Workplace injuries, whether minor or severe, require thorough investigation to understand their causes and prevent future occurrences.

While non-critical injuries, such as minor cuts, sprains, or bruises, may not have immediate serious consequences, they still play a significant role in the overall safety and health landscape of an organization. Investigating these incidents is essential to identifying potential hazards, improving safety protocols, and fostering a culture of continuous improvement.
However, investigating non-critical injuries presents its own set of challenges. In this article, we’ll explore these common challenges and provide actionable tips on how to overcome them to ensure a comprehensive and effective investigation process.
- 1. Recognizing the Importance of Non-Critical Injury Investigations
- 2. Encouraging Prompt Reporting of Non-Critical Injuries
- 3. Overcoming the ‘It Was Just a Minor Injury’ Mentality
- 4. Lack of Witnesses for Minor Injuries
- 5. Incomplete Documentation of Non-Critical Injuries
- 6. Addressing Root Causes Instead of Symptoms
- 7. Identifying and Addressing Systemic Issues
- 8. Follow-Up and Corrective Actions
1. Recognizing the Importance of Non-Critical Injury Investigations
One of the primary challenges in investigating non-critical injuries is the tendency to underestimate their importance. Since these injuries may seem minor, both employees and employers may overlook their potential impact on workplace safety.
Why Non-Critical Injuries Matter:
- Early Warning Signs: Minor injuries often signal larger, systemic issues within the workplace that could lead to more serious incidents if left unaddressed.
- Legal and Regulatory Compliance: Failing to investigate non-critical injuries can lead to gaps in documentation and compliance with occupational health and safety (OHS) regulations.
- Workplace Morale and Culture: A workplace that actively investigates and addresses all injuries, regardless of severity, demonstrates a commitment to employee well-being and fosters a positive safety culture.
Tip: Treat every injury with the same level of importance. Ensure that all injuries are documented, investigated, and analyzed, regardless of their severity.
2. Encouraging Prompt Reporting of Non-Critical Injuries
One of the most common challenges in investigating non-critical injuries is that workers may not report them promptly. Employees may feel that minor injuries aren’t worth reporting, or they may fear that reporting an injury could be seen as a sign of incompetence.
Common Reasons for Non-Reporting:
- Perception of ‘Toughness’: Some workers may believe that reporting minor injuries makes them appear weak or incapable of handling the job.
- Fear of Repercussions: Employees might worry about negative consequences, such as being labeled as a complainer or facing retaliation.
- Inconvenience: Workers may perceive the reporting process as too time-consuming, especially for injuries they consider insignificant.
Tip: Encourage a no-blame reporting culture where all injuries, no matter how small, are taken seriously. Simplify the reporting process and educate employees about the importance of reporting injuries for their safety and that of others.
3. Overcoming the ‘It Was Just a Minor Injury’ Mentality
Both employees and employers can fall into the mindset of downplaying non-critical injuries. However, these seemingly minor incidents could reveal unsafe work practices, faulty equipment, or inadequate training.
Examples of Small Injuries with Larger Implications:
- Repetitive Strain Injuries: A minor wrist sprain could be an early indicator of repetitive strain injuries (RSIs) caused by poor ergonomic conditions.
- Minor Slips and Trips: A small bruise from a slip may indicate inadequate housekeeping, leading to serious falls later.
- Cuts and Lacerations: Small cuts may suggest that safety guards on machines are either missing or improperly installed.
Tip: Investigate minor injuries as thoroughly as critical ones. Ask detailed questions and examine the root cause to uncover any underlying issues that may be affecting overall safety.
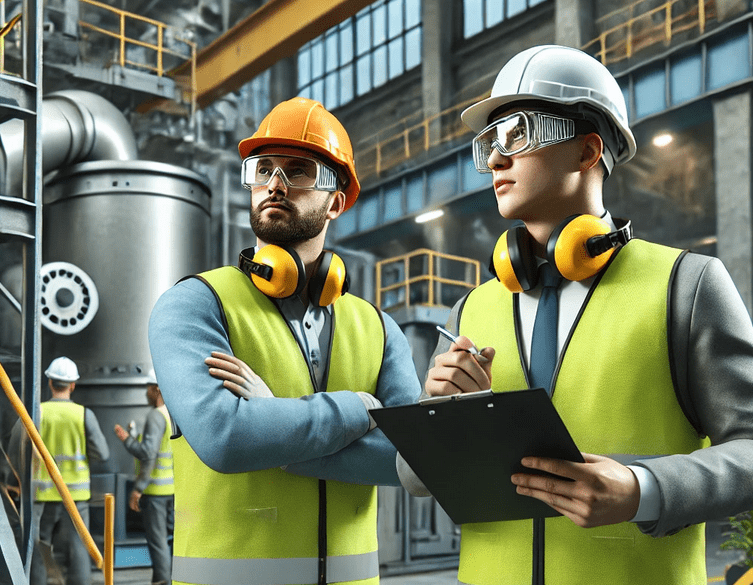
4. Lack of Witnesses for Minor Injuries
Non-critical injuries often occur in isolation, with fewer witnesses than more serious accidents. This makes it challenging to gather firsthand accounts of the event.
