The surprising benefits of hands-on safety simulations extend beyond simply learning safety protocols—they foster practical skills, enhance decision-making, and prepare workers for real-life challenges in a controlled environment.
In today’s dynamic workplace, traditional safety training often falls short of equipping employees with the tools they need to handle emergencies effectively.
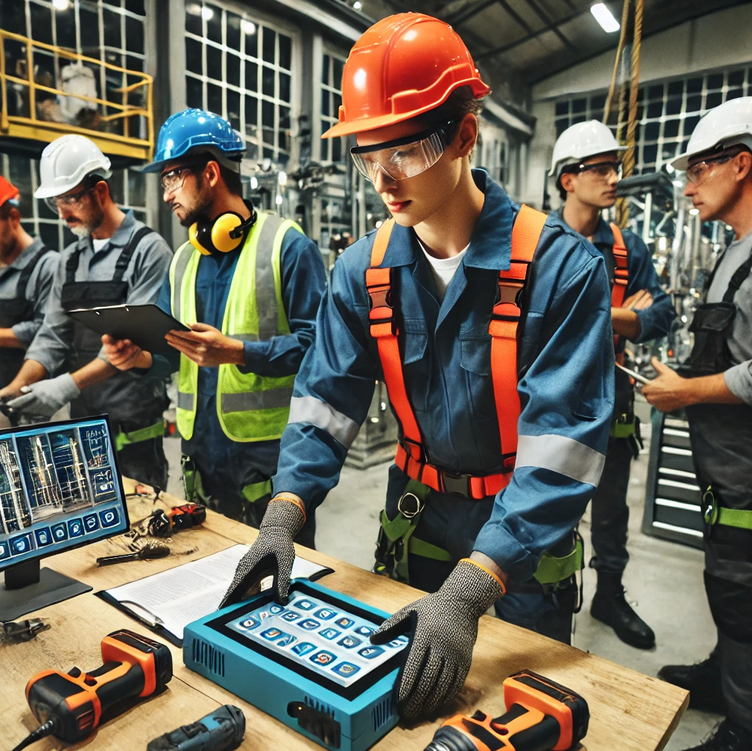
Hands-on safety simulations bridge this gap by creating realistic scenarios where workers can apply their knowledge in practice.
This article explores the numerous benefits of hands-on safety simulations and why they are an essential component of modern occupational health and safety programs.
- 1. What Are Hands-On Safety Simulations?
- 2. The Surprising Benefits of Hands-On Safety Simulations
- 3. Industry Applications of Hands-On Safety Simulations
- 4. How Hands-On Safety Simulations Enhance Workplace Safety
- 5. Challenges in Implementing Safety Simulations
- 6. The Future of Hands-On Safety Simulations
- Conclusion
1. What Are Hands-On Safety Simulations?
Hands-on safety simulations involve interactive training exercises where participants engage in realistic scenarios designed to mimic potential workplace hazards. These simulations may use tools such as virtual reality (VR), augmented reality (AR), or real-world setups to replicate high-risk environments safely.
Key Characteristics:
- Realism: Participants face lifelike situations to build practical skills.
- Interactivity: Simulations require active participation, enhancing engagement.
- Controlled Risks: Hazards are simulated in a safe environment, allowing participants to learn without fear of real danger.
This approach is gaining traction across industries, from construction and manufacturing to healthcare and aviation, as organizations recognize the limitations of traditional lecture-based training methods.
2. The Surprising Benefits of Hands-On Safety Simulations
2.1 Enhanced Learning and Retention
Safety simulations actively involve participants, making the learning process more engaging and memorable. When employees practice responding to hazards, they retain information more effectively compared to passive methods like videos or manuals. For example, practicing emergency drills ensures workers know what to do during a fire, reducing panic and confusion.
- Hands-on experiences tap into experiential learning, reinforcing knowledge through action.
- Workers can immediately apply theoretical concepts, bridging the gap between knowledge and practice.
- Retention rates improve as employees revisit scenarios and refine their skills.
