — it’s a moral one that saves lives and builds a stronger, more resilient workforce.
No comments yet