Solutions to Overcome Witness Gaps:
- Encourage Reporting at the Time of the Incident: Ensure that workers report injuries as soon as they occur, increasing the likelihood that witnesses are still available to provide relevant information.
- Use CCTV or Surveillance Footage: In areas where surveillance cameras are present, video footage can provide valuable insights into the circumstances of the injury.
- Examine the Environment: Even without witnesses, examining the environment (e.g., slippery floors, faulty equipment) can help identify potential causes.
Tip: Encourage workers to report injuries immediately, whether or not witnesses are present. In the absence of witnesses, focus on environmental factors, past reports, and surveillance footage to reconstruct the incident.
5. Incomplete Documentation of Non-Critical Injuries
Due to the perceived minor nature of non-critical injuries, documentation can sometimes be rushed or incomplete. However, incomplete documentation can lead to gaps in investigation findings, making it difficult to track trends and hazards over time.
Common Documentation Issues:
- Missing Details: Reports may lack critical information about the cause of the injury, contributing factors, or the location of the incident.
- Inconsistent Forms: Different departments or supervisors may use inconsistent reporting forms, making it difficult to track patterns.
- Failure to Document Near-Misses: Near-misses, which are closely related to minor injuries, are often ignored entirely.
Tip: Standardize the documentation process for all injuries, ensuring that every incident, including near-misses, is recorded with sufficient detail. Use checklists or templates to ensure consistency across departments and teams.
6. Addressing Root Causes Instead of Symptoms
Another common issue in investigating non-critical injuries is addressing the immediate symptoms (such as cleaning up a spill) rather than identifying the root causes. Failing to address the root cause of an injury leaves the door open for similar incidents to occur in the future.
Examples of Symptoms vs. Root Causes:
- Symptom: A worker slips and falls because of a wet floor.
- Root Cause: Housekeeping protocols were not followed, leading to a failure to clean up spills promptly.
- Symptom: An employee suffers a minor cut while using a box cutter.
- Root Cause: Workers were not trained on the proper use of cutting tools or the use of personal protective equipment (PPE).
Tip: Conduct a root cause analysis (RCA) for every injury, no matter how minor. Identify the underlying cause, and implement corrective actions to prevent future incidents.
7. Identifying and Addressing Systemic Issues
Minor injuries can sometimes be a symptom of a larger, systemic safety issue in the workplace. Failing to investigate them thoroughly may mean missing the opportunity to address these broader issues.
Signs of Systemic Issues:
- Frequent Occurrence of Similar Injuries: If the same type of minor injury keeps happening, it could indicate a systemic issue such as inadequate safety protocols, improper training, or defective equipment.
- Inconsistent Training: Gaps in safety training could result in multiple employees experiencing similar injuries, even if they are non-critical.
- Lack of Proper Safety Equipment: Consistent minor injuries related to improper use or lack of PPE could highlight the need for better safety gear or stricter enforcement of PPE usage.
Tip: Look for patterns in the types of non-critical injuries reported. Recurrent incidents may indicate systemic issues that need to be addressed with better safety protocols, training, or equipment upgrades.
8. Follow-Up and Corrective Actions
Investigating non-critical injuries should not stop at identifying the immediate cause of the injury. Implementing corrective actions and following up to ensure they are effective is essential to prevent future incidents.
Corrective Actions for Non-Critical Injuries:
- Review Training Programs: Ensure that all employees are properly trained on safety procedures, equipment usage, and hazard identification.
- Implement Housekeeping Protocols: Regular housekeeping to clear walkways, remove hazards, and maintain safe working conditions can prevent slips, trips, and falls.
- Upgrade PPE: If injuries are related to inadequate or faulty PPE, ensure that proper safety gear is provided and that employees know how to use it.
Tip: Always follow up after implementing corrective actions to ensure that they have been effective in preventing similar incidents. Conduct regular reviews of safety protocols to keep them updated and relevant.
Investigating non-critical injuries is just as important as addressing critical injuries in the workplace. By overcoming common challenges such as underreporting, incomplete documentation, and failure to identify root causes, organizations can create a safer working environment for all employees.
Proper investigation and corrective actions for even the smallest injuries not only protect workers from future harm but also demonstrate a commitment to a strong safety culture.
No comments yet