2.2 Improved Decision-Making Skills
Simulations challenge participants to think critically and make decisions under pressure. For instance, a forklift operator might need to navigate through a virtual warehouse with obstacles, honing their judgment in a risk-free environment. This real-time problem-solving experience translates to better decision-making in real-world situations.
- Simulated scenarios replicate the pressures of actual emergencies, helping workers stay composed.
- Participants learn to evaluate risks and prioritize actions, which is invaluable during workplace crises.
- Decision-making becomes second nature, reducing response times in emergencies.
2.3 Enhanced Team Collaboration
Many workplace emergencies require coordinated efforts from teams. Hands-on safety simulations foster teamwork by allowing participants to practice communication and collaboration in high-pressure situations. For example, a healthcare team might practice responding to a patient’s cardiac arrest, with each member executing their role efficiently.
- Team simulations encourage effective communication, ensuring everyone knows their responsibilities.
- Workers develop trust and learn to rely on each other in critical moments.
- Collaboration during simulations builds a strong safety culture within the organization.
3. Industry Applications of Hands-On Safety Simulations
3.1 Construction
In construction, simulations help workers practice tasks like using harnesses during high-altitude work or safely operating heavy machinery. This reduces accidents caused by improper equipment handling or lack of familiarity with safety protocols.
3.2 Healthcare
Healthcare workers use simulations to rehearse life-saving procedures such as CPR, managing trauma cases, or containing infectious diseases. These exercises build confidence and competence, improving patient outcomes.
3.3 Manufacturing
Simulations in manufacturing focus on tasks like handling hazardous chemicals, managing equipment malfunctions, or responding to fires. Workers gain a deeper understanding of how to mitigate risks without disrupting operations.
Learn more about safety simulations in different industries at NIOSH (DoFollow link).
4. How Hands-On Safety Simulations Enhance Workplace Safety
Simulations provide a safe environment for workers to experience potential hazards firsthand. By practicing how to handle emergencies, employees build muscle memory, which helps them react quickly and correctly when faced with real-life dangers. For instance, a warehouse worker trained through a simulation to handle spills can prevent accidents more efficiently.
Supporting Benefits:
- Simulations identify gaps in current safety protocols, enabling organizations to improve training programs.
- They boost worker confidence, reducing hesitation during emergencies.
- Feedback during simulations allows employees to correct mistakes in real-time.
5. Challenges in Implementing Safety Simulations
5.1 Cost and Resources
Setting up simulations, especially with advanced technologies like VR, can be expensive. Organizations may need to invest in equipment, software, and facilitators. However, the long-term benefits, such as fewer accidents and improved productivity, outweigh these initial costs.
5.2 Resistance to Change
Some employees may resist simulations, viewing them as unnecessary or intimidating. Employers must communicate the value of this training and provide supportive environments for learning.
5.3 Technological Barriers
Not all workplaces have access to the technology required for simulations. Organizations can start with simpler setups, such as mock drills, and gradually integrate advanced tools.
Explore how organizations overcome these challenges at EHS Today (DoFollow link).
6. The Future of Hands-On Safety Simulations
6.1 Integration of AI and Machine Learning
Future simulations will use AI to adapt scenarios based on participants’ skill levels and responses, making training more personalized and effective.
6.2 Virtual Reality Advancements
VR technology will become more immersive, enabling employees to experience high-risk situations in greater detail without any physical danger.
6.3 Data-Driven Insights
Simulations will provide detailed analytics on worker performance, allowing organizations to identify strengths and address weaknesses proactively.
Conclusion
The surprising benefits of hands-on safety simulations make them a powerful tool for modern workplace training. By enhancing learning, improving decision-making, and fostering collaboration, simulations prepare workers to handle emergencies with confidence and efficiency.
As industries continue to evolve, adopting hands-on safety simulations is essential for creating safer, more resilient workplaces. Embrace this innovative approach today to protect your workforce and improve your organization’s safety culture.
No comments yet